7.2.2 Расчет
передач
7.2.2.1 Определение
мощностей и передаваемых крутящих моментов на валах
Мощности на валах, кВт:

Передаваемые крутящие моменты на валах, кгс · см:
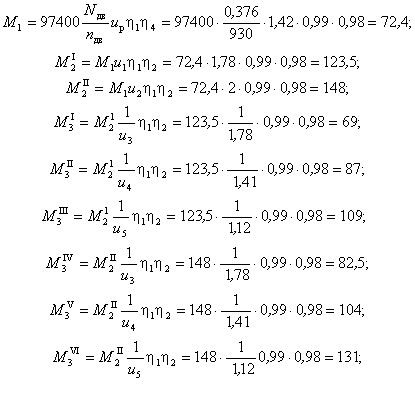
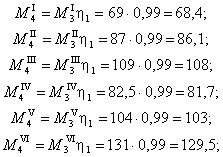
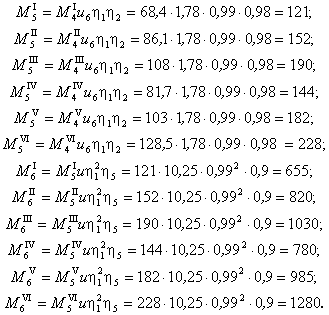
Результаты расчетов сводим в таблицу 7.11.
Таблица
7.11
Номер
валов |
Число оборотов вала п, об/мин |
Передаваемая мощность
N,
кВт |
Передаваемый крутящий момент М, кгс · см |
I |
655 |
0,364 |
72,4 |
II |
380
338 |
0,353 |
123,5
148 |
III |
655
583
520
464
414
380 |
0,343 |
69
82,5
87
104
109
131 |
IV |
380
338
302
270
240
213 |
0,340 |
68,6
81,7
86,1
103
108
129,5 |
|
№
валов |
Число оборотов вала п, об/мин |
Передаваемая мощность
N,
кВт |
Передаваемый крутящий момент М, кгс · см |
V |
380
338
302
270
240
213 |
0,330 |
121
144
152
182
190
228 |
VI |
38
34
30
27,2
24,2
21,6 |
0,270 |
655
780
820
985
1030
1280 |
|
7.2.2.2 Расчет
клиноременной передачи
Исходные данные
Передаваемая мощность – 0,376 кВт.
Частота вращения вала двигателя
nдв
=930 об/мин.
Частота вращения
I вала
коробки подач n1
= 655 об/мин.
Передача осуществляется от асинхронного двигателя с
короткозамкнутым ротором. Пусковая нагрузка до 120% нормальной, рабочая нагрузка
постоянная. Работа в две смены.
Передаточное число ременной передачи:
.
По
таблице 3.44 при передаваемой мощности до 1 кВт и
скорости, до 10 м/с принимаем сечения клиновых ремней О и А. Поскольку заданным
условиям соответствует два сечения ремня, расчет передачи выполняем в двух
вариантах и принимаем в качестве окончательного тот из них, который обеспечит
лучшие показатели передачи (меньшие габариты, большую долговечность и т. д.).
Результаты расчета клиноременной передачи сводим в
таблицу 7.12.
Таблица
7.12
Определяемые величины |
Сечение ремня |
О |
А |
1 |
2 |
3 |
Размеры сечения ремня (таблица 3.36) в соответствии с ГОСТ 1284.1—89
(рисунок 3.38) |
|
|
b0,
мм |
10 |
13 |
bp,
мм |
8,5 |
11 |
h
мм |
6 |
8 |
F
см2 |
0,47 |
0,81 |
Наименьший диаметр шкива
D1min
мм (таблица 3.45) |
70 |
100 |
Диаметр ведомого шкива, мм
D2
= upD1min |
99 |
142 |
Ближайший по ГОСТ 20889—88
D2,
мм |
100 |
140 |
Фактическое передаточное число
D,

ξ
= 0,01 — коэффициент упругого скольжения, принимаемый в соответствии
с рекомендациями |
1,44 |
1,42 |
Расхождение с требуемым
uр,
% |
1,28 |
0 |
Скорость ремня, м/с
 |
3,44 |
5 |
Межосевое расстояние, мм, предварительно принимаем
l0
= 2D1
(таблица 3.46) |
140 |
200 |
Расчетная длина ремня, мм
 |
470 |
660 |
Проверяем условие
 |
вып. |
вып. |
Ближайшая расчетная длина ремня по ГОСТ 1284.1—89 |
500 |
710 |
Уточненное межосевое расстояние, мм
 |
232 |
268 |
Наименьшее допускаемое
межцентровое расстояние, мм
 |
103 |
144 |
Угол
обхвата шкива
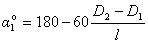 |
172º |
171º |
Условие
 |
вып. |
вып. |
Условие
 |
вып. |
вып. |
Коэффициенты
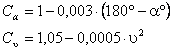 |
0,976
1,0446 |
0,973
1,02 |
Ср
принимаем |
0,9 |
0,9 |
Определяем число пробегов ремня
 |
6,55 |
7,14 |
Принимаем полезное допускаемое напряжение, кг/см2 |
14,5 |
15,1 |
Нагрузка ремня
 |
11,2 |
7,9 |
Число ремней
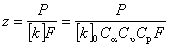 |
3 |
2 |
|
Принимаем ремни сечения О, поскольку число пробегов их
меньше, а, следовательно, долговечность больше, чем ремней сечения А, кроме того,
меньшие габариты передачи. Принимаем класс ремня I (ГОСТ 1284.1-89)
Условное обозначение: Ремень Z(0) – 500 I ГОСТ 1284.1—89.
Давление на валы

Предварительное натяжение новых ремней в первые часы
работы передачи примерно в 1,5 раза больше, чем установившееся рабочее давление.
Поэтому Qmax
≈ 1,5
Q
= 1,5 · 25,3 = 38 кг.
По ГОСТ 1284.1—89 определяем размеры шкива
Dн1
= D1
+ 2h0
= 70+2 · 2,5 = 75 мм, h0
= 2,5 мм, t
= 12 мм,
H =
10 мм, b1
= 8 мм, φ = 34°,
bp
= 8,5,
r =
0,5, b
= 10 мм (рисунок 7.26).

Просмотреть ближе
Рисунок 7.26 - Ведущий шкив клиноременной передачи

Рисунок 7.26 - Ведущий шкив клиноременной передачи. Трехмерная модель
Dн2
= D2
+ 2h0
= 100 + 2·2,5 = 105 мм;
Dвн1
= Dн1 – 2H
= 75 – 2·10 = 55 мм;
Dвн2
=
Dн2
– 2H
= 105 – 2·10= 75 мм.
Ширина шкива, мм
D
= (z
– 1)t
+ 2b1
= (3 – 1) · 12+2 · 8 = 40 мм.
Длина ступицы ведущего шкива
l1СТ
= (1,7 – l,8)d
= 1,815= 1,8 · 1,5 = 27 мм.
Длина ступицы ведомого шкива
l2СТ
= (1,4 – 1,8) d
=1,45 · 15 = 22 мм.
Натяжение ремней производится перемещением двигателя.
Расчет клиноременной передачи заканчивается
вычерчиванием ведущего шкива (рис. 7.26). Отклонения на размеры шкива приняты по
ГОСТ 20889—88.
4.2.2.3
Расчет зубчатых передач
1. Построение графика
нагрузки и определение эквивалентного числа циклов нагружения.
Наиболее нагруженной парой колес в коробке является
пара z2–z3,
для которой передаточное число имеет наибольшее значение (u2=2),
а частота вращения — наименьшую величину
n"2=338
об/мин.
Строим условный график нагрузки для того случая, когда
в зацеплении находятся колеса
z2
– z3
и z6
–
z8
(рисунок 7.27).

Просмотреть ближе
Рисунок 7.27 - График нагрузки
На графике изображена пиковая нагрузка, значительно
превышающая номинальную. Ввиду кратковременности действия этой нагрузки при
расчете зубчатых колес она не учитывается. Пара колес
z2–z3
работает наиболее длительное время – 4 часа в смену. Принимаем число рабочих
дней в году – 250, число смен – 2, срок службы до капитального ремонта – 5 лет.
Тогда номинальное число часов работы за указанный срок службы будет:
T
= 250 · 4 · 2 · 5=10000 ч.
Продолжительность действия отдельных моментов за срок
службы коробки:
при М1 = 1,15 Мн
t1
= 0,25
T
= 0,25 · 10000 = 2500 ч;
при М2 = Мн t2
= 0,5 T
= 0,5 · 10000 = 5000 ч;
при М3 = 0,85 Мн
t3
= 0,25 T
=0,25 · 10000 = 2500 ч.
Эквивалентное число циклов нагружения зубьев колеса за
срок службы коробки:

Показатель степени т при расчете по контактным
напряжениям принимается m
=3. Для нашего случая
, так
как зубчатое колесо воспринимает переменную нагрузку при постоянном числе
оборотов. За наиболее длительно действующий момент принимаем М2
= Mн
= Мmax.
Таким образом:

Эквивалентное число циклов при расчете на выносливость
по изгибным напряжениям определяется по тому же уравнению, но принимается
показатель степени т=6.

2. Выбор материалов.
По таблице рекомендуемых сочетаний материалов для
зубчатых колес и шестерен принимаем: для шестерен
z1,
z2,
z11,
блока шестерен
z8,
z9,
z10,
червяка z13
и шестерни z15
сталь марки 40Х улучшенную с механическими
характеристиками по
таблице 3.3 (при диаметре заготовки до 120 мм и толщине до 60
мм): σв = 9000 – 10 000 кг/см2; σт =8000 кг/см2;
σ–1 =5000 кг/см2, твердость сердцевины НВ = 250 –
280. Для колес z3,
z4,
z5,
z6,
z7,
z12
сталь 50 нормализованную с механическими характеристиками по
таблице 3.3: σв=5800—6200
кг/см2, σт = = 3200 кг/см2, σ–1=2500—2800
кг/см2, твердость сердцевины НВ = 210—230.
Таким образом, выбранные материалы и термообработка их
удовлетворяют желательному соотношению
HBшест
=НВкол + (25÷50).
Для блока зубчатых шестерен выбрана сталь 50
нормализованная, что позволяет производить окончательную обработку зубьев
лезвийным режущим инструментом. Если применять марки сталей с термообработкой до
НВ>350, то для окончательной обработки зубьев потребуется применение
дорогостоящих операций шлифования или притирки зубьев, что в данном случае
нецелесообразно.
3. Определение
допускаемых напряжений.
Коэффициент режима нагрузки при расчете по контактным
напряжениям

где
N0 — базовое
число циклов нагружения. Для сталей при НВ<350
N0=
1 · 107 (см.
п. 3.17).
Так как Nц.эк>N0,
то kрк< 1, поэтому
принимаем kрк
= 1 (см. п.
3.14).
Допускаемые контактные напряжения определяются по
уравнению:
[σ]к = (28 ÷ 30)
HBmin
kрк
(для нормализованных и улучшенных сталей при НВ<350).
Для шестерни [σ]к = 28·250 = 7000 кг/см2.
Для колеса [σ]к = 28·210 = 5880 кг/см2.
В данном случае расчет на контактную прочность будем
производить по колесу, так как [σ]к.кол < [σ]к.шест,
хотя возможны случаи, когда [σ]к.кол> [σ]к.шест.
Коэффициент режима нагрузки при расчете по изгибным
напряжениям для улучшенных и нормализованных сталей при НВ<350
(см.
п 3.14)

Так как
Nц.эк
> N0,
то kри
< 1, поэтому принимаем kри
= 1 (см.
п 3.14).
Коэффициенты режима нагрузки
kрк и
kри,
отражающие влияние числа циклов на выносливость зубьев по изгибным и контактным
напряжениям, для всех других более быстроходных колес коробки окажутся меньшими.
Поэтому расчет всех передач производится при коэффициентах режима
kрк = 1 и
kри
= 1. Допускаемые напряжения изгиба при работе двумя сторонами зуба (передача
реверсивная) определяем по следующим данным: коэффициент безопасности для
нормализованных и улучшенных колес [n]
= 1,5, эффективный коэффициент концентрации напряжений у корня зуба
kσ
=1,8 (см.
п 3.14).
Предел выносливости сердцевины для материалов колес
при симметричном цикле
σ–1
= 0,24 σ
врс +
600 кг/см2.
Для шестерни
σ–1
= 0,24 · 9500 + 600 = 2880 кг/см2.
Для колеса
σ–1
=0,24 · 6000 + 600 = 2040 кг/см2.
Допускаемые напряжения изгиба при симметричном цикле
нагружения определяем по уравнению
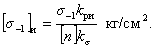
Для шестерни
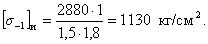
Для колеса
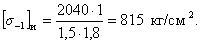
4. Определение
коэффициента нагрузки.
Для предварительных расчетов при несимметричном
расположении колес на валах принимаем коэффициент нагрузки
k
= 1,5 (см.
п. 3.16).
5. Определение
коэффициента ширины венцов колес.
По рекомендациям (см.
п.
3.12)
принимаем для колес, включаемых осевым перемещением, коэффициент ширины колес ψa
= 0,15, а для колес, находящихся в
постоянном зацеплении, ψа = 0,18.
6. Определение
межосевых расстояний.
Расчет выполняется для наиболее тяжело нагруженных пар
колес, для которых передаточное число наибольшее, а частота вращения колеса
наименьшая. Такими являются колеса: пара
z2—z3,
пара z6—z8
и пара
z11—z12.
Межосевое расстояние из условия контактной
прочности определяем по уравнению:

Расчетный модуль
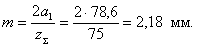
По ГОСТ 9563—60 принимаем
m
=2,5 мм. Уточненное делительное межосевое
расстояние для первой двухваловой передачи:
.
Делительное межосевое расстояние между вторым и
третьим валами

Расчетный модуль
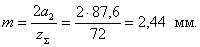
По ГОСТ 9563—60 принимаем
m
=2,5 мм. Уточненное делительное межосевое
расстояние для второй двухваловой передачи:
.
Делительное межосевое расстояние между четвертым и
пятым валами

Расчетный модуль
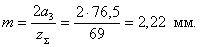
По ГОСТ 9563—60 принимаем
m
=2,5 мм. Уточненное делительное межосевое
расстояние для третьей двухваловой передачи
.
7. Определение ширины
венцов зубчатых колес.
Определяем ширину венцов зубчатых колес:

определим
из условия равнопрочное по уравнению
;

Определяем ширину зубчатых венцов колес
z6
и z8:

определяем
из условия равнопрочности:


Для облегчения переключения зубчатые венцы колес
z4,
z5,
z6
и блока колес z8,
z9,
z10
выполняются с бочкообразной формой рабочих торцов зубьев. В результате рабочая
длина зуба уменьшается на величину
b'
= h·tg
15° (рисунок 7.6),
где
h
— высота зуба.
В нашем случае
b'
=2,25·2,5·0,268 = 1,5 мм.
Поэтому окончательная ширина венцов зубчатых колес
будет:
bZ6
=
bZ8
= 13,5 + 1,5 = 15 мм;
bZ4
=bZ10
= 13 + 1,5 = 14,5 мм. Принимаем 15 мм;
bZ5
=
bZ9
= 12,1 + 1,5 = 13,6 мм. Принимаем 14 мм.
Ширина венцов зубчатых колес
bZ11
и
bZ12
bZ11
=
bZ12
=0,18·86,25 = 17,2 мм. Принимаем 18 мм.
8. Определение
степеней точности колес.
Степень точности зависит от окружной скорости
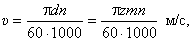
которую вычисляем для зубчатых колес, имеющих
наибольшую скорость. Такими колесами в первой двухваловой передаче являются
z1
и
z2:

По
Приложению 19 принимаем 7-ю степень точности для
колес z1
z2,
z3
и z7.
Во второй двухваловой передаче наибольшую скорость имеют колеса
z4,
z5,
z6.

По той же таблице принимаем 7-ю степень точности для
колес z4,
z5,
z6
и блока шестерен
z8,
z9,
z10.
9. Уточнение
коэффициента нагрузки
В наиболее неблагоприятных условиях по концентрации
нагрузки вдоль зуба находятся две пары колес
z1–z7
и z2–z3
по следующим причинам: для этих пар колес отношение
b/d
наибольшее, а именно
(таблица
7.13).
Таблица
7.13 - Сводная таблица
основных параметров колес
Число зубьев
колес |
Модуль,
мм |
Диаметры,
мм |
Ширины
зубчатых
венцов, мм |
Отношение
 |
d |
dа |
df |
z1
= 27 |
2,5 |
67,5 |
72,5 |
61,25 |
15 |
0,222 |
z2
= 25 |
2,5 |
62,5 |
67,5 |
56,25 |
17 |
0,272 |
z3
=
50 |
2,5 |
125 |
130 |
118,75 |
17 |
0,136 |
z4
= 42 |
2,5 |
105 |
110 |
98,75 |
15 |
0,143 |
z5
=
38 |
2,5 |
95 |
100 |
88,75 |
14 |
0,147 |
z6
=
46 |
2,5 |
115 |
120 |
108,75 |
15 |
0,130 |
z7
= 48 |
2,5 |
120 |
125 |
113,75 |
15 |
0,125 |
z8
= 26 |
2,5 |
65 |
70 |
58,75 |
15 |
0,23 |
z9
=
34 |
2,5 |
85 |
90 |
78,75 |
14 |
0,165 |
z10
=
30 |
2,5 |
75 |
80 |
68,75 |
15 |
0,200 |
z11
= 25 |
2,5 |
62,5 |
67,5 |
56,25 |
18 |
0,29 |
z8
= 44 |
2,5 |
110 |
115 |
103,8 |
18 |
0,164 |
|
Указанные пары зубчатых колес расположены
несимметрично относительно опор. Исходя из этих соображений, коэффициенты
концентрации нагрузки определим для передач
z1—z7,
z2—z3.
Коэффициент концентрации нагрузки, приближенно
отражающий влияние на прочность зубьев неравномерности распределения нагрузки по
длине контактной линии, происходящей за счет деформации валов, принимаем по
таблице 3.14, как для прирабатывающихся пар колес
(твердость зубьев НВ<350):

В связи с небольшим колебанием нагрузки принимаем φ =
0,6. По
таблице 3.15 принимаем Θ =
1,4. Тогда
kкц
= 1,4 (1 – 0,6) + 0,6= 1,16.
Подсчеты, выполненные по данным указанных таблиц,
показывают, что значения kкц
для обеих пар колес одинаковы. Коэффициент динамичности принимаем по
таблице 3.13. Он оказывается одинаковым для всех передач
kд
=1,1.
Уточненное значение коэффициента нагрузки

А. С. Проников [64] рекомендует не учитывать
дополнительных динамических нагрузок при расчете тихоходных зубчатых передач
коробок подач. В примере дано определение
kд
с учебной целью. Значение его оказывается небольшим, мало влияющим на величину
расчетной нагрузки.
10. Проверка зубьев
колес на выносливость по контактным и изгибным напряжениям.
В связи с тем что уточненное значение коэффициента
нагрузки отличается от ранее принятого ориентировочного значения
k
=1,5 в меньшую сторону, то рабочие напряжения
оказываются меньше допускаемых. Следовательно, проверку на выносливость по
контактным напряжениям производить не нужно, так как условие прочности
выполнено. (В предварительном расчете при ориентировочно принятом коэффициенте
нагрузки k
=1,5 это условие выполнялось, значит, в
нашем случае при k
= 1,28 оно будет тем более выполняться.)
Проверка зубьев шестерен и колес на выносливость по
напряжениям изгиба производится по уравнению
.
Для шестерен и колес 7-й степени точности коэффициенты формы зуба принимаем по
таблице 3.7 (для шестерен и колес
при
С*
= 0,25). Для сравнительной оценки изгибной прочности зубьев шестерен и колес
вычислим произведения [σ—1]и у.
Результаты вычислений сводим в таблицу 7.14.
Таблица
7.14 - Значения произведений
[σ—1]и у
|
z1 |
z2 |
z3 |
z4 |
z5 |
z6 |
z7 |
z8 |
z9 |
z10 |
z11 |
z12 |
Число зубьев |
27 |
25 |
50 |
42 |
38 |
46 |
48 |
26 |
34 |
30 |
25 |
44 |
[σ—1]и
у |
0,408 |
0,400 |
0,458 |
0,446 |
0,440 |
0,453 |
0,456 |
0,404 |
0,429 |
0,417 |
0,400 |
0,450 |
y |
462 |
452 |
373 |
364 |
359 |
370 |
372 |
457 |
485 |
472 |
452 |
367 |
|
Из сопоставления произведений у [σ—1]и
и других величин, входящих в уравнение прочности σи < [σ—1]и
у, видно, что необходимо проверить изгибную прочность колес или шестерен
шести пар зацеплений z1—z7,
z2—z3,
z4—z10,
z5—z9,
z6—z8,
z11—z12:

Условия изгибной прочности выполняются.
В уравнения прочности входят частоты вращения колес,
каждое из которых в общем случае может вращаться с разными скоростями. В
уравнения подставляем наименьшие частоты вращения, принимая их по графику частот
вращения.
Анализ произведений у [σ–1]и
показывает, что парные зубчатые колеса не отвечают желательному равенству
произведений y
[τ–1]и шестерен и парных
им колес, хотя эта разница небольшая. Наибольшая разница произведений у пары
z5—z9.
Для уравнивания этих произведений применим колеса со смещением так, чтобы
коэффициент суммы смещений
xΣ
= x1
+ x2
= 0.
11. Расчет
геометрических параметров зубчатых колес
z5
и
z9
со смещением.
Принимаем при заданном межосевом расстоянии а =
aW
= 0,5 (z5
+ z9)
m
коэффициенты смещения для шестерни х1
= 0,3, для колеса х2= – 0,3. Путем интерполяции
находим коэффициенты формы зуба у (табл. 3.7) и вычисляем произведения [σ–1]и·у,
которые указаны в таблице 7.15.
Таблица
7.15
|
x |
y |
[σ–1]и·у |
z5=38
z9
= 34 |
+0,3
–0,3 |
0,490
0,358 |
400
404 |
|
Из
сопоставления произведения [σ–1]и·у видно, что
выбранные коэффициенты смещения практически обеспечивают изгибную равнопрочность
колес z5
и z9.
Результаты расчетов геометрических параметров колес
z5
и z9
сводим в таблицу 7.16.
Таблица
7.16
Определяемые величины |
z5 = 38 |
z9
=
34 |
Величина смещения, мм Х=хт |
+0,75 |
–0,75 |
Передаточное число
 |
|
Межосевое расстояние, мм 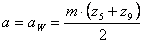 |
90 |
Делительный диаметр, мм
d5,
9 =
mz5,
9 |
95 |
85 |
Начальные диаметры

 |
95 |
85 |
Диаметр вершин зубьев, мм
da5, 9 =
d5,
9+ 2·(
ha*
+
x5,
9)·т |
101,5 |
88,5 |
Диаметр впадин, мм
da5,
9 =
d5,
9 + 2 (ha*
+ С* –
x5,
9)·т |
90,25 |
77,25 |
Основной диаметр, мм
da5
9
= d5
9
cos
a
|
89,26 |
79,89 |
Угол
профиля в точке на концентрической окружности диаметра
dx = d
+ 2m z
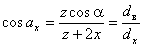 |
0,925 |
0,856 |
Угол
ах |
22°24' |
17°03' |
Расчетное число зубьев в длине общей нормали
 |
4,13
|
3,73
|
Принимаем |
5 |
4 |
Длина общей нормали, мм
W
= [π (zn
— 0,5) + 2х tg
α
+
z
inv
α] m
cos
α |
34,94 |
24,19 |
|
12. Проверка качества
зацепления по геометрическим параметрам:
а) Проверка отсутствия подрезания зуба
Коэффициент наименьшего смещения
.
Для
z5
= 38; xmin=
–1,22; для z9
= 34; xmin
= –0,99.
Так как в нашем случае
xz5
= 0,3 > хтin
и
xz9
= –0,3 >
xmin,
то подрезания зубьев происходить не будет.
б) Проверка отсутствия интерференции зубьев
Радиус кривизны в граничной точке профиля зуба

Угол профиля зуба в точке окружности вершин αа

Для z5
=
38

Для z9
=
34

Радиус кривизны активного профиля зуба в нижней точке:
колеса z5
ρр =
aW·sinα
– 0,5dB9tg
αB9
= 90·0,342 – 0,5·79,89·0,475 = 11,78 мм;
шестерни
z9
ρр =
aW
sin
α
– 0,5dB5
tgαa5
= 90·0,342 – 0,5·89,26·0,543 = 6,55 мм.
Радиус кривизны в граничной точке профиля зуба ρl:
колеса
z5

шестерни
z9

Так как у колеса
z5ρ
< ρр и у шестерни z9ρ
< ρр, интерференция зубьев отсутствует.
в) Проверка коэффициента перекрытия
Коэффициент торцевого перекрытия

что больше допустимого εα = 1,2 (см.
п. 3.14).
Проверка толщины зуба на поверхности вершин
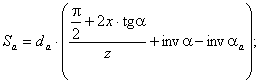
колеса
z5

шестерни
z9

что больше допустимого значения
Sa
= 0,3m
= 0,3·2,5 = 0,75 мм.
7.2.2.4 Расчет реечной
передачи
Скорость поступательного движения суппорта

где
n6
– об/мин реечной шестерни;
т – модуль реечной шестерни. Предварительно
принимаем m
=3 мм, а число зубьев реечной шестерни
z15
= 10.
Результаты расчета сводим в таблицу 7.17.
Таблица
7.17
n,
об/мин |
21,6 |
24,2 |
27,2 |
30 |
34 |
38 |
υ,
м/с |
0,0339 |
0,0380 |
0,0427 |
0,0472 |
0,0534 |
0,0597 |
|
По табл. 3.2 принимаем для реечной шестерни сталь 40Х
с механическими характеристиками (таблице 3.3) σв
= 10000 кг/см2, σт =8000 кг/см2.
Твердость сердцевины НВ = 250–280. Твердость
поверхности после закалки т. в. ч.
HRC =
50–55 (таблице 3.3).
Допускаемое напряжение изгиба при симметричном цикле
нагружения с учетом концентрации напряжений

где
kσ
—эффективный коэффициент концентрации напряжений у корня зуба. При поверхностной
закалке т. в. ч. kσ
=1,2;
kри—
коэффициент режима нагрузки. При расчете по изгибным напряжениям
kри
= 1;
[n]
– коэффициент безопасности, для шестерен с поверхностной закалкой т.в.ч. [n]
= 1,7(см.
п. 3.14);
σ–1 — предел выносливости
материала шестерни z15
на изгиб при симметричном цикле нагружения
при поверхностной закалке т. в. ч.
σ–1 = 0,34·σврс + 800 =
0,34·10 000 + 800 = 4200 кг/см2.
Допускаемое напряжение
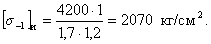
Определяем наименьший коэффициент смещения
xmin,
при котором отсутствует подрезание зуба,
,
где

.
Исходя из необходимости повышения изгибной прочности
зубьев реечной шестерни, принимаем х = 0,6.
Проверяем зубья шестерни на прочность по напряжениям
изгиба:

По данным
п. 3.14 принимаем γ =
2,0, где Р – окружное усилие на реечном колесе (тяговая сила подачи),
Р = 436 кг; k
— коэффициент нагрузки;
kкцkд,
где kкц
— коэффициент концентрации нагрузки. При поверхностной твердости НВ<350, хотя бы
для одного из колес зубчатой пары:
.
Θ в принимаем по
таблице 3.15.
При консольном расположении зубчатого колеса и отношении
b/d=
1 ÷ 1,6; Θ = 1,3.
По данным
п. 3.16 принимаем φ =
0,6, kд
= 1 — коэффициент динамичности (таблица
3.12).
Тогда коэффициент нагрузки
k
= kкцkд
= [1,3·(1 – 0,6) + 0,6]·1 = 1,12,
y
— коэффициент формы зуба при х = 0,6;
y
= 0,530 (таблице 3.7);
b
– ширина зубчатого венца. Обычно
b =
ψm·т=10
· 3 = 30 мм.
Тогда

Условие прочности на изгиб выполняется. Определяем
основные параметры передачи.
Величина смещения
Х = хт =
0,6·3= 1,8 мм.
Делительный диаметр:
d15
= т·z15
= 3·10 = 30 мм.
Начальный диаметр:
dW15
= d15
= 30 мм.
Диаметр вершин зубьев:
da15
=
d15
+ 2 (
ha*
+ х) т = 30 + 2 (1 + 0,6)·3 = 39,6
мм.
Диаметр впадин:
df15
=
d15
– 2 ( ha*
+ С* – х) т = 30 – 2 (1 + 0,25 – 0,6)·3 = 26,1 мм.
Основной диаметр:
dв15
=
d15
cos
α
= 30·0,9396 = 18,188 мм.
Высота головки зуба рейки:
ha
= (h*
– х)·т = 3(1 – 0,6)= 1,2 мм.
Полная высота зуба рейки:
h
= 2,25·m
= 2,25·3 = 6,75 мм.
Коэффициент торцевого перекрытия:

Угол
профиля в точке на концентрической окружности диаметра
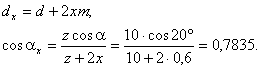
Угол
αx
= 38°06'.
Расчетное число зубьев в длине общей нормали

Принимаем
zп
= 3.
Длина общей нормали
W
= [π.·(zп
– 0,5) + 2·х·tg
α +
z·inv
α]·m·cos
α = [3,14·(3 – 0,5) + 2·0,6·tg
20° + 10·inv
20°]·3·cos
20° = 23,82 мм.
7.2.2.5
Расчет червячной передачи
Для значительного понижения скоростей в цепи подач
применяем червячную передачу, позволяющую осуществить большое передаточное
число при малых габаритах, обеспечить бесшумность работы и плавность хода.
1. Геометрический
расчет червячной передачи.
Передаточное число

где zч
и zк
— число заходов червяка и число зубьев колеса;
пч
и
nк
— частоты вращения червяка и колеса;
Мч
и Мк — крутящие
моменты на валах червяка и червячного колеса;
η — КПД
червячной передачи.
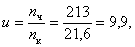
По
таблице 3.16 принимаем
u
= 10 (стандартное передаточное число червячной
передачи). Число заходов червяка и число зубьев червячного колеса принимаем
zч=
4 и zк
= 40, что соответствует стандартным значениям. Предварительно задаемся величиной
(число
модулей в диаметре делительного цилиндра червяка), равной
q
= 12.
Принимаем: коэффициент высоты зуба
f0
= l;
коэффициент радиального зазора С0 = 0,2. Высота головки
h'=ms.
Высота ножки зуба
h"
=
1,2ms.
Радиальный зазор С = 0,2ms.
2. Материал и
термообработка
Выбираем венец червячного колеса из безоловянистой
бронзы БРАЖ 9–4Л (отливка в кокиль) (таблица 3.25),
имеющей предел прочности σв = 5000 кг/см2. Для червяка
принимаем сталь 40Х с поверхностной закалкой витков червяка до
HRC =
50–55, с последующим шлифованием и полированием профиля червяка.
3. Расчет передачи на
выносливость по контактным напряжениям и напряжениям изгиба.
В большинстве случаев проектный расчет червячных
передач производится по контактным напряжениям. Расчет по напряжениям изгиба
выполняется как проектный лишь в тех случаях, когда число зубьев колеса
zк
>90, и поэтому изгибная прочность зубьев
может оказаться недостаточной.
По
таблице 3.27 при твердости червяка
HRC>45
принимаем [σ–1]и = 840 кг/см2. Поскольку червяк
закаленный, а витки его шлифованы и полированы, то можно увеличить допускаемое
напряжение на 25%. Тогда
[σ–1]и = 840·1,25= 1050 кг/см2.
Для твердой бронзы АЖ9–4Л допускаемое контактное
напряжение выбираем по
таблице 3.25 из условия сопротивления заеданию в
зависимости от скорости скольжения. Предварительно принимаем
υск
= 0,5 м/с. Тогда [σ]к = 2500кг/см2.
Межосевое расстояние из условия контактной прочности и
отсутствия заедания определяется по уравнению:
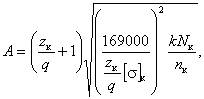
где
Nк
— мощность, передаваемая червячным колесом,
Nк
= 0,27 кВт.
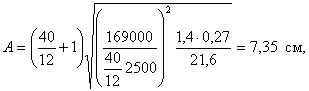
где
k
– коэффициент нагрузки. Предварительно принимаем
k
= 1,4.
Определяем модуль зацепления:

Принимаем ближайший стандартный
ms
= 3 мм.
В зависимости от принятого модуля окончательно
принимаем q
= 12. Уточненное межосевое расстояние будет:
А
= 0,5 (q
+
zк)
ms
=
0,5 · 52,3
= 78 мм.
4. Определение
основных размеров червяка и червячного колеса.
Делительный диаметр червяка
dч
= q·ms
= 3·12 = 36 мм.
Диаметр цилиндра выступов
Deч
=
dч
+ 2ms
= 36 + 2·3 = 42
мм.
Диаметр цилиндра впадин червяка
Diч
= dч
– 2,4ms
= 36 – 2,4·3 = 28,8 мм.
Угол подъема винтовой линии на делительном цилиндре
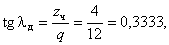
λд = 18°25'06", что соответствует
ГОСТ 2144–76 (таблица 3.18).
Длина нарезной части червяка (таблица
3.19)
L
= (12,5 + 0,09zк)
ms
= (12,5 + 0,09·40) ·3 == 48,3 мм.
Во избежание искажения рабочей части боковых
поверхностей витков, цилиндрического червяка при входе и выходе шлифовального
круга длину нарезной части увеличиваем при
ms
= 3 на 25 мм (таблица
3.19). Тогда
L
= 48,3 + 25 = 73,3 мм. Принимаем 74 мм.
Делительный и начальный диаметры окружностей
червячного колеса
dдк
=
dк
= mszк
= 3·40 = 120 мм.
Диаметр окружности выступов червячного колеса

Диаметр окружности впадин червячного колеса

Наружный диаметр D н
червячного колеса при zч = 4 равен

Ширина венца червячного колеса В при zч
= 4 равна

Условный угол обхвата 2γ червяка венцом колеса определяется уравнением

Скорость скольжения
υск
направлена по касательной к винтовой линии червяка и определяется по уравнению

что меньше предварительно
принятого значения υск
= 0,5 м/с. По
таблице 3.21 определяем коэффициент и угол
трения:
f = 0,055, р = 3°09'.
Определяем уточненное значение КПД
червячной передачи

Уточнение коэффициента нагрузки. Коэффициент
нагрузки
k = kКЦ kД
,
где kКЦ — коэффициент
концентрации нагрузки, зависит в основном от деформации червяка.
При переменной нагрузке эффективный
коэффициент концентрации нагрузки определяется по уравнению

где θ = 0,94
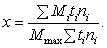
Здесь Mi,
ti, ni
— соответственно крутящий момент, время работы в часах и частота вращения в
минуту при режиме i

Мmax
— наибольший длительно действующий момент.
Коэффициент динамичности нагрузки
kД зависит от точности изготовления
передачи и от скорости скольжения. По
таблице 3.13
принимаем kД = 1,3.
Тогда
.
Так как уточненный коэффициент нагрузки меньше,
чем принятый раньше, то проверочный расчет по контактным напряжениям не
проводим.
5.
Проверочный расчет на изгиб.
Проверку на изгиб производим по червячному
колесу, так как витки червяка значительно прочнее зубьев колеса.
Условие прочности:
,
где [σ-1]и
— допускаемое напряжение изгиба;
Рк — окружное усилие на
червячном колесе
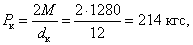
k — коэффициент нагрузки,
k = 1,32;
yк
— коэффициент формы зуба червячного колеса; определяется по приведенному числу
зубьев:

По
таблице 3.24
yк = 0,642.
Тогда

Силы в червячном зацеплении. Окружное усилие на
колесе, равное осевому усилию на червяке:
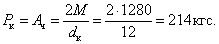
Окружное усилие на червяке равно осевому
усилию на червячном колесе:

Радиальное (распорное) усилие, раздвигающее оси
червяка и колеса:

6.
Тепловой расчет червячной передачи.
Тепловой расчет передачи носит условный характер
и состоит в определении разности температур масла, смазывающего передачу, и
окружающего воздуха.
Эта разность может быть определена по уравнению:

где t и t0
— температура масла и температура окружающего воздуха, град.;
kП — коэффициент относительной
продолжительности работы. Для передач, работающих с перерывами, для среднего
режима работы принимаем kП = 0,25;
kT
— коэффициент теплопередачи при нормальной естественной
циркуляции воздуха принимаем kT=10
ккал/м2 • град • ч;
S — свободная поверхность охлаждения
корпуса передачи, включающая 50 % поверхности ребер, принимаем S = 0,05 м2;
ψ —
коэффициент, учитывающий теплоотвод в корпус станка,
ψ
= 0,3 (см.п.
3.19).
7.
Расчет вала червяка.
а) предварительный расчет вала.
Предварительный расчет вала производится из
условия прочности на кручение без учета изгибных напряжений по уравнению:

б) определение усилий, действующих на вал.
Усилия, действующие в зацеплении z11— z12,
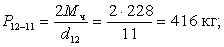

Усилия, действующие в червячном зацеплении:
Рк
= Ач = 214 кг; Рч = Ак =
126 кг; R = 78 кг.
в) проверка тела червяка на прочность и
жесткость.
Проектный расчет червяка на прочность не
производится. Его размеры определяются из условия прочности зубьев червячного
колеса. Поэтому выполняется лишь проверочный расчет червяка на прочность и
жесткость, причем проверка на прочность сводится к определению фактических
напряжений в теле червяка и сравнению их с допускаемыми или к определению
запасов прочности и сравнению их с допускаемыми. Проверка на жесткость
заключается в определении действительной стрелы прогиба и сравнении ее с
допускаемой стрелой прогиба, принятой для заданных условий.
На рисунке 7.28 показана расчетная схема червяка,
эпюры изгибающих моментов от сил Рк , Рч,
R, а также эпюра крутящих моментов.
Крутящий момент на валу червяка

Изгибающий момент от усилия Рч
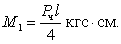
где l —
расстояние между опорами червяка. По компоновочной схеме принимаем (рисунок 7.29)
l=160 мм.
Наибольший изгибающий момент от распорной силы
R

Если перенести Pк
на ось червяка, то получится пара сил, изгибающий момент от которой

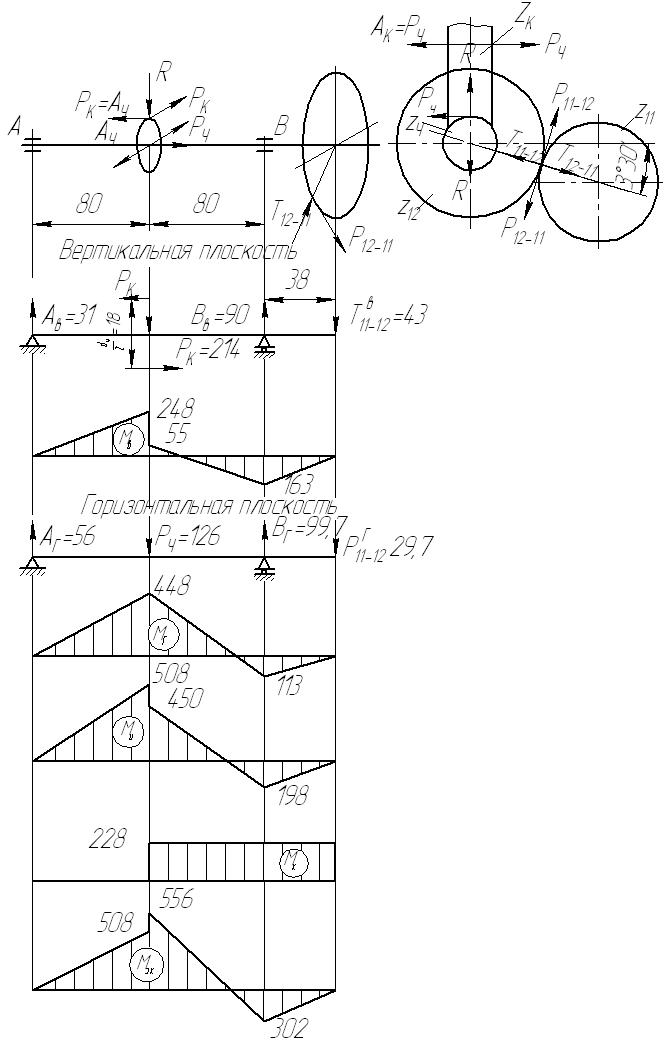
Просмотреть ближе
Рисунок
7.28 - Расчётная схема V
вала

Просмотреть ближе
Рисунок 7.29
- Компоновочная схема механизма суппорта
изгибает вал червяка, а сила сжимает
(растягивает) червяк.
Суммарный изгибающий момент

Тело червяка скручивается, изгибается и
сжимается (растягивается).
Наибольшие касательные напряжения от кручения:
Нормальные напряжения от сжатия (растяжения):

Наибольшее нормальное напряжение от изгиба:

Условие прочности по теории прочности энергии
формоизменения:


Допускаемые напряжения
принимаются
как для симметричного цикла изгиба по
таблице 3.30.
Несущая способность червячных передач
существенно зависит от жесткости червяка.
Допустимую величину прогиба принимаем
.
Так как червяк расположен симметрично
относительно опор, то величину прогиба определяем по уравнению:

где l —
расстояние между опорами, мм;
Е —модуль продольной упругости. Для стали
;
Iпр. — приведенный момент инерции
сечения червяка с учетом витков резьбы:

Тогда

* Влияние изгибающих моментов от усилий,
действующих на вал со стороны колеса z12,
на величину прогиба червяка незначительное.
г) основной расчет червячного вала.
Для выполнения этого расчета необходимо
построить эпюры изгибающих и крутящих моментов. Для удобства расчетов силы
раскладываем на две взаимно перпендикулярные плоскости (рисунок 7.28)
α
= 13°30' ; sin
α
= 0,234 ; cos
α = 0,97.
Силы, действующие в вертикальной плоскости:

Реакции опор в вертикальной плоскости:

BВ =
90 кгс.
Силы, действующие в горизонтальной плоскости:

Реакции опор в горизонтальной плоскости:

BВ=
99,7 кгс.
Наибольший результирующий изгибающий
момент определяем по уравнению:
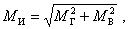
где MГ
и MВ — изгибающие моменты, которые
условно принимаем действующими в горизонтальной и вертикальной плоскостях.


Эквивалентный момент определяется по уравнению:



Диаметр вала:
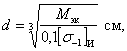
где
–
допускаемое напряжение при симметричном цикле изгиба,

Тогда
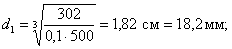
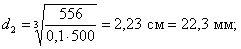
Большая суммарная реакция в опоре

Реакция в опоре:

Подбор подшипников вала червяка. Для обеих опор принимаем роликоподшипники
конические. Радиальные нагрузки опор A = 67
кгс, B = 134 кгс, осевая нагрузка
Aч = Pк=
214 кгс, частота вращения вала 213 об/мин, передача работает в масляной ванне с
легкими толчками при температуре подшипника
.
Желаемый срок службы подшипника Lh
= 5000 ч.
Предварительно принимаем по диаметру цапфы вала
d = 20 мм роликоподшипник конический средней серии 7304 с начальным
углом контакта β
= 18°, поскольку осевая нагрузка больше радиальных. Проверим возможность
применения этого подшипника для заданных условий.
Для указанного подшипника из каталога выписываем
е = 0,296 и определяем осевые составляющие
и
радиальных
нагрузок подшипников (рисунок 7.30).

Просмотреть ближе
Рисунок
7.30 - К подбору подшипников для V и VI валов


Поскольку
> ,
а Aч>0, то осевые нагрузки на
подшипники определяем по формулам, указанным
в п. 3.30:

Определяем эквивалентные нагрузки,
принимая для указанных условий работы kк = kT
= 1 и kб = 1,2 (таблица 3.63).
Для подшипника в I
опоре (рисунок 7.30). Так как отношение

меньше е=0,296, то приведенную нагрузку
вычисляем по формуле:

Для подшипника в опоре II.
Поскольку отношение:

то приведенную нагрузку вычисляем по формуле

Здесь Х = 0,4 для роликоподшипников
конических однорядных при отношении осевой нагрузки AII к радиальной A, большем е,
и Y = 2,026, взятых из каталога.
Величину требуемой динамической
грузоподъемности определяем по более нагруженной опоре:

Таким образом, предварительно выбранный
роликоподшипник средней серии 7304А (ГОСТ 27365—87) обеспечивает желаемую
долговечность. Условие Стр > С=2500 кгс выполняется.
При составлении расчетной схемы вала червяка (рисунок 7.29) точки приложения
радиальных реакций А и В определены с учетом расстояния
a (рисунок 7.30), вычисленного по формуле:
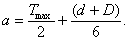
Монтажные размеры подшипника, мм:
d
= 20; D = 52; B=15; Tmax
= 16,5; r = 2.
д) расчет вала на выносливость.
После выполнения конструктивного чертежа червяка
(рисунок 7.31) определяется фактический запас прочности n
в нескольких предположительно опасных сечениях.
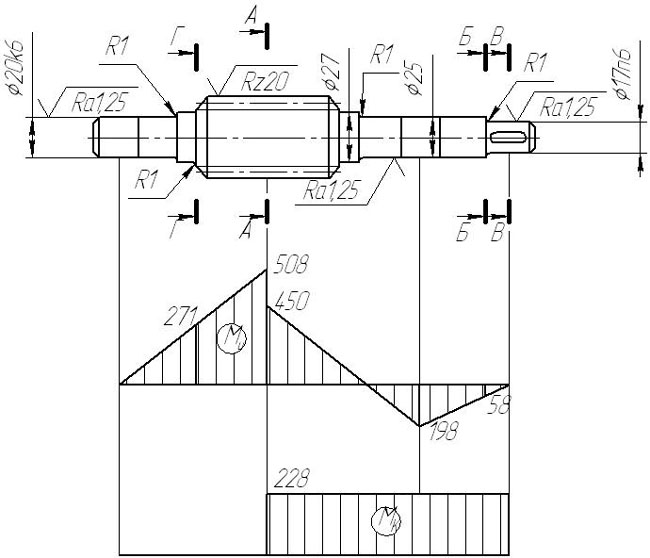
Просмотреть ближе
Рисунок 7.31 - К расчету V вала на выносливость
Коэффициент запаса прочности
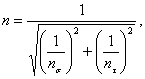
где
и
—
соответственно коэффициенты запаса по изгибу (при отсутствии кручения) и по
кручению (при отсутствии изгиба):

где
σ-1 и
τ-1
— пределы выносливости материала червяка при симметричном цикле изгибных и
касательных напряжений,
σ-1
=4100 кг/см2,
τ-1
= 2400 кг/см2 (таблице 3.37);
kσ
и kτ
— эффективные коэффициенты концентрации напряжений при изгибе и соответственно
кручении, kσ
= 2,5; kτ
= 1,9;
εσ и
ετ — масштабные факторы при изгибе и соответственно кручении,
εσ =
0,77; ετ
= 0,77;
ψσ
и ψτ— коэффициенты, характеризующие чувствительность
материала к асимметрии цикла напряжений,
ψσ = 0,2 и
ψτ = 0,1;
β — коэффициент упрочнения, при
закалке с нагревом т. в. ч.β = 2,0 (таблице
3.59);
σа
и τа
— переменные составляющие циклов (амплитуды цикла);
σm
и τm
— постоянные составляющие (средние напряжения цикла).
Можно считать, что
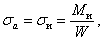
где
σи — номинальное
напряжение изгиба;
Ми — наибольший изгибающий
момент в рассматриваемом сечении;
W — момент сопротивления изгибу:
.
Ввиду наличия осевой
силы, вызывающей сжатие или растяжение вала
червяка:
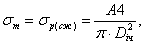
где А — продольная сила, А = Рк
— осевому усилию червяка.
Так как вал подвергается частому реверсированию,
принимаем, что напряжения кручения изменяются по симметричному циклу, тогда
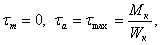
где Мк
— наибольший крутящий момент в рассматриваемом
сечении;
Wк — момент
сопротивления кручению,

Определяем коэффициенты запаса прочности в
наиболее опасных сечениях.
Сечение А—А:


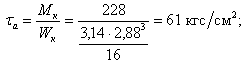

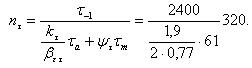
Коэффициент запаса прочности в сечении А—А:

Сечение Б—Б:
Коэффициенты:
εσ =
0,83 и ετ =
0,89 (таблица 3.58);
ψσ =
0,1 и ψτ
= 0,05 (таблица
3.57);
β = 0,85
(таблица 3.59).
kσ
= 1,7 при
и
для
сталей с σв
= 40 кг/мм2 (концентратор № 5,
приложение
4). kτ = 1,5 при тех же данных (таблица
3.60).
τm
= 0.
σm
= 0, так как вал в данном сечении не испытывает осевой нагрузки.


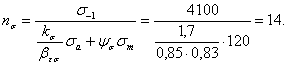

Коэффициент запаса
прочности в сечении Б—Б:

Сечение B—B:
Коэффициенты: kσ
=1,0 и kτ
=2,05 (приложение 8);
εσ = 0,87
и ετ = 0,91
(таблица 3.58);
β = 1(таблица
3.59).
σm
= 0, так как вал в данном сечении не испытывает осевых нагрузок
τm
= 0.


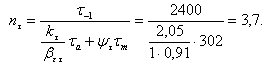
Коэффициент запаса прочности в
сечении В—В:
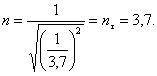
Сечение Г—Г:
Коэффициенты:
kσ
=2,01 (Приложение
4, 5);
kτ
=1,65 (таблица
3.60) (при
и
);
εσ =
0,83 и ετ =
0,89 (таблица 3.58);
β = 0,85
и ψσ
= 0,1 (таблица
3.59);
ψτ =
0,05 (таблица
3.57).
τm
= 0, так как вал в данном сечении
не испытывает напряжений кручения

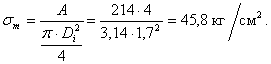

|