3.9 Материалы,
используемые для производства зубчатых колес. Термообработка
Выбор материалов и термообработки зубчатых колес
коробок скоростей и подач зависит от многих условий, важнейшими из которых
являются следуещее.
1. Критерии работоспособности, условия нагрузки, назначение машин, в которых
работают зубчатые передачи. Практика эксплуатации закрытых, хорошо смазываемых
передач коробок скоростей и подач показывает, что наиболее важным критерием
работоспособности их является усталостное выкрашивание поверхностных слоев
зубьев (контактная прочность).
Нагрузки, допускаемые по контактной прочности зубьев, пропорциональны
твердости поверхностного слоя материала зубьев. В некоторых случаях лимитирующей
является выносливость зубьев по изгибным напряжениям и она определяется в
зависимости от предела прочности сердцевины зуба. Износостойкость и
противозадирные свойства также возрастают с увеличением поверхностной твердости
зубьев. Поэтому наилучшим материалом для изготовления зубчатых колес являются
стали различных марок, подвергнутые термообработке. Зубчатые передачи коробок
скоростей и подач некоторых металлорежущих станков нередко испытывают
значительные перегрузки статического или ударного действия, например, при
обработке прерывистых поверхностей, снятии неравномерного припуска, включении
колес, муфт и т. д. Для восприятия таких нагрузок лучшими материалами также
являются стали. Специфической особенностью работы зубчатых передач коробки
скоростей и подач является то, что наряду с постоянными зубчатыми зацеплениями
имеются передачи, работающие поочередно и при значительно изменяющихся
нагрузках. В этом случае необходимо применять с целью повышения несущей
способности закаленные колеса (НВ ≥ 350), особенно в условиях работы с малым
общим или приведенным числом циклов нагружения.
2. Условия равнопрочности зубьев колеса и шестерни по основным критериям
работоспособности. Контактные напряжения у зубьев колеса и шестерни одинаковые,
но контактная прочность зубьев колеса в общем случае большая, чем шестерни,
из-за большего числа зубьев и большего радиуса кривизны зуба. Поэтому для колес
выбирается, как правило, менее прочный материал, чем для шестерни, с целью
создания равнопрочной зубчатой пары, при этом необходимо иметь в виду, что число
циклов нагружения шестерни больше, чем зубьев колеса. При поверхностной
твердости зубьев НВ ≤ З50 рекомендуется назначать такие сочетания марок стали и
их термообработку, чтобы поверхностная твердость зубьев шестерни превышала
поверхностную твердость зубьев колеса на 25-70 НВ. При этом условии
обеспечивается хорошая приработка передачи и почти одинаковая несущая
способность рабочих поверхностей зубьев. Если критерием работоспособности
является выносливость зубьев по изгибающим напряжениям, то материал шестерни
должен иметь более высокие механические характеристики, чем материал колеса, с
тем, чтобы компенсировать меньшие значения коэффициента формы зуба у, большее
число циклов нагружения и получить желательное равенство произведений,
обеспечивающее изгибную равнопрочность зубьев шестерни и колеса.
3. Условия приработки зубьев. В зависимости от твердости рабочих поверхностей
зубьев колеса и шестерни различают прирабатывающиеся и плохо прирабатывающиеся
передачи. При твердости рабочих поверхностей обоих колес НВ>350 передачи
являются плохо прирабатывающимися, при твердости НВ< 350 хотя бы одного из колес
возможна приработка передач. В соответствии с этим для колес с твердостью НВ>350
назначаются марки стали, подвергаемые закалке, цементации, азотированию, а при
HB ≤ 350 - марки стали, подвергаемые улучшению или нормализации.
4. Технология изготовления зубчатых колес. По
этому признаку зубчатые колеса можно разделить на две группы:
а) нарезаемые после окончательной термообработки;
б) нарезаемые до окончательной термообработки.
Твердость зубьев колес первой группы НВ ≤ 350. При этой твердости нарезание
зубьев долбяками и червячными фрезами сопровождается значительными усилиями
резания, понижением стойкости инструментов, понижением точности зубчатых венцов
и сокращением производительности.
Поэтому, как правило, зубчатые колеса с твердостью НВ = 320÷350 выполняются
небольших размеров (d=350 мм). В связи с тем, что твердость колес этой группы
зависит от их конструкции, размеров и температуры отпуска, то рекомендуется
назначать ее с учетом указанных факторов по графику (рисунок 3.14).Находят применение колеса с пониженной
твердостью (HB = 200÷280), которая достигается улучшением (закалка с высоким
отпуском) или нормализацией (нагревание с охлаждением на воздухе).
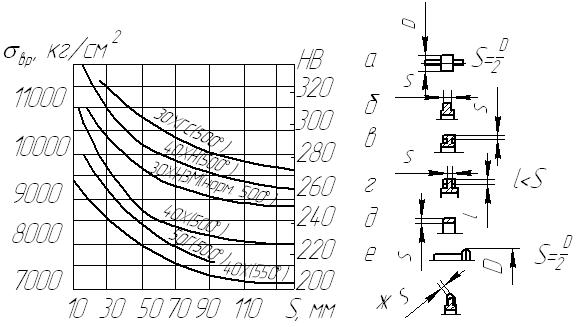
Рисунок 3.14 - График для определения σвр
или НВ в зависимости от сечения s
заготовки зубчатого колеса при улучшении или нормализации (в скобках
температура отпуска)
Просмотреть ближе
В коробках скоростей и подач металлорежущих станков в качестве улучшаемых
применяются стали марок 45, 50Г2, 40Х, 45Х. Эти марки стали находят в
станкостроении для производства зубчатых колес коробок скоростей и подач весьма
широкое применение. Улучшение применяется главным образом в мелкосерийном и
индивидуальном производстве, а также при производстве запчастей в условиях
неспециализированного производства.
Твердость колес второй группы НВ>350. Нарезание зубьев лезвийными
инструментами неприменимо по причине высокой твердости материала после
термообработки. Искажение профилей зубьев и другие ошибки, возникшие в процессе
термообработки, исправляются шлифованием или притиркой с применением специальных
паст. Для производства колес этой группы применяются качественные углеродистые
стали марок 45, 50, 50Г2 и легированные марок 40Х, 40ХН, 45Х, 20Х, 18ХГТ, 12ХНЗ,
20ХНЗА.
Для закаливаемых сталей обычно применяется нагрев т. в. ч. Достигаемая
твердость HRC 48÷52.
Твердость закаленных сталей измеряется обычно на приборе Роквелла по шкале С.
Для расчетов зубчатых колес по контактным напряжениям пользуются твердостью в
единицах Бринеля. Можно приблизительно принимать 10 НВ = 1 HRC. При расчете
зубьев на выносливость по изгибным напряжениям должна быть известна
характеристика σврс (предел прочности сердцевины на растяжение), для определения
которой можно воспользоваться зависимостью σврс ≈ 35 НВ. Цементируемые стали позволяют получить большую
твердость рабочих поверхностей зубьев (HRC 56÷бЗ) и достаточно вязкую
сердцевину, необходимую для повышения изгибной прочности и хорошо
сопротивляющуюся динамическим нагрузкам. Следует иметь в виду, что для зубчатых
колес, работающих при больших удельных и динамических нагрузках, при
недостаточной прочности сердцевины возможно продавливание цементированного слоя,
вследствие чего зубчатые передачи окончательно выходят из строя. Для указанных
условий чаще всего применяются цементируемые стали марок 12ХНЗА, 18ХГТ, 20ХНЗА.
После цементации и закалки можно получить твердость рабочих поверхностей зубьев
HRC 56-63, а твердость сердцевины НВ до 300.
5. Конструкция, размеры, точность зубчатых колес и возможные методы
механической обработки зубьев, материал и вид термообработки зубчатых передач, а
также экономические показатели тесно взаимосвязаны. Нередко улучшение одних
показателей влечет ухудшение других.
Например, для получения высоких показателей контактной прочности рабочих
поверхностей зубьев, глубинной контактной прочности, изгибной прочности зубьев и
достаточно вязкой сердцевины, хорошо противостоящей динамическим нагрузкам,
целесообразно применять легированные стали, цементируемые в твердом
карбюризаторе. Но эти стали часто не могут быть использованы для цельных блоков
зубчатых колес высокой точности (5-6-7-й степени) по той причине, что ошибки
элементов зубчатого венца и окалина могут быть устранены шлифованием лишь в том
случае, когда обеспечен выход для шлифовального круга. Последнее обстоятельство
требует увеличения ширины проточки между венцами, а следовательно, удлинения
блока в осевом направлении, что вызывает весьма нежелательное увеличение длины
хода блока при включении передач, увеличение расстояния между опорами,
уменьшение жесткости опор валов, рост габаритов и стоимости коробок.
Поэтому приходится применять стали, подвергаемые улучшению или нормализации,
и соглашаться, таким образом, с понижением несущей способности зубчатых передач
и некоторым увеличением их размеров, стоимости и т. д.
Нарезание зубьев можно произвести после термообработки и достичь 8-й степени
точности, а в качестве отделочной операции для зубьев применить шевингование,
посредством которого достигается 7-я степень точности. Для получения блоков
зубчатых колес, венцы которых должны иметь 5–6-ю степень точности, при небольших
осевых размерах блоки изготавливаются сборными (рисунок 3.15).
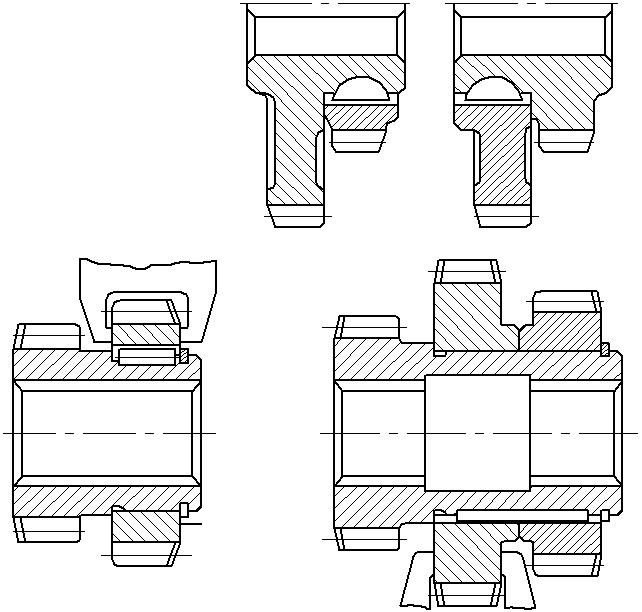
Просмотреть ближе
Рисунок 3.15 - Конструкции сборных блоков зубчатых
колес
Однако это вызывает значительное удорожание производства колес. Блоки
зубчатых колес могут изготавливаться также из стали марок 40Х, 45Х, 40ХН и
других, подвергаемых объемной закалке или закалке с нагревом т. в. ч. после
нарезания зубьев. Зубчатые венцы получаются 7-8-й степени точности. В качестве
отделочной операции для зубьев применяется притирка. Объемная закалка
применяется главным образом для малоответственных колес из-за существенных
недостатков: значительного искажения профиля зубьев, появления грубых
погрешностей зубчатого венца, низкого сопротивления динамическим воздействиям,
большой неоднородности предела выносливости по изгибным напряжениям.
Для зубчатых блоков так же, как и для колес других конструкций, в настоящее
время широко используется закалка с нагревом т. в. ч. Этот способ термообработки
свободен от многих недостатков объемной закалки, обеспечивает высокую твердость
поверхностей зубьев в сочетании с вязкой сердцевиной. Для мелкомодульных
зубчатых колес, которые часто встречаются в коробках скоростей и подач
металлорежущих станков, во избежание сплошного науглероживания и сплошной
закалки зубьев нужно назначать жидкостную цементацию или цианирование.
Недопустимо для мелкомодульных колес выбирать стали, подвергаемые объемной
закалке или даже закалке с нагревом т. в. ч. во избежание сплошного
прокаливания.
Если закаливаются только боковые стороны зубьев,
то возникают остаточные растягивающие напряжения в точках перехода закаленного
слоя к незакаленному, вследствие чего понижается изгибная прочность зубьев,
наблюдается большой разброс в величинах нагрузок, лимитируемых изгибной
прочностью зубьев. В связи с этим такой вид термообработки приемлем в тех
случаях, когда имеется весьма значительный запас прочности по изгибным
напряжениям (например, не меньше 2,5-3).
При модуле до 2,5 мм можно применить индивидуальную закалку с нагревом т. в.
ч. впадины каждого зуба. Вместе с тем закалка отдельно каждой впадины по всему
контуру способствует значительному повышению изломной прочности зубьев.
В отличие от зубчатых венцов, подвергнутых объемной закалке, при
поверхностной закалке с нагревом т. в. ч. искажения профиля невелики, а поэтому
притирка или шлифование производятся лишь в тех случаях, когда необходимо
получить колеса 6-7-й степени точности.
Таким образом, при назначении материала колес следует учитывать
технологические особенности термообработки и последующей окончательной
механической обработки зубьев.
На поверхностях, подвергнутых жидкостной цементации, цианированию,
азотированию, не образуется окалины, поэтому последующей обработки абразивными
инструментами, как правило, не требуется; лишь иногда в весьма ответственных
случаях производится притирка зубьев. Следовательно, точную механическую
обработку можно производить до химико-термической обработки. Если цементация
производится в твердом карбюризаторе, то окончательная механическая обработка
профилей зубьев необходима, но при этом следует иметь в виду, что шлифование
зубьев может оказаться недопустимым ввиду малой глубины цементированного слоя.
Выбор материалов предопределяет габариты передачи. Чем меньшие требуются
габариты, тем необходимо выбирать более прочный материал при прочих равных
условиях; если габариты не ограничиваются, можно выбирать материалы со средними
механическими качествами, стоимостью и дефицитностью.
Если колесо изготовлено заодно с валом, на котором имеются цапфы под
подшипники, резьбы и другие элементы, не подвергаемые закалке или закаливаемые
до невысокой твердости, то выбор материала предопределяется не нагрузочной
способностью зубчатой передачи, а требованиями, предъявляемыми к указанным
элементам. Обычно прочность и жесткость вала-шестерни достаточно высокие,
поэтому для изготовления их можно применить качественные углеродистые стали
марок 40, 45, 50, 50Г. Целесообразно в ответственных случаях применять стали
марок 40Х, 45Х, 40ХН. Для увеличения нагрузочной способности зубья подвергаются
закалке с нагревом т. в. ч. Если требуются 7-я и выше степени точности, то
необходимо зубья шлифовать или притирать.
6. В связи с тем, что окружные скорости зубчатых колес зависят от частоты
вращения и диаметров, для колес скоростных передач необходимо применять
материалы с большими значениями допускаемых напряжений для того, чтобы уменьшить
габариты зубчатых колес. Уменьшение скорости существенно снижает динамические
нагрузки. При окружных скоростях 2-6 м/с рекомендуется применять углеродистые
стали; при больших окружных скоростях - легированные стали.
7. Экономические показатели. Выбранный материал должен гарантировать высокую
несущую способность передачи, вместе с чем обеспечивать при заданных условиях
работы наименьшие расходы на изготовление зубчатых колес. Несущая способность
закрытых зубчатых передач может быть повышена при одновременном уменьшении
габаритов и веса за счет повышения допускаемых контактных напряжений [σ]к
или допускаемых изгибных напряжений [σ] в зависимости от основного критерия
работоспособности. При расчетах полезно использовать данные по относительной
стоимости конструкционных сталей.
Важным источником экономии сталей является возможно более широкое
использование термообработки, повышение ее качества, следовательно, увеличение
механических свойств сталей.
Экономические показатели выбранного материала и термообработки могут
характеризовать равнопрочность зубчатых колес по основным критериям
работоспособности.
Для производства зубчатых колес коробок
скоростей и подач применяется сравнительно небольшое число марок стали, основные
показатели которых указаны в таблица 3.9.1 и 3.9.3 [80].
Таблица 3.1 - Стали, применяемые для зубчатых колес
Рекомендуемая область применения |
Марка стали |
Твердость |
1 |
2 |
3 |
Зубчатые колеса с модулем
свыше 4 мм при небольших нагрузках
|
45
|
HRC =
48-52 закалка с нагревом т. в. ч.
|
Зубчатые колеса с модулем свыше 6 мм при небольших
нагрузках
|
50
|
То же
|
Зубчатые колеса крупных размеров при небольших
нагрузках
|
50Г2
|
НВ=212-241
улучшение
|
Зубчатые колеса крупных размеров при средних
нагрузках
|
50Г2
|
HRC=27-33
|
Зубчатые колеса средних размеров при средних
удельных нагрузках и высоких скоростях
|
20Х
|
HRC=56-63
сердцевина НВ≥212
|
Зубчатые колеса с модулем до 3 мм, от которых
требуется высокая износостойкость и незначительные деформации при
термообработке
|
20Х
|
HRC=58-62
закалка с нагревом т. в. ч.
|
Зубчатые колеса при средних и больших удельных
нагрузках, высоких скоростях и наличии ударных нагрузок при
весьма высоких требованиях к снижению
габаритов и веса
|
18ХГТ
12ХНЗА
20ХНЗА
|
HRC=56-62
сердцевина НВ=240-300
|
Зубчатые колеса при средних удельных нагрузках и
средних скоростях v
≤
10 м/с
|
40Х
|
HRC=22-30
|
Зубчатые колеса и рейки при больших удельных
давлениях, средних скоростях и отсутствии ударных нагрузок
|
40Х
|
HRC=45-50
|
Зубчатые колеса мелких размеров
|
40Х
|
HRC=50-55
|
Зубчатые колеса при средних удельных нагрузках,
средних скоростях и требованиях повышенной прочности сердцевины
|
40Х
|
HRC=48-52
закалка с нагревом т. в. ч.
|
Зубчатые колеса при больших удельных нагрузках,
высоких скоростях и наличии ударных нагрузок
|
40ХН
|
HRC=50-54
|
Зубчатые колеса при высоких скоростях и наличии ударных
нагрузок
|
40ХН
|
HRC=48-52
закалка с нагревом т. в. ч.
|
Зубчатые колеса для точных
передач, обрабатываемых в улучшенном состоянии, при требовании
повышенной твердости
|
35ХМ
|
НВ =255-302
|
Зубчатые колеса, работающие в условиях атмосферной
коррозии
|
4X13
|
HRC=48–52
|
Зубчатые колеса для небольших
нагрузок при необходимости высокой коррозийной
стойкости
|
Х18НЮТ
|
НВ = 140-175
|
Блоки зубчатых колес в тех
случаях, когда требуется высокая ответственность, и при невозможности
применения отделочной операции для зубьев после термообработки.
Зубчатые колеса внутреннего
зацепления |
38ХМЮА |
НВ>350 |
|
Таблица 3.2 - Рекомендуемые сочетания материалов, применяемые
для изготовления зубчатых колес и шестерен
Шестерня |
Колесо |
Марка стали |
Рекомендуемый способ
термообработки |
Марка стали |
Рекомендуемый способ
термообработки |
45
|
Улучшение
или нормализация НВ<350 |
35 |
Улучшение
или нормализация НВ <350 |
50 |
Улучшение или нормализация
НВ < 350 |
35 |
Улучшение или нормализация
НВ < 350 |
50Г |
Улучшение или нормализация
НВ < 350 |
45 |
Улучшение
или нормализация НВ<350 |
40Х |
Улучшение или нормализация
НВ<350 |
50 |
Улучшение или нормализация
НВ <; 350 |
40ХН |
Улучшение
или нормализация НВ < 350 |
40Х |
Для кованых сталей
улучшение или нормализация |
45, 50 |
Поверхностная
закалка с нагревом т. в. ч., объемная закалка НВ > 350 |
40ХН |
Для кованой стали
поверхностная
закалка
НВ > 350 |
45, 50 |
Поверхностная
закалка с нагревом т. в. ч., объемная закалка НВ > 350 |
35 |
Поверхностная закалка с
нагревом т. в. ч. объемная закалка
НВ > 350 |
40Х
40ХН |
То же
То же |
50
40Х |
НВ
>
350
Нормализация и
улучшение |
15Х
20Х |
Цементация и закалка
НВ>350 |
15Х;
20Х |
Цементация и закалка
НВ > 350 |
12ХНЗА
20ХНЗА
18ХГТ |
Цементация и закалка
НВ > 350 |
12ХНЗА
20ХНЗА
18ХГТ |
Цементация и закалка
НВ > 350 |
|
Таблица 3.3
- Механические характеристики сталей, применяемых
для изготовления зубчатых колес
Марка стали |
Заготовка |
Механические характеристики, кг/см2 |
Твердость
|
Термообработка
|
Вид |
Диаметр D, мм |
Толщина S, мм |
σВ |
σТ |
Σ-1 |
Сердце-вины
НВ |
Поверх-ности
НRC |
35 |
Поковка
|
Любой
|
Любая
|
5400-5800
|
3200
|
2300-2500
|
150-180
|
-
|
Нормализация
|
45
|
То же |
То же
|
То же
|
6100-7000
|
3600
|
2600-3000
|
170-200
|
-
|
То же
|
45
|
То же |
60-90
|
45-70
|
7500-8500
|
4500
|
3200-3400
|
210-230
|
- |
Улучшение
|
45
|
То же |
30
|
30
|
10000
|
7500
|
4300
|
335-492
|
- |
Объемная закалка
|
45
|
То же |
Любой
|
Любая
|
6000
|
3400
|
2600-3000
|
HRC 53-55
|
- |
Поверхностная закалка
|
50
|
То же |
То же
|
То же
|
5800-6200
|
3200
|
2500-2800
|
210-230
|
- |
Нормализация
|
50Г
|
То же |
То же
|
То же
|
6600-7000
|
4000
|
3400
|
210-230
|
- |
То же
|
15Х
|
Поковка
|
-
|
-
|
7000-8000
|
-
|
-
|
-
|
58—63
|
Цементация и закалка
|
20Х
|
Поковка |
60
|
60
|
8000
|
6500
|
4200
|
230-240 |
- |
Цементация и закалка
|
40Х
|
Поковка |
280
|
90
|
8000-9000
|
5500
|
4200-4600
|
230-260
|
- |
Улучшение
|
40Х
|
Поковка |
120
|
60
|
9000-10000
|
8000
|
5000
|
250-280
|
- |
Объемная закалка
|
40Х
|
Поковка |
30
|
30
|
11000-13500
|
9000-10500
|
5000-5900
|
350-420
|
35-42
|
|
40Х
|
Поковка |
Любой
|
Любая
|
10000
|
8500
|
5000
|
-
|
52-56 |
Поверхностная закалка
|
40ХН
|
Поковка |
То же
|
То же
|
7500-8500
|
4500
|
4100-4400
|
220-250
|
- |
Улучшение
|
40ХН
|
Поковка |
150
|
75
|
9000-10000
|
7000
|
4600-5000
|
270-300
|
- |
То же
|
40ХН
|
Поковка |
75
|
75
|
10000
|
8500
|
5000
|
- |
50-54
|
Объемная закалка
|
12ХНЗА
|
Поковка |
90
|
90
|
10000
|
8500
|
5000
|
260-400
|
58—63
|
Цементация с двойной
закалкой |
20ХНЗ
|
Поковка |
-
|
-
|
8000-9000
|
-
|
-
|
-
|
58—63
|
Цементация с закалкой |
18ХГТ
|
Поковка |
-
|
-
|
11500
|
9500
|
5500
|
400
|
56—62
|
Цементация с двойной
закалкой |
38ХМЮА
|
Поковка |
30 |
30 |
10000
|
8500
|
5000
|
350 |
60
|
Азотирование с
предварительной закалкой |
|
|