7.2 Коробка
подач
Тема проекта: Рассчитать и сконструировать
шестиступенчатую коробку подач и передачи к продольному суппорту. Реверсирование
осуществляется электродвигателем. Быстрый отвод суппорта не предусматривается.
Исходные данные: схема механизма коробки подач и
передач к продольному суппорту (рисунок 7.22). Пределы подач
s1
= 1,02 мм/об, s6=l,8
мм/об. Наиболее прочный обрабатываемый материал сталь с σв = 75 кг/мм2.
Содержание пояснительной записки такое же, как и в примере расчета коробки
скоростей (см. п. 7.1.1).
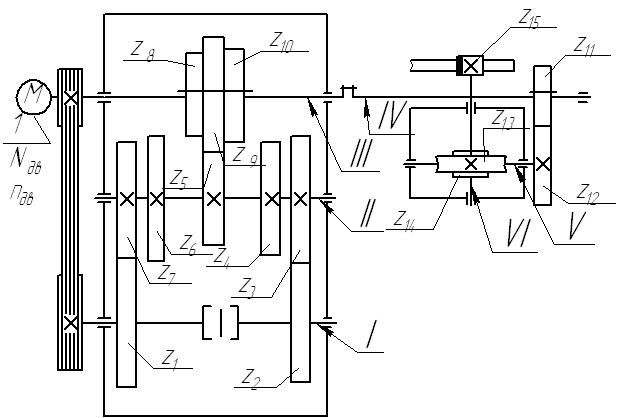
Просмотреть ближе
Рисунок 7.22 - Кинематическая схема
коробки подач
7.2.1 Выбор
электродвигателя и кинематический расчет
7.2.1.1
Силовой расчет механизма подач
Тяговое усилие, преодолевающее полезные и вредные
сопротивления:
P
= kпPx
+ F
кг (с. 84 [49]),
где
Рх —
осевая составляющая силы резания (рисунок 7.23),
kп
=1,5 – коэффициент, учитывающий влияние
опрокидывающего момента, возникающего из-за
несимметричного положения силы подачи (табл. 8 [49]);
F –
сила трения в направляющих для суппортных токарных станков с призматическими
направляющими по уравнению F
= (Pz+Q)f
(табл. 8
[49]), где Pz
– вертикальная составляющая силы резания
(рисунок 7.23), Q
– вес движущихся частей. Принимаем примерное значение
Q =
40 кг, f
= 0,15—приведенный коэффициент трения (табл. 8 [49]).
Силы резания определяются по уравнениям:
.
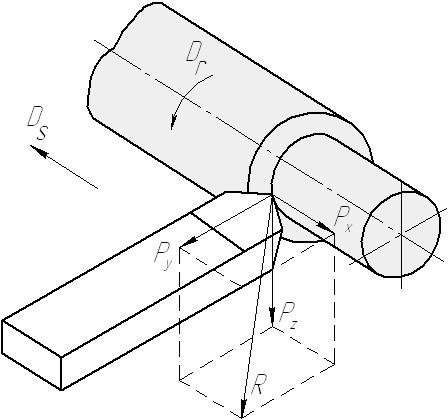
Просмотреть ближе
Рисунок 7.23 - Схема усилий резания при
точении
По таблице принимаем значения коэффициентов для случая
обработки сталей с пределом прочности σв = 75 кг/мм2.
Режущий инструмент стандартный.
Таблица 7.9
Сила
резания |
Значения коэффициентов |
|
С,
кГ |
x |
y |
Pz
Рх |
204
66,3 |
1,0
1,2 |
0,75
0,65 |
|
Определяем наибольшие силы резания при максимальных
значениях t
и
s,
принимая наибольшую глубину резания
t =
3 мм,
Pz
=
C·tx·Sy
= 204·3·1,80,75 = 955 кг;
Рх
=
C·tx·Sy
= 66,3·31,2·1,80,65 =
248 кг.
Сила трения
F=
(955 + 40) 0,15 = 151 кг.
Тяговое усилие Р =248 · 1,15 + 151 = 436 кг.
Работа, выполняемая за один оборот реечной шестерни
(с. 84 [49]),
РН
= 2πМк,
где Мк – крутящий момент на
валу реечной шестерни;
Н – ход
кинематической пары, преобразующей вращательное движение в прямолинейное.
Для реечной пары
H
= πmz
мм (с. 14 [49]),
где т – модуль зацепления, мм;
z
– число зубьев реечного колеса.
Предварительно принимаем z
= 10, т = 3 мм. Тогда
H
= 3,14·3·10 = 94,2 мм.
Искомый крутящий момент
.
7.2.1.2
Кинематический расчет
Подачи целесообразно располагать по геометрическому
ряду. Определим знаменатель этого ряда
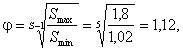
где
S – число ступеней коробки подач.
Для удобства последующих расчетов выразим степени φ:
φ2=1,26; φ3=1,41;
φ4=1,58.
Геометрический ряд подач в мм/об шпинделя
s1
= l,02; s2= s1·φ=1,02 · 1,12=1,14;
s3=
1,02 · 1,26= 1,28; s4=l,02 · 1,41 = 1,45;
s5=
1,02 · 1,58 = 1,62; s6 = l,80.
Определяем числа оборотов реечной шестерни на один
оборот шпинделя для каждой подачи по уравнению
об.
реечн. шест./об. шп.,
где s
— подача, мм/об;
т– модуль
реечной шестерни, мм;
z—число зубьев реечной шестерни.
об.
реечн. шест./об. шп.
Выполнив аналогичные вычисления, при других подачах
получим:
п'2
= 0,0121; n’3
= 0,0136; п'4 = 0,015; п'5 =
0,0168; n’6
= 0,0188.
Принимая наибольшую частоту вращения шпинделя
n
= 2000 об/мин, определим числа оборотов в
минуту реечной шестерни
n1
=n’1·2000
= 0,0108·2000 = 21,6 и аналогично
n2
= 24,2;
n3
= 27,2; n4
= 30; n5
= 34; n6
= 38.
Определяем максимальную требуемую мощность,
передаваемую реечной шестерней:
.
7.2.1.3
Выбор электродвигателя
Принимаем ориентировочные значения КПД:
η1
= 0,99 — пары подшипников качения;
η2
= 0,98 — пары прямозубых цилиндрических колес, работающих в масляной ванне (таблица
2.1);
η3
= 0,96 — реечной передачи;
η4
= 0,95 — клиноременной передачи (таблица
2.1);
η5
= 0,9 — червячной передачи (таблица
2.1).
Общий КПД привода

Требуемая мощность электродвигателя
.
Выбираем электродвигатель асинхронный с
короткозамкнутым ротором в закрытом обдуваемом исполнении типа АО32 – 6
мощностью Nдв
= 0,6 кВт n
= 930 об/мин.
Диаметр конца вала электродвигателя
d
= 18 мм.
7.2.1.4
Построение графика частот вращения, определение передаточных чисел и чисел
зубьев колес
Число оборотов электродвигателя не входит в
стандартный ряд чисел оборотов, поэтому передаточное число ременной передачи не
может быть степенью знаменателя φ ряда чисел оборотов. Передаточное число
ременной передачи выбираем так, чтобы вал
I
(рисунок 7.22) имел число оборотов из стандартного ряда:
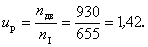
Передаточные числа первой группы двухваловой передачи
принимаем по графику чисел оборотов (рисунок 7.24)
u1
= φ5 = 1,255 = 1,78;
u2
= φ6 = 1,126 = 2.
Необходимо проверить условие:
.
Это условие выполняется.
Принимаем суммарное число зубьев для первой
двухваловой передачи zΣ
= 75 (таблица 3 [64]). При одинаковых модулях колес справедливы уравнения:
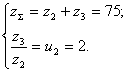
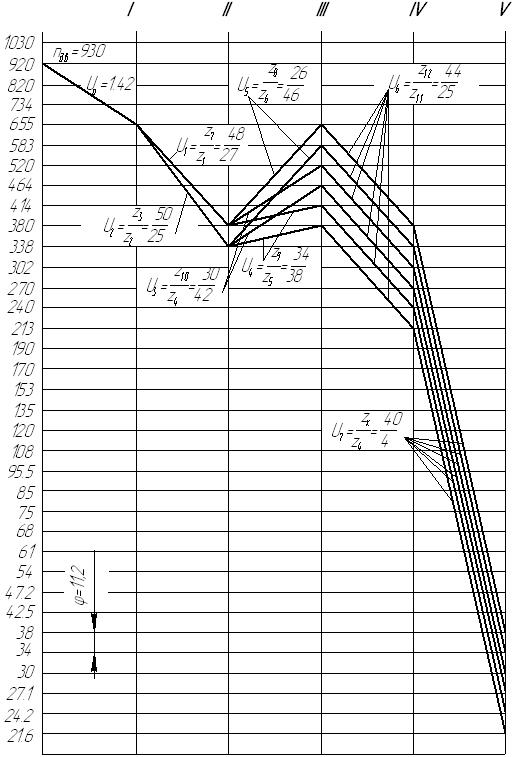
Просмотреть ближе
Рисунок 7.24 - График частоты вращения
Решая эти уравнения, получим:
z1
= 27; z7
= 48; z2
= 25; z3
= 50.
Передаточные числа второй группы двухваловой передачи
также принимаем по графику частоты вращения (рисунок 7.24).
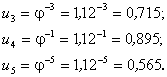
Исходя из тех же условий, что и в предыдущем случае, и
приняв суммарное число зубьев второй двухваловой передачи
zΣ
= z4
+ z10
= z5
+ z9
= z6
+ z8
= 72,
составим уравнения:
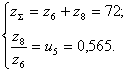
Решая эти уравнения, получим:
z4
= 42; z10
= 30; z9
= 34; z5
= 38; z8
= 26; z6
= 46.
Передаточное число третьей двухваловой передачи (рисунок
7.24)

Принимаем суммарное число зубьев третьей двухваловой
передачи

Запишем уравнения
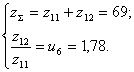
Решая эти уравнения, получим:
z11
= 25,
z12
= 44.
Передаточное число червячной передачи и = 10,00
(таблица 3.16).
В соответствии с ГОСТ 2144—76 принимается по таблице
zч
= 4, тогда
zк
= zч
· и =4 · 10 = 40.
Результаты подбора зубьев сведены в таблицу 7.10.
Таблица
7.10
и |
u1
= l,78 |
u2
= 2 |
 |
 |
 |
u
= 10 |
u6
=
1,78 |
 |
 |
 |
 |
 |
 |
 |
 |
zΣ |
75 |
72 |
|
69 |
|
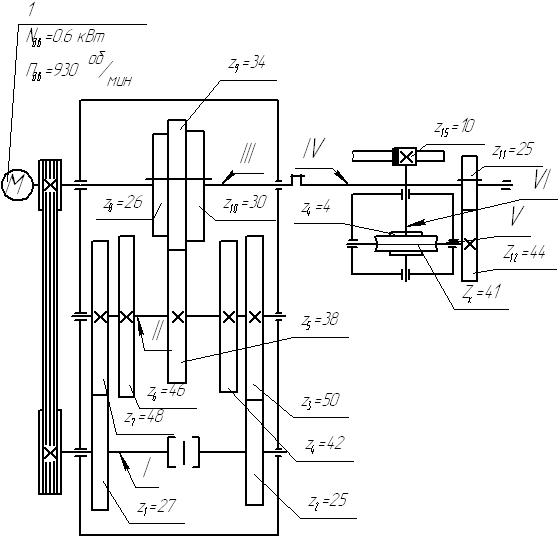
Просмотреть ближе
Рисунок 7.25 - Расчетная кинематическая
схема коробки подач
Кинематический расчет завершаем вычерчиванием
кинематической схемы механизма коробки подач с соблюдением произвольного
масштаба в радиальном направлении. На схеме указываем числа зубьев колес, данные
об электродвигателе, нумеруем валы передачи (рисунок 7.25).
|