3.24 Расчет
валов и осей
3.24.1 Специфические
особенности работы валов коробок скоростей и подач
Расчет валов коробок скоростей и подач имеет
специфические особенности, обусловленные конструктивными и кинематическими
разновидностями коробок скоростей и подач, а также их назначением. Эти
особенности должны быть учтены при составлении расчетных схем, установлении
критериев работоспособности и расчета, а также при определении размеров валов и
их конструкций. Эти особенности следующие:
а) наличие зубчатых колес или их блоков,
вводимых в зацепление путем осевого перемещения. Поэтому один и тот же вал будет
передавать различные крутящие моменты в зависимости от передаточных отношений
зубчатых колес, вводимых в зацепление. Установив, в каких случаях имеются
наибольшие нагрузки на опоры и наибольшие изгибающие моменты на валу, следует
производить расчеты при нескольких включениях. При более высоких скоростях валы,
зубчатые колеса и другие элементы передач будут недогружены, размеры их
существенно большими тех, которые необходимы по условиям прочности и жесткости,
а материал недоиспользован;
б) пониженная жесткость валов на изгиб и
кручение, по сравнению, например, с валами редуктора, что обусловлено увеличением
длины валов за счёт блоков зубчатых колес, многодисковых фрикционных муфт.
Недостаточная жесткость валов вызывает ряд весьма нежелательных явлений в работе
зубчатых передач, кулачковых муфт и подшипников. Кроме того, недостаточная
жесткость является одной из причин повышения уровня шума, возникновения вибраций,
недопустимых по амплитуде крутильных и поперечных колебаний, вызывающих
ухудшение точности и качества поверхностей деталей, обрабатываемых на станках,
понижение точности обработки. Поэтому необходимо производить соответствующие
расчеты на жесткость. Диаметры валов, выбранные для обеспечения необходимой
жесткости, больше, чем если бы были выбраны из расчета на прочность. По этой
причине валы в коробках скоростей станков иногда работают при малых напряжениях.
В результате расчетов на жесткость определяются
размеры вала, обеспечивающие при заданных нагрузках деформации, не превышающие
заранее предписанных, величина которых гарантирует необходимое качество работы
зубчатых зацеплений, опор и т. д.
Жесткость валов может определяться не только в
направлении действия наибольшей нагрузки, но в любом другом направлении, по
которому жесткость должна быть ограничена. Следует иметь в виду, что деформация
системы слагается из двух деформаций, одна из которых представляет линейное или
угловое перемещение под действием сил и моментов, другая же — контактную
деформацию в местах соприкосновения деталей. С целью уменьшения контактной
деформации необходимо увеличивать поверхностную прочность сопрягаемых деталей,
улучшать качество обработки контактных поверхностей;
в) валы коробок скоростей и подач чаще всего
располагаются в разных плоскостях, что приводит к значительному усложнению
расчетных схем. Плоскости действия суммарных реакций опор и изгибающих моментов
для различных валов не совпадают. Поэтому для расчетов удобно все силы,
действующие на валы со стороны различных передач, условно отнести к двум взаимно
перпендикулярным плоскостям, а затем произвести геометрическое суммирование
изгибающих моментов и опорных реакций. Если на валу
расположено несколько зубчатых колес, вводимых в зацепление в определенной
последовательности, то следует установить путем расчета при нескольких
включениях наиболее неблагоприятное положение, при котором нагрузки на опоры и
изгибающие моменты окажутся наибольшими;
г) введение третьей опоры, которая, как правило,
располагается в промежуточной стенке коробки и способствует увеличению жесткости
и виброустойчивости, повышению несущей способности зубчатых колес, кулачковых
муфт и т. д.;
д) широкое применение шлицевых валов и лишь в
некоторых случаях направляющих шпонок.
Конструктивные формы валов оказывают весьма
существенное влияние на усталостную прочность, кроме того, остаточные напряжения
после термообработки у валов сложной формы всегда больше, чем у валов простой
формы, что оказывает влияние на усталостную прочность;
е) в коробках скоростей часто встречаются валы,
имеющие реверсивное вращение, при котором возникают напряжения кручения,
изменяющиеся по знакопеременному циклу и способствующие появлению весьма опасных
для работы деталей передач крутильных колебаний;
ж) в коробках скоростей применяются такие
кинематические варианты, при которых одни и те же
зубчатые колеса могут работать ведущими, ведомыми или паразитными, а поэтому
расчетные схемы валов значительно отличаются друг от друга;
з) широкое применение на первой ступени коробок
скоростей ременных передач для привода от электродвигателя. Характерной
особенностью нагружения ведомого вала передачи является большой
изгибающий момент над опорой, вызываемый ременной передачей при значительной
длине консоли. С целью уменьшения напряжения изгиба в опасном сечении и прогибов
вала необходимо устанавливать шкивы на втулках (рисунок 3.48), разгружающих вал.
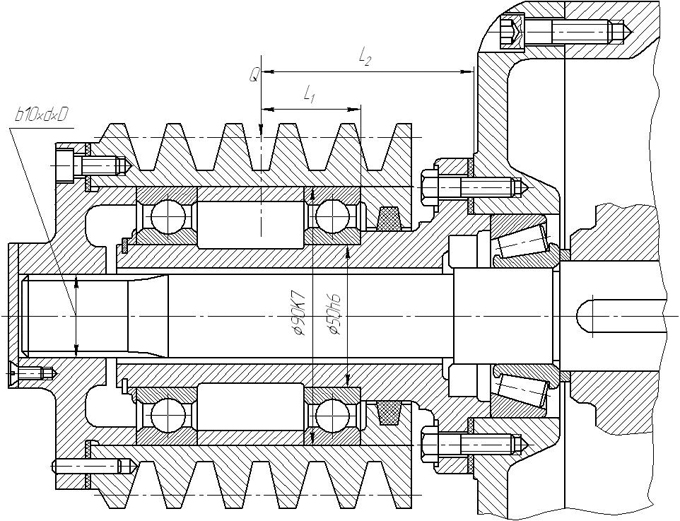
Просмотреть ближе
Рисунок 3.48
- Шкив на разгрузочной
втулке
3.24.2 Материалы и термообработка
На выбор материала для валов и осей и их
термообработку оказывают влияние критерии работоспособности, конструктивные
особенности, технология изготовления, условия работы. В некоторых случаях
определяющим при выборе материалов и термообработки является работоспособность
шлицев, что особенно важно для коробок скоростей и подач, иногда зубчатых венцов
и резьб.
Основными материалами для изготовления валов и
осей являются углеродистые и легированные стали, применение и марки которых
указаны в таблице 3.56.
Использование легированной стали для валов
обусловлено необходимостью высоких механических характеристик для сокращения
габаритов и повышения надежности в ответственных случаях.
Для быстроходных валов, диаметры ступеней
которых определяются исходя из требований жесткости, нерационально использовать
легированные стали по той причине, что величина модуля упругости у всех марок
стали, по существу, одинакова. Поперечные сечения валов, полученные по критерию
жесткости, обеспечивают достаточную прочность даже в том случае, когда эти валы
изготовлены из углеродистых конструкционных сталей.
Твердость и прочность отдельных элементов и
поверхностей валов (цапф, шлицев) легко достигается закалкой с нагревом т. в. ч.
Только в тех случаях, когда требуется, например, высокая прочность подвижного
шлицевого соединения, передающего повышенные динамические нагрузки,
целесообразно применять легированные стали. Известно, что с повышением предела
прочности возрастает чувствительность материала к концентрации напряжений,
поэтому применение высокопрочных сталей для валов, которые постоянно работают
при переменных напряжениях, не всегда оправдано.
Таблица 3.56 - Стали, применяемые
для изготовления валов и осей
Рекомендуемая область применения |
Марка стали |
Твердость |
Валы в
подшипниках качения, шлицевые
валы |
45
|
НВ 220—260 |
Валы в
подшипниках скольжения
средних и крупных размеров при требовании
высокой поверхностной твердости
и повышенной износостойкости |
45 |
HRC
54 —60
Закалка с нагревом т. в. ч. |
Валы
крупных размеров при общей
повышенной прочности,
износостойкости
и большой глубине закаленного
слоя |
45Х
|
HRC
52—56
Закалка с нагревом т. в. ч. |
Валы ответственных передач, шлице-вые валы для подвижных соединений и ударных нагрузок |
40ХН |
HRC
54—58
Закалка с нагревом т. в.ч. |
Валы
средних и крупных размеров
при требовании высокой поверхностной твердости,
повышенной износостойкости |
50 |
HRC
54—58
Закалка с нагревом т. в ч. |
Валы
крупных размеров в подшипниках
качения |
50Г2
|
НВ212—241 |
Быстроходные гладкие, ступенчатые
и шлицевые валы, вращающиеся в
подшипниках скольжения |
20, 20Х |
HRC
58—62 Закалка с нагревом т. в.ч. |
Быстроходные и сильнонапряженные
валы |
12ХНЗА,
12Х2Н4А, 18ХГТ |
HRC
60—64 |
Особо
быстроходные валы на подшипниках скольжения при требовании
высокой твердости и износостойкости,
высокого предела выносливости
и прочной
сердцевины |
38ХВФЮ |
HRC
64—67 |
Быстроходные ступенчатые валы в
подшипниках качения |
35 |
Нормализация
НВ>187 |
|
3.24.3 Критерии работоспособности и расчета
валов коробок скоростей и подач
Наиболее важным критерием работоспособности для
большинства валов является выносливость под действием переменных напряжений.
Усталостные разрушения составляют до 40—50% выходов валов из строя. Расчет
валов на выносливость ведется в том случае когда повторяемость длительно действующих
нагрузок не менее 103÷104 циклов. Статическое разрушение
характерно для тихоходных валов, на которые действуют случайные кратковременные
нагрузки, а их повторяемость незначительна. Для длинных валов критериями расчета
являются изгибная и крутильная жесткости вала. При определенных значениях углов
поворота и прогибов может возникнуть недопустимая степень концентрации нагрузки
в зубчатых зацеплениях, нарушение правильной работы подшипников, повышение
интенсивности вибраций. Таким образом, в общем случае валы рассчитываются на
усталостную и статическую прочность и колебания.
3.24.4 Составление расчетных схем
Валы коробок скоростей и подач обычно
рассматриваются как балки на шарнирных опорах, что соответствует наиболее
типичному случаю, когда в каждой опоре устанавливается по одному подшипнику
качения, допускающему поворот или перемещение. Если на вал действует осевая
нагрузка, например, от косозубых, конических, червячных зацеплений, то одну из
опор выполняют шарнирно-неподвижной, другую же шарнирно-подвижной.
Распределенные силы, действующие в зубчатых
зацеплениях, шлицевых соединениях и т. д., заменяются на сосредоточенные,
приложенные по середине длины рабочих поверхностей. Вследствие прогиба валов и
перекоса цапф центр давления в подшипниках скольжения смещается в сторону
нагруженного пролета (рисунок 3.49). Методика построения расчетных схем и
особенности этих схем для валов коробок скоростей и подач, построения эпюр
изгибающих и крутящих моментов изложена в примерах расчета (см.
глава 7).
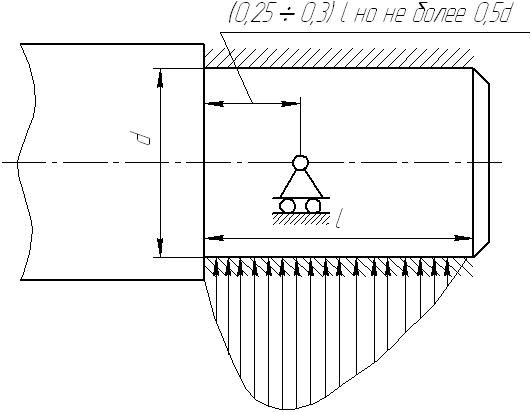
Просмотреть ближе
Рисунок 3.49
- Смещения центров давления в подшипниках скольжения при прогибе вала
3.24.5 Расчеты, валов на прочность
Различают предварительный и основной расчеты
валов на прочность. Для составления расчетных схем необходимо знать расстояния
между опорами и деталями, насаженными на вал, которые зависят от осевых размеров
зубчатых колес, муфт, шкивов, подшипников, в свою очередь зависящих от диаметра
вала. Поэтому посредством предварительного расчета определяется примерный
диаметр вала по условному расчету на кручение без точного учета напряжений
изгиба, поскольку неизвестны величины изгибающих моментов.
Условие прочности на кручение
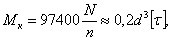
откуда
,
где N— мощность, кВт;
п — частота вращения, об/мин;
d — диаметр вала, см;
[τ]— условное допускаемое напряжение на кручение, кг/см2
При [τ] = 200 кг/см2 ; с = 13.
Для выполнения основного расчета необходимо построить эпюры изгибающих и
крутящих моментов. В общем случае нагрузки, действующие на валы коробок
скоростей и подач, могут быть расположены в различных плоскостях. Для удобства
расчетов силы раскладываются на две взаимно перпендикулярные плоскости, причем
за одну из них принимается та, в которой действует наибольшее число нагрузок.
Часто неясно, при каких включениях зубчатых колес на валы действуют наибольшие
изгибающие моменты, а на их опоры наибольшие силы. В таком случае необходимо
определить реакции опор и построить эпюры изгибающих моментов при различных
включениях зубчатых колес и муфт. Для наглядности расчетов и исключения
возможных ошибок полезно построить компоновочную свернутую схему в изометрии, на
которой следует указать направление векторов сил, действующих на валы, и
компоновочные размеры. Наибольший результирующий изгибающий момент определяется
по уравнению:
,
где МИ и МВ — изгибающие моменты, которые
условно принимаем действующими в горизонтальной и вертикальной плоскостях.
Эквивалентный момент определяется по уравнению
.
Для валов из пластических материалов (углеродистые
и легированные стали) эквивалентное напряжение в опасном сечении определяется на
основании теории наибольших касательных напряжений, тогда уравнение прочности на
одновременное кручение и изгиб будет:
.
Диаметр вала
,
где [σ-1]и-
допускаемое напряжение, устанавливается как при симметричном цикле изгиба:
,
где σ-1— предел выносливости при симметричном цикле
изгиба (таблица 3.57);
Таблица 3.57 - Основные характеристики механической прочности сталей
Марка стали |
Диаметр заготовки, мм до |
Твердость,
не ниже НВ |
Механические характеристики,
кг/мм2 |
σВ |
σТ |
τТ |
σ-1 |
τ-1 |
φσ |
φτ |
Ст. 5
45 |
Любой
Любой
120
80 |
190
200
240
270 |
52
56
80
90 |
28
28
55
65 |
15
15
30
39 |
22
25
35
38 |
13
15
21
23 |
0
0
0,1
0,1 |
0
0
0
0,05 |
40Х |
Любой 200
120 |
200
240
270 |
73
80
90 |
50
65
75 |
28
39
45 |
32
36
41 |
20
21
24 |
0,1 |
0,05 |
40ХН |
Любой
200 |
240
270 |
82
92 |
65
75 |
39
45 |
36
42 |
21
25 |
0,1 |
0,05 |
20
20Х
12ХНЗА
20Х2Н4А
18ХГТ |
60
120
120
120
60 |
145
197
260
300
330 |
40
65
95
125
115 |
24
40
70
107
95 |
12
24
49
75
66,5 |
17
30
42
63
52 |
10
16
21
38
28 |
0
0,05
0,1
0,15
0,15 |
0
0
0,05
0,1
0,1 |
30ХГТ
20ХГБ
18ХНВА
40ХНМА
35 |
Любой
200
150
50
100 |
270
320
415
300
340
300
187 |
95
115
150
100
115
100
52 |
75
95
120
80
85
85
31 |
52
66,5
84
56
58
58
17 |
45
52
65
45
54
45
26 |
26
31
33
27
30
27
13 |
0,1
0,15
0,2
0,1
0,2
0,15
0 |
0,05
0,1
0,1
0,05
0,1
0,1
0 |
|
εα— масштабный фактор для нормальных напряжений (таблице 3.58);
Таблица 3.58 - Значения масштабного фактора
ε в зависимости от диаметра вала
Наибольший из примыкающих к зоне концентрации
диаметров
d,
мм |
Углеродистые
стали |
Лeгиpoвaные стали |
εσ |
ετ |
εσ |
ετ |
20—30
30—40
40—50
50—60
60—70
70—80
80—100
100—120
120—140 |
0,91
0,88
0,84
0,81
0,78
0,75
0,73
0,70
0,68 |
0,89
0,81
0,78
0,76
0,74
0,73
0,72
0,70
0,68 |
0,83
0,77
0,73
0,70
0,68
0,68
0,64
0,62
0,60 |
0,89
0,81
0,78
0,76
0,74
0,73
0,72
0,70
0,68 |
|
β — коэффициент поверхностной чувствительности, зависящий от чистоты и состояния
поверхности, значения которого ориентировочно можно принимать: полирование β —
1,0; шлифование 0,95÷0,98; чистое обтачивание 0,88÷0,94; грубое обтачивание
0,80÷0,86;
kσ — эффективный коэффициент концентрации напряжений;
п — запас прочности.
В связи с тем что в стадии основного расчета валов попутно производится
конструирование их, т. е. устанавливаются диаметры ступеней, форма и размеры
галтелей, выточек, канавок и других конструктивных элементов вала, оказывающих
влияние на концентрацию напряжений, значения kσ
и εα могут приниматься лишь
ориентировочно. По этой причине выбор запаса прочности п и определение
допускаемого напряжения [σ-1]и
носят приближенный характер. Дополнительные погрешности
возникают из-за того, что не учитывается различие в характере циклов нормальных
и касательных напряжений. Указанные причины, понижающие точность расчета [σ-1]и,
приводят к тому, что допускаемые напряжения иногда не рассчитываются по
приведенному уравнению, а принимаются на основании практических данных, например,
для валов из среднеуглеродистой стали
. Основной проектный расчет вала следует
производить попутно с подбором подшипников качения, так как может оказаться, что
по расчетной динамической грузоподъемности подшипника диаметр вала требуется
увеличить по сравнению с тем, который получен при предварительном расчете. Этот
случай характерен для быстроходных валов, передающих сравнительно небольшие
крутящие моменты. Следует отметить большую трудоемкость определения диаметра
вала по методике основного расчета (эквивалентному моменту), в то же время не
дающей желаемой точности результатов. Поэтому в некоторых простейших случаях,
например при расчете валов редукторов, можно ограничиться предварительным
расчетом, а затем произвести расчеты на выносливость, статическую несущую
способность и жесткость.
Проектный расчет завершается вычерчиванием
конструкции вала с указанием размеров ступеней, шпоночных пазов и шлицев,
радиусов галтелей, диаметров поперечных отверстий, размеров выточек, чистоты
обработки поверхностей и способа обработки их, способов термообработки и
упрочняющей обработки посадочных поверхностей и поверхностей, где имеет место
концентрация напряжений, посадок, т. е. всех данных, необходимых для выполнения
расчета вала на выносливость.
3.24.6 Расчеты валов на выносливость
Этот расчет сводится к определению фактических
коэффициентов запаса прочности для нескольких предположительно опасных сечений
вала и сравнению их с допустимыми. Опасным сечением является то, для которого
коэффициент запаса прочности окажется наименьшим. Нередки случаи несовпадения
этого сечения с тем, в котором действует наибольший эквивалентный момент.
Объясняется это концентрацией напряжений и некоторыми другими причинами.
При одновременном действии напряжений изгиба и кручения коэффициент запаса
прочности определяется по уравнению:
,
где nσ— коэффициент запаса усталостной прочности
по изгибу:
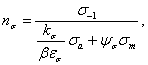
nτ— коэффициент запаса усталостной прочности по
кручению:
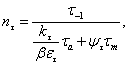
где σa, τa— переменные составляющие циклов (амплитуды
цикла);
σm, τm— постоянные составляющие (средние напряжения цикла);
σ-1, τ-1 — предел выносливости при изгибе и кручении с симметричным знакопеременным
циклом (таблица 3.57);
εσ, ετ — масштабный фактор для нормальных напряжений и напряжений кручения (таблица
3.58);
β — коэффициент влияния на предел усталости состояния поверхности вала (таблица
3.59);
Таблица 3.59 - Коэффициенты
β влияния на величину предела выносливости состояния поверхности вала
Состояние поверхности вала |
Коэффициенты β |
При малой концентрации напряжений
kσ(kτ)≤1,5 |
При большой концентрации напряжений
kσ(kτ)≥1,5 |
Без
специального упрочнения или
термообработки
шероховатость
ниже Ra 1,25
шероховатость
Ra 1,25
и выше |
0,85
1,00 |
0,85
1,00 |
При специальном
упрочнении или термообработке
накатка
стальным роликом |
1,3 |
1,6 |
Обжатие места выхода
поперечного
отверстия (концентратор №19) плоским
пуансоном |
1,4 |
1,4 |
Обдувка струей дроби |
1,5 |
1,7 |
Азотирование,
цианирование, цементация |
1,5 |
1,8 |
Закалка с нагревом т. в. ч. |
1,6 |
2,0 |
|
ψσ, ψτ— коэффициенты, отражающие влияние постоянной
составляющей цикла напряжений на величину предела выносливости.
Значения ψσ
и ψτ для различных марок стали указаны в
таблица 3.57;
kσ, kτ — эффективные коэффициенты концентрации напряжений, величины которых в
зависимости от формы концентратора (рисунок 3.50) приведены в Приложениях
2,
3,
4,
5,
6,
7 ,8.
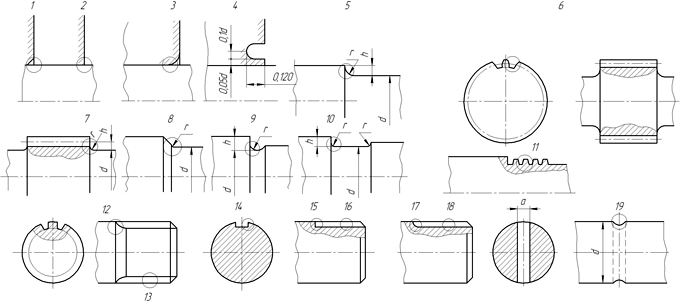
Просмотреть ближе
1, 2, 3, 4 – посадки с гарантированным натягом;
5, 7, 8, 9, 10 – различные галтельные
переходы;
6 – шестерня – вал;
12, 13 – шлицы;
4, 15, 16, 17, 18 – шпоночные
пазы;
9 – поперечное отверстие
Рисунок 3.50
- Основные конструктивные концентраторы
напряжений на валах
Постоянные составляющие σm и τm
определяются при симметричном цикле напряжений изгиба и
при условии, что вал не нагружен осевыми силами:
,
где σи — номинальное напряжение изгиба;
МИ — наибольший изгибающий момент в рассматриваемом сечении;
W — момент сопротивления по изгибу.
Моменты сопротивления сечений валов вычисляются по уравнениям:
вал с прямобочными шлицами
,
где d — внутренний диаметр шлицевого вала;
ξ— поправочный коэффициент, принимаемый для d = 23÷112 мм по следующим данным:
легкая серия—1,09÷1,16; средняя — 1,14÷1,27, тяжелая — 1,14÷1,39. Меньшие
значения соответствуют большим значениям d.
Моменты сопротивления сечений валов с одним
отверстием с отношением
могут
быть определены по уравнениям:
,
где а — диаметр отверстия.
Моменты сопротивления сечений валов с двумя шпоночными пазами могут быть
определены по уравнениям:
.
Моменты сопротивления сечений валов со шпоночным
пазом могут быть определены по уравнениям:
.
Если вал нагружен осевой силой, вызывающей
растяжение, например, вал червяка, то
,
где А — осевая нагрузка.
Если А сжимающая нагрузка, то для циклов со средним напряжением сжатия
принимается ψσ=0.
При нереверсивном вращении напряжения кручения изменяются по пульсирующему циклу.
Поэтому
,
где Мк — наибольший крутящий момент в
рассматриваемом сечении;
Wк — момент сопротивления кручения. При реверсивном вращении
.
При отсутствии табличных данных для
σ-1 и
τ-1 в
зависимости от принятого материала вала можно воспользоваться приблизительными
зависимостями
.
Коэффициенты ψσ и
ψτ вычисляются по уравнениям:
,
где σ0,
τ0 — пределы выносливости материала при
пульсирующем цикле.
Расчет шлицевых валов на изгиб необходимо производить по действительному сечению.
При напрессовке на вал или ось различных деталей резко понижается усталостная
прочность валов и осей, что учитывается введением в расчеты коэффициентов
концентрации, указанных в Приложениях
2,
3,
4.
Если в одном сечении действует несколько источников концентрации напряжений от
формы, то учитывается только один, дающий наибольшую величину коэффициента
концентрации, и, кроме того, учитывается влияние шероховатости поверхности.
Тогда общий коэффициент концентрации будет kσ
+ kσn - 1. Значения kσ и
kσn определяются по таблица
3.60.
Таблица3.60
- Эффективные коэффициенты концентрации напряжений в зависимости
kσ и
kσn от шероховатости
поверхности
Обработка и шероховатость
поверхности |
σВ, кг/мм2 |
40 |
80 |
120 |
kσ и
kσn |
Шлифование Ra 0,32 -
0,16
Обточка Ra
2,5 - 0,63
Обдирка Rz
80 - 20 |
1
1,05
1,20 |
1
1,10
1,5 |
1
1,25
2,2 |
|
Наименьшая величина запаса прочности по пределу
выносливости должна быть не менее того значения, которое допустимо для данных
условий эксплуатации. При отсутствии этих данных для средних условий принимается
п = 1,5÷2,5.
Многие детали станков, в том числе и валы, рассчитываются по длительному (неограниченному)
пределу выносливости с тем, чтобы исключить разрушение валов из-за появления
усталостных трещин.
Следует иметь в виду, что при работе валов в условиях нестационарных нагрузок,
характерных для многих металлорежущих станков из-за непостоянства
технологических процессов, режимов резания и т. п., необходимо учитывать
суммарный эффект на усталостную прочность от действия различных по величине и
продолжительности нагрузок. Расчет валов по наибольшим нагрузкам в предположении
их постоянного действия приводит к неоправданному утяжелению валов и
недостаточному использованию материала.
Методика расчета валов на выносливость,
изложенная выше, не отражает переменности режима нагрузки, характерного для
большинства станков. В этом случае проверочные расчеты необходимо производить по
приведенному напряжению.
Приведенным напряжением называется некоторое
расчетное напряжение, усталостное действие которого дает тот же эффект, который
проявляется в течение фактического числа циклов действительной нестационарной
нагрузки.
Условие прочности:
,
где N0 — число циклов, соответствующее точке
излома кривой усталости (рисунок 3.3), принимается равным 5•106 для небольших сечений и 107
для более крупных сечений;
пiц
— общее число циклов нагружений при напряжении ;
m — показатель степени кривой усталости. Обычно принимается
т = 9, для валов с
прессовыми посадками m = 6, для упрочненных деталей m= 18÷20;
а — коэффициент сопротивления
перегрузкам. Для одноступенчатого изменения напряжений принимается по рисунок
3.51, в остальных случаях — равным 1;
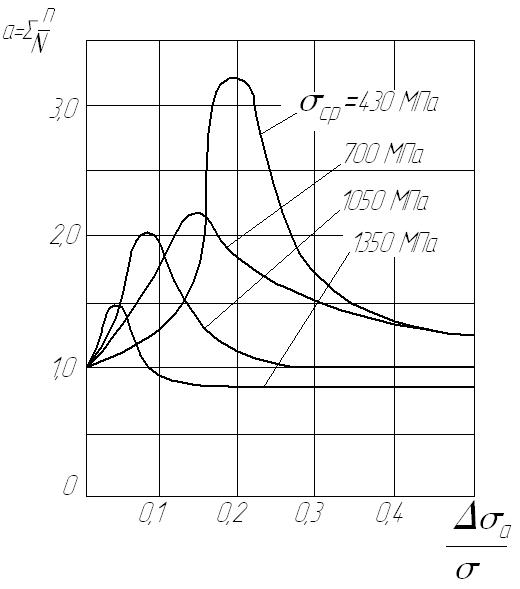
Просмотреть ближе
Рисунок 3.51
- Изменение коэффициента сопротивления перегрузкам а для одноступенчатого
изменения напряжения
σmax — напряжение, определяемое по
наибольшей длительно действующей нагрузке. Пиковые кратковременные перегрузки не
учитываются.
Тяжелонагруженные тихоходные валы коробок
скоростей и подач, для которых не опасно усталостное разрушение, проверяются на
статическую прочность с целью предупреждения малых пластических деформаций в
моменты кратковременных перегрузок например, пусковых, при врезании инструментов,
снятии неравномерных припусков и т. д.
Эквивалентное напряжение определяется по уравнению:
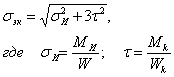
Здесь МИ — суммарный изгибающий момент в опасном
сечении при перегрузке; Мк — крутящий момент в опасном сечении при перегрузке.
Условие прочности σэк
≤[σ]. Обычно принимают [σ]≈0,8σT.
3.24.7 Расчет валов на жесткость
Критериями жесткости валов являются: наибольшие прогибы
и прогибы в местах
посадки зубчатых колес, углы поворота опорных сечений и сечений, совпадающих с
серединами зубчатых венцов, наибольшие углы закручивания, отнесенные к единице
длины пала.
Недостаточная изгибная жесткость вала может вызвать недопустимую концентрацию
нагрузки вдоль контактных линий в зубчатом зацеплении, вследствие чего
понижается несущая способность губчатых передач, увеличиваются кромочные
давления в подшипниках скольжения и при достаточно большом угле поворота (рисунок
3.52) может произойти защемление вала.
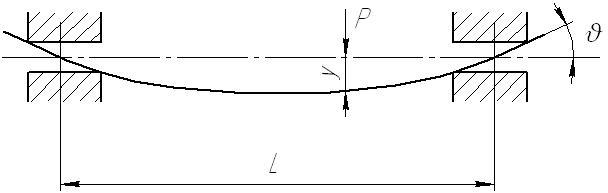
Просмотреть ближе
Рисунок 3.52
- Прогибы и углы поворота вала
При действии нагрузок в разных плоскостях их
раскладывают в двух взаимно перпендикулярных (условно в горизонтальной и
вертикальной) плоскостях и определяют углы поворота отдельно от действия каждой
силы в данном сечении.
Суммарный угол поворота упругой линии вала в горизонтальной и вертикальной
плоскостях определяется по уравнениям:

Полный угол поворота упругой линии вала в
расчетном селении определяется по уравнению:
.
Суммарный прогиб вала определяется по уравнениям:
.
При более сложных схемах нагружения прогибы и
углы поворота определяются с помощью интегралов Мора и способа Верещагина,
рассматриваемых в курсе «Сопротивление материалов». Допустимые прогибы и углы
поворота устанавливаются экспериментально, применительно для конкретных
конструкций, например, для валов зубчатых передач прогиб под шестерней
мм.
Угол взаимного наклона валов под шестернями рад
≤0,001.
В станкостроении для валов коробок передач (кроме шпинделей):
,
где l — расстояние между опорами.
Угол поворота вала в подшипнике скольжения
[θ] = 0,001 рад,
в радиальном шарикоподшипнике [θ]= 0,01 рад.
Крутильная жесткость может ограничиваться требованиями точности работы, главным
образом цепей подач, например, токарно-винторезных и зуборезных станков, степенью концентрации нагрузки по
длине зубьев.
Упругие деформации длинных ходовых винтов и
ходовых валиков могут вызвать скачкообразное перемещение суппортов, кареток и т.
д., что понизит точность изготавливаемых изделий. По этой причине, например,
производится обязательный расчет на жесткость ходовых винтов и валов (см.
п. 3.19).
Проверка на жесткость коротких валов коробок передач необязательна.
Угол закручивания вала постоянного диаметра определяется по уравнению:
,
где G — модуль упругости при сдвиге, кг/см2;
Мк
— крутящий момент, кгс·см;
Iр — полярный момент инерции сечения вала, см4.
Для круглого
сечения
, для сечения, ослабленного шпоночными канавками, правая часть уравнения
умножается на величину
,
здесь n = 0,5 при одной шпонке; n =1,2 при двух
шпонках под углом 180°; h — глубина шпоночной канавки. Момент инерции сечения
шлицевого вала с прямобочными зубьями определяется по приведенному диаметру d +
0,3 (D—d), а при большом числе зубьев— 0,5 (d+D), где d и D — внутренний и
наружный диаметры (принимаются по ГОСТ 1139—80); l — длина закручиваемого
участка вала.
Для ступенчатых валов углы закручивания отдельных ступеней складывают. Общий
угол закручивания определяется по уравнению:
,
где Мкi — крутящий момент, действующий на
i-й
участок, кгс·см;
li — длина i-гo участка вала, см;
di — диаметр г-го участка вала, см.
Допустимое
значение угла закручивания зависит от назначения вала и механизма, в котором вал
работает.
3.24.8 Расчет валов на колебания
Расчет сводится к определению критических чисел
оборотов, при которых вращение валов становится динамически неустойчивым, и
выбору таких размеров вала, при которых бы исключалось явление резонанса, когда
частоты возмущающих сил и собственных колебаний совпадают или кратны.
Во время резонанса амплитуда колебаний резко возрастает, что может явиться
причиной разрушения вала. Угловая скорость, соответствующая состоянию резонанса,
называется критической.
Различают изгибные, крутильные и изгибно-крутильные колебания валов и осей.
Критический режим работы вала может возникнуть, например, в случае недостаточной
сбалансированности деталей, насаженных на вал, и самого вала.
На рисунок 3.53, а показан тот случай, когда центр тяжести вращающейся массы тела G
не совпадает с геометрической осью вращения, а смещен на величину . Пусть под
действием неуравновешенной центробежной силы С при угловой скорости ю вал
прогнулся на величину у (рисунок 3.53, б, в).
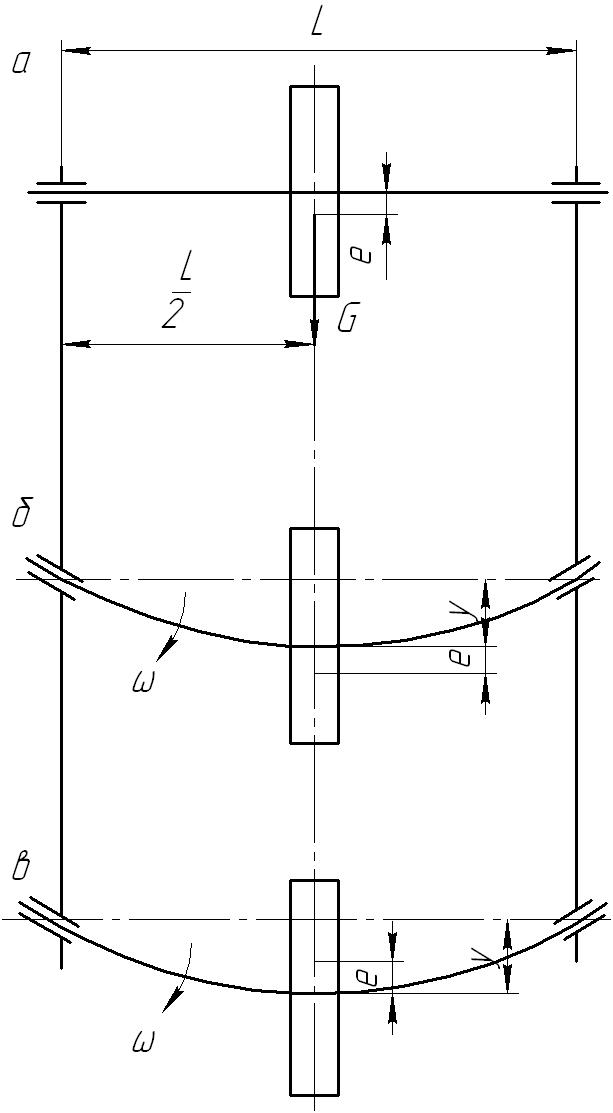
Просмотреть ближе
Рисунок 3.53
- Схема к расчету вала на колебания
Величина центробежной силы .
При установившемся режиме работы сила С
уравновешивается силами упругости вала. В этом случае
,
где К — сила, вызывающая прогиб вала,
равный единице. Из уравнения следует, что
.
Если окажется, что
и
неизбежно произойдет разрушение вала. Поэтому
—
есть критическая угловая скорость.
При симметричном расположении вращающейся массы
относительно опор (рис. 3.53) величина К может быть определена по уравнению:
,
Чаще определяется критическое число оборотов по
уравнению:
.
Величина статического прогиба f определяется по
уравнениям, известным из курса сопротивления материалов.
Из сопоставления уравнений
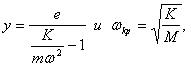
следует, что
.
Если окажется, что ω>ωкр, то прогиб вала начнет уменьшаться и при
ω→∞ y→-e, т. е. центр
тяжести вращающейся массы стремится совпасть с осью вращения вала. Следовательно,
для отсутствия резонанса скорость вращения вала при установившемся движении
должна быть меньше или больше критической скорости. Валы коробок скоростей
работают в до критической области. Во избежание резонанса валов необходимо
повышать их жесткость (уменьшать прогибы), а числа оборотов допускать не более
n=0,7nкр.
3.24.9 Расчет осей
Диаметр оси определяется исходя из условия
прочности на изгиб по уравнению:
,
где [σ]и—допускаемое напряжение на изгиб,
зависящее от материала и условий нагружения оси. Для вращающихся осей
допускаемые напряжения такие же, как и для валов.
Последовательность расчета:
1. Определяются действующие на ось усилия, и вычерчивается схема нагружения.
Вращающаяся ось рассматривается как балка на шарнирных опорах, не вращающаяся —
как балка, заделанная обоими концами.
2. Строят в двух плоскостях эпюры изгибающих моментов и находят значение
результирующего изгибающего момента в опасном сечении.
3. По характеру действующих нагрузок и выбранному материалу определяют
допускаемые напряжения.
4. По результирующему моменту и допускаемому напряжению определяют диаметр оси в
опасном сечении.
Если в опасном сечении оси имеются шпоночные канавки, необходимо компенсировать
ослабление сечения увеличением расчетного диаметра на 8÷10%.
Для изготовления осей применяются те же материалы, что и для валов.
3.24.10 Практические меры, повышающие
усталостную прочность валов и осей
На усталостную прочность валов и осей оказывают
совместное влияние многочисленные технологические особенности изготовления и
конструктивные разновидности отдельных элементов валов и осей. Укажем на
наиболее важные из них. Как известно, концентрация напряжений создает
благоприятные условия для возникновения и развития трещин усталости и сильно
снижает величину предела выносливости. На валах и осях всегда имеются
конструктивные концентраторы напряжений, показанные на рисунок 3.50.
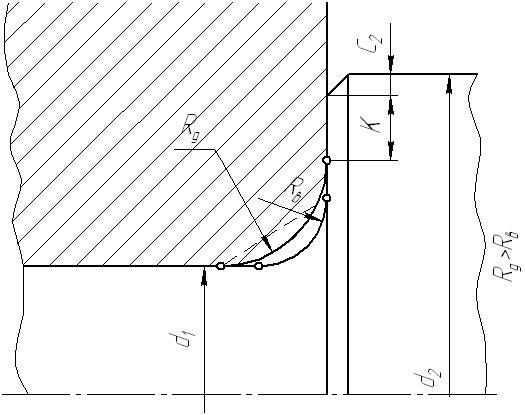
Просмотреть ближе
Рисунок 3.54 - Галтель постоянного радиуса
Конструктор всегда имеет возможность путем
изменения очертаний концентраторов напряжений существенно повысить равномерность
распределения напряжений в опасных сечениях и тем самым увеличить усталостную
прочность валов. При увеличении разности диаметров смежных ступеней повышается
концентрация напряжений, поэтому необходимо стремиться к наименьшей разности
диаметров. Если на валу необходим упор (рисунок 3.54), то диаметр смежной большой
ступени
,
где RД — радиус закругления или катет фаски в
отверстии парной детали, определяемый из условия RД> RB ,
RB — радиус галтели вала. В сильно напряженных валах
желательно принимать
;
d1
— диаметр меньшей ступени;
k — ширина кольцевой опорной площадки, определяемая из условия прочности на
смятие в случае действия осевых усилий, обычно принимается k = 1,5 + 2,0 мм;
с2— катет фаски вала.
Если заплечик или бурт не нужен (рисунок 3.55), то d2 = d1 + 2×(Rв + с2).В случае
посадки подшипников качения d2 = d1 + 2 h,
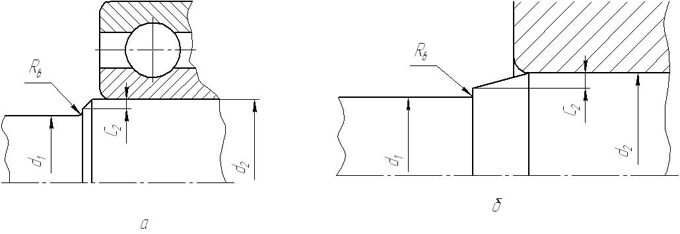
Просмотреть ближе
а – посадка
деталей при небольшом отношении
;
б – посадка
деталей при большом отношении

Рисунок 3.55 - Посадка деталей без упора
где h — высота заплечика (рисунок 3.56, а), которая должна приниматься в
соответствии с нормалями.
Если смежные ступени вала окажутся такими, что размер h будет меньшим, чем это
предусмотрено нормалями, то применяют промежуточное упорное кольцо (рисунок 3.56,
б). Радиус закругления упорного кольца меньший, чем у соответствующих
подшипников, что дает возможность понизить высоту заплечика h, а следовательно,
уменьшить разность диаметров смежных ступеней. В тех случаях, когда невозможно
получить небольшую разность диаметров смежных ступеней и тем самым избежать
увеличения концентрации напряжений, выполняют плавные переходы между ступенями в
виде конических участков, а для упора применяют промежуточные втулки.
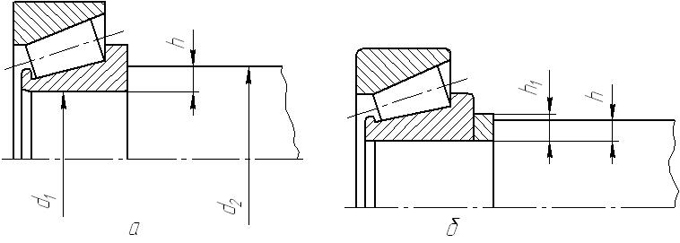
Просмотреть ближе
Рисунок
3.56 - Высота заплечика при посадке подшипников качения
Иногда венцы зубчатых колес изготавливают заодно с валом. Для уменьшения
концентрации напряжений, вызываемых большой разностью диаметров смежных ступеней,
вал необходимо выполнять ступенчатым (рисунок 3.57).
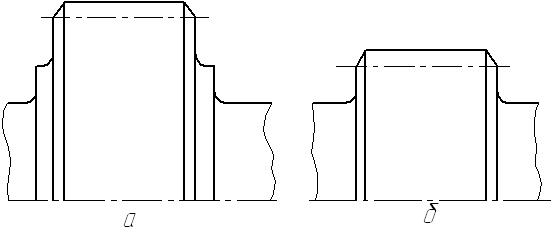
Просмотреть ближе
а –
ступенчатый переход с двумя ступенями;
б –
ступенчатый переход с одной ступенью
Рисунок 3.57
- Ступенчатые переходы от зубчатого венца к валу
Канавки под пружинные стопорные кольца и для выхода -шлифовальных кругов
ослабляют сечение детали, понижают ее прочность и вызывают резкую концентрацию
напряжений. Эти канавки должны иметь возможно большие радиусы закруглений.
Применение их допустимо для не вращающихся осей, несущих статическую нагрузку,
для концевых участков валов, на которых изгибающие моменты невелики, и для валов
коробок передач, если их диаметры определены условиями жесткости.
Целесообразно для осевой фиксации зубчатых колес
применять вместо пружинных стопорных колец распорные втулки, винты и другие
средства.
Канавки со скруглением при точеном торце (рисунок 3.58, а) и при шлифованном торце
(рисунок 3.58, б), выполняемые в соответствии с ГОСТ 8820—69, позволяют понизить
концентрацию напряжений. С увеличением отношения
(рисунок 3.54) концентрация
напряжений уменьшается, поэтому для тяжелонагруженных участков валов применяют
плавные галтели переменного радиуса (рисунок 3.59, а).
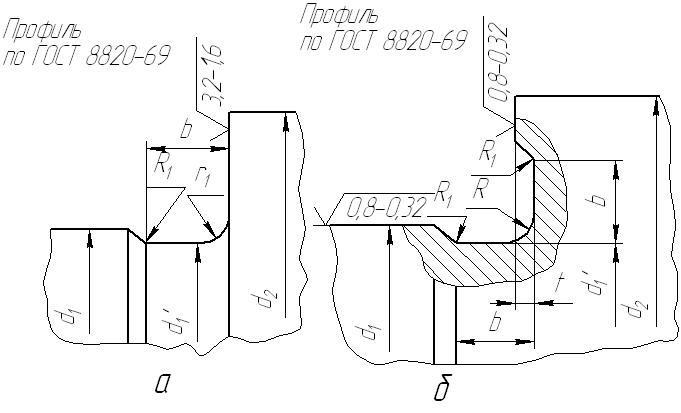
Просмотреть ближе
Рисунок 3.58
- Канавки для понижения концентрации напряжений
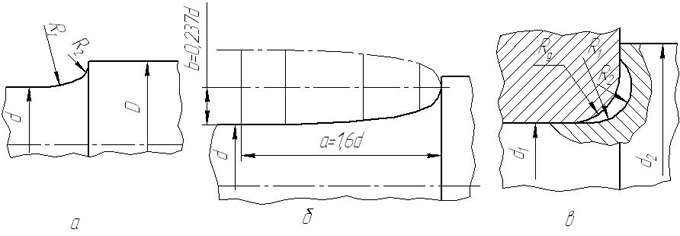
Просмотреть ближе
Рисунок 3.59 - Очертания галтелей
В тех случаях, когда позволяют габариты, особенно эффективно применение галтелей
эллиптического профиля (рисунок 3.59, б), почти полностью устраняющих концентрацию
напряжений. Галтели с поднутрением (рисунок 3.59, в) значительно понижают степень
концентрации напряжений и не вызывают увеличения габаритов вала. Однако
эффективность применения галтели этого вида может значительно понизиться при
недостаточно тщательной обработке ее поверхности. Обычно принимают отношение

Достигается увеличение предела выносливости до 30 %. Для более равномерного
распределения напряжений, а следовательно, понижения эффективного коэффициента
концентрации напряжений следует стремиться к уравнению жесткостей смежных
участков вала. С этой целью выполняются плавные канавки на более жесткой части
вала (рисунок 3.60).
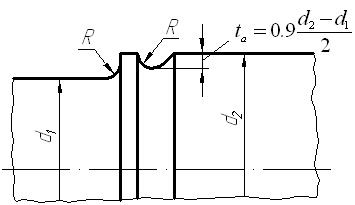
Просмотреть ближе
Рисунок 3.60
- Разгружающая канавка
При посадке с натягом на вал или ось зубчатых
колес, муфт, шкивов, подшипников качения и т. д. резко снижается сопротивление
усталости вала или оси.
Усталостные трещины зарождаются у края контакта соприкасающихся поверхностей.
Причинами снижения предела выносливости при посадках с натягом являются
концентрация напряжений у кромки контакта и наличие так называемой коррозии
трения, электроэрозионного разрушения и механического истирания поверхностей. Все это способствует образованию и развитию трещин усталости даже при
весьма низких номинальных напряжениях. Посредством поверхностного упрочнения
обкаткой шариками — роликами, обдувкой дробью, цементацией и т. д. пределы
выносливости валов с прессовыми посадками можно повысить в 2—3 и более раз. С целью повышения выносливости валов в местах посадок деталей с натягом
необходимо стремиться к уменьшению давлений у края контакта, чего можно
достигнуть в определенной мере, применяя конструкции, показанные на рисунок 3.61.
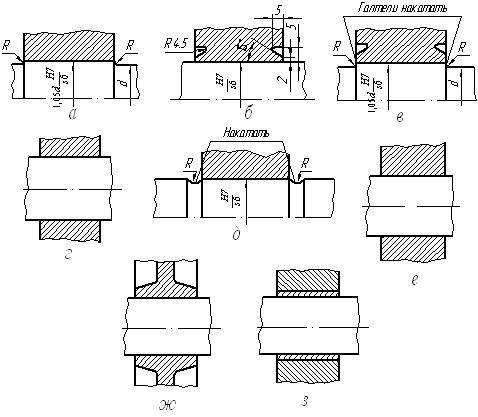
Просмотреть ближе
Рисунок 3.61
- Повышение усталостной прочности валов и осей в местах посадок с натягом
Так, например, утолщение подступичной части вала на 5 % по сравнению со смежным
участком вала (рисунок 3.61, а) или проточка разгрузочной канавки в торце ступицы (рисуно
3.61, б) повышают предел выносливости вала до 30 %, а совместное применение
разгрузочной канавки в торце ступицы и плавный переход от одной ступени вала к
другой (рисунок 3.61, в) повышают предел выносливости вала до 70—90 % по
сравнению с конструкцией, изображенной на рисунок 3.61, г.
Понижения предела выносливости тяжелонагруженных валов в местах посадок с
натягом можно почти полностью избежать, если применить совместно разгрузочные
канавки (рисунок 3.61, д), обкатку и разгрузочные канавки в торце ступицы.
Значительного понижения концентрации напряжений можно достичь, применив
закругление кромок ступицы (рисунок 3.61, е) и утонение ступицы (рисунок 3.61, ж).
Применение втулки или заливки из материала с низким модулем упругости (рисунок
3.61, з) также понижает кромочное давление и концентрацию напряжений.
Если консоль вала нагружена крутящими и
изгибающими моментами, например, на консоли посажены шкивы, звездочки и т. д.,
то для уменьшения концентрации напряжений следует длину посадочной ступени вала
под подшипник увеличить на 3—4 мм по сравнению с шириной кольца подшипника (рисунок
3.62). Усталостную прочность валов можно повысить, придавая им ступенчатую форму,
причем с таким расположением ступеней и размерами их по диаметру и длине, чтобы
путь, проходимый деталью под усилием запрессовки, был возможно короче. Каждая
деталь до своей ступени должна перемещаться свободно, при этом смежные ступени
следует выполнять с возможно меньшей разностью их диаметров.
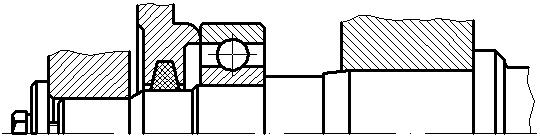
Просмотреть ближе
Рисунок 3.62
- Правильная посадка подшипника: посадочная ступень вала длиннее кольца
подшипника
Весьма сильное влияние на усталостную прочность оказывает качество обработки
поверхностей валов, особенно мест с высокой концентрацией напряжений. Следы
резцов, риски, царапины, вмятины, прижоги, шлифовочные трещины и т. д. на
поверхности вала, где действуют наибольшие напряжения изгиба и кручения, часто
являются зародышами усталостных трещин.
Следует отметить, что легированные стали с высоким пределом прочности, мало
склонные к перераспределению напряжений в зоне концентрации, а следовательно, к
смягчению концентрации напряжений, резко понижают предел выносливости при
наличии даже незначительных дефектов на поверхности. Поэтому при использовании
высокопрочных легированных сталей для производства валов конструктивные
концентраторы напряжений должны особенно тщательно шлифоваться или полироваться,
иначе нецелесообразно применение дорогостоящих легированных сталей.
Максимальные напряжения у валов возникают на их поверхности, где напряжения
кручения и изгиба достигают наибольшей величины. Поэтому с целью повышения
усталостной прочности валов применяются различные технологические способы
упрочнения поверхностного слоя, основными из которых являются: химико-термическая
обработка (азотирование, цементация, цианирование и т. п.), поверхностная
закалка с нагревом т. в. ч. и т. д.
На рабочем чертеже вала следует указывать способы повышения усталостной
прочности, например: закалить с нагревом т. в. ч и полировать.
|