3.3 Определение
расчетных нагрузок.
Прочность деталей коробок скоростей и подач
Проектирование коробок скоростей и подач должно начинаться с разработки
технологических процессов обработки деталей на станках, которые, как правило,
отличаются большим разнообразием. На детали механизмов передач станков действуют
нагрузки различной продолжительности, изменяющиеся в широких пределах по
величине и характеру; причем величины нагрузок и длительность действия их
различны. По исследованиям ЭНИМС, для средних условий эксплуатации
универсальных станков длительность работы станка при передаче различных нагрузок
составляет: 60-80 % при передаче мощности до 0,25 N, 80-90 % до 0,5 N и 1-5 % с
превышением N. Переменность режима нагрузки можно выразить графиком нагрузки
(рисунок 3.1), который в большинстве случаев построить трудно, так как
продолжительность действия и величина каждой ступени нагрузки весьма
разнообразны и трудно поддаются учету. За время t одного рабочего цикла
изменения нагрузок может быть принят любой промежуток времени, в течение
которого проявляются все возможные нагрузки по величине и длительности, которые
затем вновь повторяются. В продолжительность времени цикла изменения нагрузок не
включается время действия пиковых, например, пусковых кратковременно действующих
нагрузок. За номинальную расчетную нагрузку, принимаемую по графику, берется
наибольшая длительно действующая нагрузка.

Рисунок 3.1 - График нагрузки
Просмотреть ближе
Рис. 3.1. График нагрузки
В расчетные уравнения подставляются значения расчетной нагрузки, которая
выражается чаще всего произведением номинальной расчетной нагрузки Мк на
коэффициент нагрузки k, который учитывает повышение нагрузки, вызванное
внутренними процессами в передачах. Например, коэффициент нагрузки при расчете
зубчатых передач учитывает повышение нагрузки вследствие концентрации ее вдоль
контактных линий и внутренней динамики передачи.
Влияние переменности напряжений на несущую способность деталей учитывается
при определении допускаемых напряжений (см.
п. 3.15).
В деталях машин могут возникать постоянные напряжения, вызываемые статической
нагрузкой, стационарные переменные напряжения, вызываемые постоянной нагрузкой,
например напряжения изгиба в валах, зубьях зубчатых колес при действии
постоянных нагрузок, и нестационарные напряжения, вызванные переменной
нагрузкой. Большинство деталей машин работает при переменных напряжениях с
различными частотами и амплитудами. В современных машинах статические нагрузки
встречаются редко, о чем свидетельствует хотя бы тот факт, что не менее 80 %
поломок и аварий, происходящих при эксплуатации машин, связано с переменными
напряжениями, вызывающими разрушения усталостного характера.
Прочностные расчеты на усталость (выносливость ) могут выполняться в двух
направлениях: по ограниченному пределу выносливости (рисунок 3.2) на определенный
(ограниченный) срок службы детали и по неограниченному пределу выносливости
(рисунок 3.3) с тем, чтобы исключить возможность усталостной поломки детали в
течение всего времени эксплуатации машин. Детали коробок скоростей и подач
металлорежущих станков рассчитываются, как правило, по неограниченному пределу
выносливости. Поломки деталей из-за появления усталостных трещин не допустимы. По
кривой усталости (рисунок 3.3), состоящей из двух ветвей - левой криволинейной,
соответствующей ограниченной долговечности, и правой прямолинейной части,
соответствующей неограниченной долговечности, можно определить долговечность (в
циклах), которую будут иметь детали, погруженные напряжениями выше предела
усталости, или напряжениями, являющимися предельными при заданной долговечности.
При определенном числе циклов нагружения с перегрузками, гораздо меньшим
базового числа циклов N0 (рисунок 3.2), в детали могут возникнуть
повреждения, в результате чего она становится непригодной для дальнейшей
эксплуатации. Разрушение детали происходит при напряжениях, значительно меньших
тех, которые возникли при перегрузках. Следует иметь в виду, что различные
материалы при разной термообработке способны по-разному накапливать повреждения,
и значит, по-разному переносить перегрузки. Например, отожженные углеродистые
стали совершенно не переносят перегрузку, и значит, расчеты деталей,
изготовленных из таких сталей, следует производить только по ограниченному
пределу выносливости.

Просмотреть ближе
Рисунок 3.2 - График кривой без длительного
предела выносливости
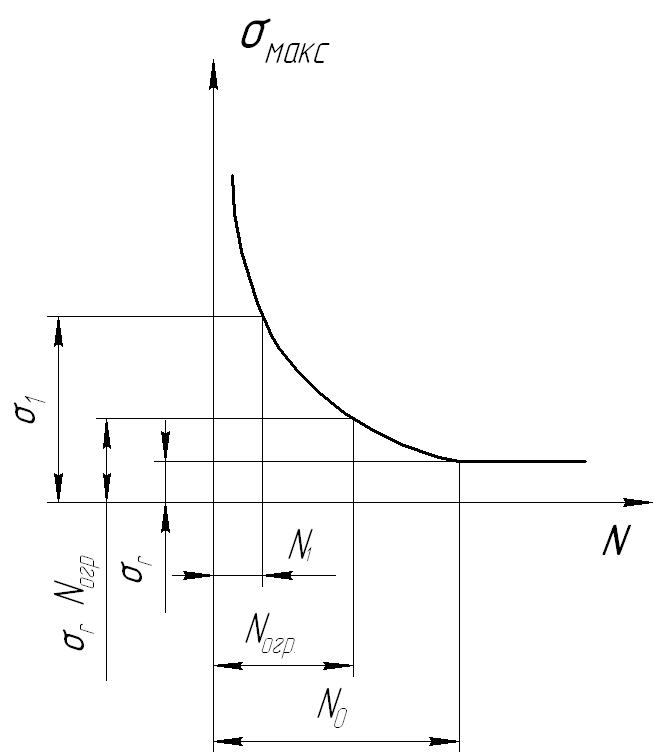
Рисунок 3.3 - График
кривой с делительным пределом выносливости
Просмотреть ближе
Расчеты на выносливость при нестационарных переменных напряжениях базируются
на уравнении суммирования повреждений:
,
где nц i - общее число циклов действия некоторого напряжения σt;
Nц i - число циклов до разрушения при том же напряжении;
а - экспериментальный коэффициент, характеризующий сопротивление нагрузкам,
и как правило, близкий к единице.
Методика этого расчета наиболее полно изложена в работе.
Кроме того, по ограниченному пределу выносливости должны рассчитываться
детали в следующих случаях:
а) если они изготовлены из материалов, не имеющих четко выраженного предела
усталости или имеющих резко падающую кривую усталости (высоколегированные стали,
чувствительные к концентрации напряжений);
б) если они работают при напряжениях с низкой частотой циклов;
в) когда они работают с периодическими длительными перерывами или при малых
нагрузках с общим числом циклов за весь срок амортизации, меньшим базового числа
циклов N0;
г) когда их габариты или вес ограничиваются условиями компоновки.
На величину предела выносливости оказывают влияние многие факторы, важнейшими
из которых являются: условия нагрузки, коэффициент асимметрии цикла, форма и
абсолютные размеры детали, микрогеометрия поверхности, качество поверхностного
слоя материала детали, технология изготовления. Важнейшее влияние на усталостную
прочность оказывают перегрузки, возникающие при эксплуатации детали.
Усталостная прочность деталей значительно понижается при наличии концентрации
напряжений, которые могут вызвать повышение напряжений в 2-3 раза по сравнению с
их номинальным значением, определяемым по уравнениям, известным из курса
сопротивления материалов. Концентрацию напряжений могут вызвать многие причины
конструктивного и технологического характера, поэтому принято различать
геометрические и технологические концентраторы напряжений. При расчетах на
прочность влияние концентрации напряжений учитывается теоретическими или
эффективными коэффициентами концентрации напряжений. Первый определяется
отношением наибольшего местного напряжения (не большего предела упругости) к
величине номинального напряжения:
,
где σmax
- теоретическое максимальное напряжение, определяемое
методами математической теории упругости или экспериментально поляризационно-оптическими методами;
σном - номинальное напряжение, определяемое по уравнениям,
известным из курса сопротивления материалов.
Этот коэффициент отражает лишь влияние формы концентратора на величину
местных напряжений.
Второй определяется отношением предела выносливости при симметричном цикле
гладкого образца к пределу выносливости при симметричном цикле образца того же
диаметра, но с концентрацией напряжений:
.
Этот коэффициент отражает влияние формы концентратора, материала, абсолютных
размеров, коэффициента асимметрии цикла, состояния поверхности и других
факторов.
Наиболее надежное значение эффективного коэффициента концентрации напряжений
можно получить только из опыта на натурных объектах. Величина максимальных
напряжений в зоне концентрации зависит от характера нагрузки. При действии
статической нагрузки у пластичных материалов концентрация напряжений проявляется
незначительно. Это объясняется тем, что в зоне концентрации при достижении
напряжений, равных пределу текучести, происходит значительное выравнивание
напряжений за счет пластических деформаций. Поэтому для высокопластичных
материалов можно принимать kσ, а для хрупких эффект уравнения
напряжений не проявляется и поэтому можно в расчетах принимать kσ = kТ.
При переменных нагрузках концентрация напряжений сказывается сильнее.
Для расчетов можно воспользоваться соотношениями:
легированная сталь kσ = (0,85 ÷ 0,9) kТ;
углеродистая и низколегированная сталь kσ = (0,75 ÷ 0,8) kТ.
Пpи отсутствии экспериментально установленных величин эффективных
коэффициентов концентрации напряжений их можно определять по уравнению:
kσ = 1+q( kТ – 1),
где q - коэффициент чувствительности материала к концентрации напряжений при симметричном цикле.
Для высокопрочных легированных сталей, склонных к концентрации напряжений, q
≈ 1. Для конструкционных сталей в среднем q = 0,6-0,8, причем для более прочных
сталей q = 0,8; для низко-углеродистых сталей q = 0,5. Для чугуна q = 0.
Эффективное использование чувствительных к концентрации высокопрочных сталей
для производства деталей коробок скоростей и подач, работающих при переменных
нагрузках, может быть достигнуто лишь в том случае, когда будут в значительной
мере устранены геометрические и технологические причины, вызывающие концентрацию
напряжений.
Увеличение плавности переходов, уменьшение перепадов смежных сечений,
ослабленных и неослабленных участков детали, улучшение чистоты обработки,
равномерность толщины слоя, упрочненного термообработкой, и другие меры
способствуют понижению концентрации напряжении. Из уравнения следует, что
понизить максимальные напряжения на участке концентрации при данном Кσ можно с
помощью мер, способствующих уменьшению σном. К числу этих мер можно
отнести увеличение поперечных сечений и моментов сопротивлений ослабленных
сечений, а также уменьшение действующих нагрузок. При совместном использовании
указанных конструктивных и технологических мероприятий можно почти полностью
устранить концентрацию напряжений, и в таких случаях применение концентрационно
чувствительных высокопрочных легированных сталей будет вполне оправдано.
|