7.2.3 Расчет
валов
7.2.3.1 Выбор
материала валов
Для правильного выбора материалов валов и
термообработки их необходимо знать: тип подшипников, в которых вращается вал,
характер посадок деталей на валу (подвижные или с натягом), характер
действующей нагрузки.
Первый вал наиболее быстроходный, вращается в
подшипниках качения. На валу на игольчатых подшипниках качения вращаются
зубчатые колеса z1
и
z2.
Многодисковая фрикционная муфта сцепления установлена на шлицах по переходным
посадкам. Наиболее подходящим материалом вала для этих условий является сталь
40Х (таблица 3.56). Термообработка — закалка трущихся
поверхностей с нагревом т. в. ч. до
HRC
52—56. Механические свойства этой стали принимаем по
таблице
3.57.
σВ
= 9000 кг/см2;
σT
= 7500 кг/см2;
σ-1
= 4100
кг/см2;
τ-1
= 2400 кг/см2;
τT
= 4500 кг/см2;
ψσ
= 0,1; ψτ
= 0,05.
Второй вал вращается
также в подшипниках качения. Зубчатые колеса
z3,
z4,
z5,
z6,
z7
посажены на вал на шпонках по переходным посадкам. Наиболее подходящим
материалом для этих условий является сталь 45 с твердостью НВ 220—260.
Механические свойства этой стали принимаем
σВ
= 5600 кг/см2;
σT
= 2800 кг/см2;
σ-1
= 2500 кг/см2;
τ-1
= 1500 кг/см2;
τT
= 1500 кг/см2;
ψσ
= 0;
ψτ
= 0.
Третий вал имеет шлицы, по которым перемещается
блок зубчатых колес z8 —
z9 — z10.
Вал вращается в подшипниках качения. Для
обеспечения достаточной износостойкости трущихся поверхностей шлицев принимаем
сталь 20Х (таблица 3.56). Термообработка — цементация и
закалка трущихся поверхностей до HRC 58—62. Механические свойства этой стали
принимаем
σВ = 6500
кг/см2; σT
= 4000 кг/см2; σ-1
= 3000 кг/см2;
τ-1 = 2400
кг/см2; τT
= 1600 кг/см2; ψσ
= 0,05; ψτ
= 0.
Четвертый вал вращается в подшипниках качения.
Зубчатое колесо z11 посажено на вал на
шпонке по ходовой посадке. Для этого вала наиболее подходящей является сталь
40Х нормализованная. Термообработка производится до окончательной обработки
вала, так как при значительной длине его (1200 мм) при нагревании возможно
коробление. Механические свойства этой стали принимаем по
таблице 3.57 при твердости не ниже НВ 270:
σВ = 9000
кг/см2; σT
= 7500 кг/см2; σ-1
= 4100 кг/см2;
τ-1 = 4500
кг/см2; τT
= 2400 кг/см2; ψσ
= 0,1; ψτ
= 0,05.
Выбор материала для пятого вала и расчет его
произведен при расчете червячной передачи.
Шестой вал выполнен заодно с шестерней z15.
На валу на шпонке по переходной посадке посажено червячное колесо. Вал
вращается в подшипниках качения. Наиболее подходящей для этих условий является
сталь 40Х (таблица 3.56). Термообработка — закалка
зубчатого венца с нагревом т. в. ч. до HRC 52—56. Механические свойства этой
стали принимаем
σВ = 9000
кг/см2; σT
= 7500 кг/см2; σ-1
= 4100 кг/см2;
τ-1 = 4500
кг/см2; τT
= 2400 кг/см2; ψσ
= 0,1; ψτ
= 0,05.
Построение компоновочных схем коробки подач и
суппорта.
Для расчета валов и подбора подшипников
необходимо вычислить реакции опор и изгибающие моменты, действующие в различных
сечениях валов. Эта задача может быть выполнена лишь в том случае, когда будут
известны расстояния между плоскостями действия нагрузок и опорами.
Для нахождения этих расстояний необходимо вычертить в произвольном масштабе
эскизную компоновку коробки подач в виде развертки по осям и свертки (рисунки 7.29, 7.32). При выполнении компоновочной схемы необходимо учесть рекомендации,
данные в примере расчета коробки скоростей (п.
7.1.3).
На основании указанных рекомендаций
компоновочную схему разрабатываем в следующем порядке:
1) проводим оси валов, причем межосевые
расстояния, полученные при расчете зубчатых передач, откладываем в определенном
масштабе;
2) предварительно определяем диаметры валов.
Для составления расчетных схем необходимо знать расстояния между плоскостями
действия сил, которые зависят от осевых размеров муфты, зубчатых колес,
подшипников и т.д., которые в свою очередь зависят от диаметра вала. Поэтому
диаметры вала могут быть определены лишь предварительно по условному расчету на
кручение по уравнению

Диаметр первого вала
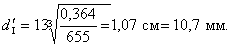

Просмотреть ближе
Рисунок
7.32 - Компоновочная схема коробки подач
Для обеспечения свободного прохода подшипников и
муфты на посадочные места вал следует выполнить ступенчатым. Поэтому диаметр
шейки вала под подшипник увеличиваем до большего стандартного диаметра
внутреннего кольца подшипника (ГОСТ 8338—75) dI
= 17 мм.
Диаметр второго вала
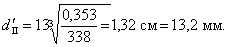
Предварительно принимаем dII
=17 мм, и этот размер принимаем за диаметр шеек вала под подшипники.
Диаметр третьего вала

Предварительно принимаем диаметр шейки вала под
подшипник 15 мм.
Для обеспечения свободного прохода блока
зубчатых колес на шлицевой участок вал следует выполнить ступенчатым. Наружный
диаметр шлицевого участка вала увеличим до ближайшего стандартного значения
(ГОСТ 1139—80) dIII =20 мм и по
этому диаметру подбираем подшипники.
Четвертый вал (ходовой) работает только на
скручивание. Диаметр этого вала

Предварительно округляем dIV
до ближайшего значения по ГОСТ 8338—75 на подшипники и принимаем за
диаметры шеек вала под подшипники d=17 мм.
Диаметр шестого вала
.
Предварительно принимаем в соответствии с
указанным стандартом на подшипники диаметр шеек под подшипники для шестого вала

В зависимости от этих диаметров внутренних колец
подшипников выписываем из таблиц стандарта диаметры наружных колец D и
ширины колец B (размеры в мм).
d
— 17 17 15 20 17 35; D — 40 40 35 48 40 72; В — 12 12 11 14 12
23.
При последующем основном расчете валов эти
диаметры могут быть изменены в большую или меньшую сторону.
Выбираем способ смазки подшипниковых узлов и
зубчатых зацеплений. В данном случае подшипники должны смазываться масляным
туманом, образуемым внутри корпуса коробки подач. Поэтому подшипники не
закрываются со стороны внутренней полости корпуса. Расстояние между средней
плоскостью клиноременного шкива, в которой действует нагрузка на вал от ременной
передачи, и средней плоскостью подшипника определяется в зависимости от
конструкции уплотняющих устройств, размеров сквозной крышки и конструкции
ограждения для ременной передачи (рисунок 7.33).
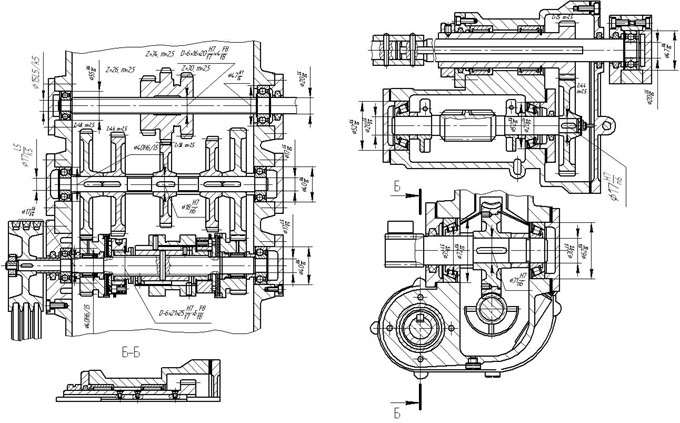
Просмотреть ближе
Рисунок 7.33
- Общий
вид коробки подач
Определяем в зависимости от диаметра вала и
конструктивных особенностей деталей передач длины ступиц зубчатых колес,
шкивов, фрикционной муфты. Переключение блоков шестерен z8
— z9 — z10 осуществляется с помощью вилки. В таком случае
ширина блока складывается из ширины зубчатых венцов z8, z9
и z10, ширины проточки для выхода долбяка b1=6
мм и ширины проточки для вилки переключения b2=11
мм.
B=17+6+14+11 + 15=63 мм.
Этот же размер принимаем за длину ступицы блока,
но так как рекомендуемая длина последней

то в средней части блока делаем выточку (см. рисунок
7.33), которая, не ослабляя шлицевого соединения, способствует повышению
долговечности протяжек.
Предварительно подбираем размеры муфты,
смонтированной внутри коробки, в зависимости от диаметра вала и передаваемой
нагрузки. В данном случае осевые размеры фрикционной муфты определяются в
зависимости от осевых размеров деталей, посаженных на II
вал, и осевых размеров деталей самой фрикционной муфты.
Принимаем зазор между торцами цилиндрических
зубчатых колес и внутренней стенкой корпуса равным толщине стенки корпуса,
причем толщину стенки принимаем δ = 0,025 a + 5
мм, где а — большее из межосевых расстояний, мм.
В нашем случае

Принимаем δ
=8 мм.
Расстояние между торцами зубчатых колес не
должно превышать 4—6 мм, а расстояние между торцами зубчатых блоков и
неподвижных колес следует принимать 3—4 мм.
По найденным осевым и радиальным размерам
деталей коробки подач, а также монтажным размерам (расстояния между различными
деталями) вычерчивается развертка. Одновременно вычерчиваем свертку коробки,
руководствуясь ранее изложенными рекомендациями (см. рисунки 7.29, 7.32). При
последующем основном расчете валов чертеж свертки необходим для вычерчивания
расчетных схем валов. По свертке определяются направления радиальных и окружных
усилий, действующих в зубчатых зацеплениях, а также направление силы,
действующей на вал от ременной передачи (см. рисунок 7.32).
Следует иметь в виду, что в результате
предварительной компоновки деталей на валах коробки подач мы получаем
необходимые нам расстояния между плоскостями действия сил лишь ориентировочно,
по той причине, что размеры опор, муфт, зубчатых колес, регулировочных
и крепежных средств зависят и устанавливаются по диаметру вала. Последний
может быть определен более точно по эквивалентному моменту только после
вычерчивания развертки, необходимой для составления расчетных схем.
7.2.3.2
Основной расчет валов
Для каждого вала составляем расчетные схемы в
соответствии с нагрузками, действующими в зубчатых зацеплениях при различных
положениях колес и муфты, что дает возможность выявить наиболее тяжелый случай
нагружения вала.
При этом расчете вычерчиваем схему нагружения
вала с изображением векторов сил, действующих на вал со стороны зубчатых и
ременной передач. В обозначениях сил, возникающих в зубчатых зацеплениях, первый
индекс обозначает номер колеса, на которое действует сила, второй — номер
колеса, со стороны которого действует сила.
На расчетных схемах вычерчиваем эпюры
изгибающих, крутящих и эквивалентных моментов. Для удобства построения эпюр
изгибающих моментов на схемах нагружения валов указываем активные силы и реакции
опор в цифровом виде. Затем непосредственно определяем изгибающие моменты в
сечениях под силами, не прибегая к составлению уравнений моментов.
7.2.3.2.1 Расчет I
вала
Из рассмотрения компоновочной схемы (рисунок 7.32)
видно, что расстояния между средними плоскостями подшипников и зубчатых венцов
колес z1 и z2 почти одинаковы и
равны соответственно 21,5 мм и 22,5 мм. Поскольку делительные диаметры колес
z1 и z2 отличаются
незначительно, поэтому окружное и распорное усилия, действующие на эти колеса,
будут соответственно почти одинаковыми. Если в зацеплении находится пара колес
z1 —z7, то реакция на ближайшую
опору будет наибольшей, что видно из компоновочной схемы (рисунок 7.32), поэтому за
расчетный случай принимаем тот, когда в зацеплении находятся колеса
z1 —z7. Этот вывод
подтверждается вычислениями.
Максимальный крутящий момент, передаваемый
I валом:
.
Усилия в зацеплении z2—z3:
окружное
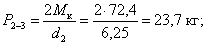
распорное T2-3
= P2-3 · tg α = 32,7 · 0,364
= 8,62 кг.
Усилия в зацеплении z1—z7:
окружное
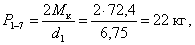
распорное

Так как усилия в зацеплениях
z1—z7 и z2—z3
различаются незначительно, то дальнейший расчет ведем по зацеплению
z1—z7.
Определяем опорные реакции.
В вертикальной плоскости (рисунок 7.34)


Проверка:

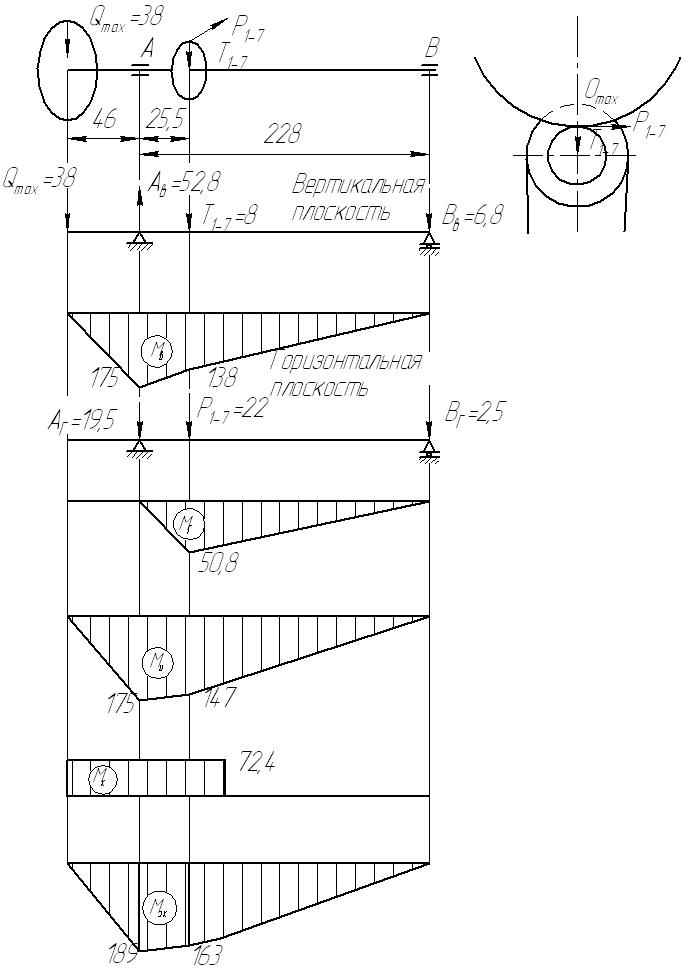
Просмотреть ближе
Рисунок
7.34 - Расчетная схема I
вала при включении передачи z1—
z7
В горизонтальной плоскости:


Проверка:

Результирующий изгибающий момент

Значения Mиг
и Mив берём по эпюрам изгибающих
моментов.
Суммарные реакции опор:


Вал скручивается моментом
только на участке левее средней плоскости ведомых дисков фрикционной
муфты сцепления при включении зубчатого венца z1,
что отражено на эпюре крутящих моментов.
Эквивалентные моменты:


Определим диаметр вала

Для упрощения расчетов принимаем допускаемое
напряжение
,
тогда

Диаметры смежных ступеней вала и их осевые
размеры должны обеспечивать беспрепятственное прохождение деталей на место
посадки, с тем чтобы исключалось повреждение посадочных поверхностей и в связи с
этим нарушение характера посадки. Однако отношение диаметров смежных ступеней
вала должно быть возможно меньшим, но обеспечивать необходимые размеры упорных
буртов для подшипников, муфт, зубчатых колес и т. д. Следует иметь в виду, что с
увеличением отношения диаметров сменных ступеней вала усталостная прочность
вала понижается в связи с ростом концентрации напряжений в переходном сечении.
В данном случае принимаем для закрепления
ведомого шкива клиноременной передачи на I валу
и передачи крутящего момента призматическую шпонку. Передача крутящего момента
на ведущие диски фрикционной муфты осуществляется с помощью шлицев (рисунок 7.33).
Подбор и проверка прочности шлицевого соединения.
Принимаем соединение средней серии с
центрированием по наружному диаметру, число зубьев z
= 6, d = 21 мм, f = r
= 0,2 мм. Обозначение по ГОСТ 1139—80 D-6×21×25
(рисунок
7.33). Проверка прочности на смятие

Подбор подшипников качения.
Для определения динамической грузоподъемности
принимаем следующие условия: нагрузка только радиальная, вращается внутреннее
кольцо подшипника, рабочая температура подшипника не превышает 100
°С,
желательная долговечность Lh = 10
000 ч, диаметр шейки вала d = 17 мм.
Требуемая динамическая грузоподъемность
определяется для наиболее нагруженного подшипника в опоре А.

Принимаем: коэффициент динамичности kб,
= 1,1 (таблица
3.63), кинематический коэффициент kк
=1, температурный коэффициент kТ =1, желаемую
долговечность Lh = 10 000 ч.
По ГОСТ 8338—75 принимаем радиальный
шарикоподшипник № 203 легкой серии, имеющий С =752 кгс. Монтажные
размеры подшипника d =17 см, D =40 мм,
В = 12 мм, радиус фаски внутреннего кольца r
=1,5 мм.
С целью унификации подшипниковых узлов для опоры
В (менее нагруженной) принимаем тот же подшипник, как и для опоры А.
Подбор муфты.
Для переключения передач z1—z7
и z2—z3 принята дисковая фрикционная муфта. Выбор ее
обусловлен тем, что дисковые фрикционные муфты допускают частые включения и
выключения, предохраняют детали передач от поломок при перегрузках,
обеспечивают плавное безударное включение и позволяют производить переключение
передач без остановки двигателя. Так как фрикционная муфта работает внутри
коробки подач, то диски будут смазываться, поэтому первые диски выполняются из
стали и текстолита.
Размеры муфты приняты по таблице (Приложение 10). Номер муфты 1.
В расчетно-пояснительную записку вносим лишь те
конструктивные элементы и их размеры, которые необходимы для выполнения
проверочных расчетов муфты.
Из указанной нормали выписываем размеры.
Наружный диаметр кольцевой поверхности трения
R =32,5 мм.
Внутренний диаметр кольцевой поверхности трения
r = 17,5 мм.
Число шлицев на валу z1
= 6. Число пазов в корпусе z2 = 3.
Высота площади смятия, которую мы принимаем
равной высоте выступов дисков:
ведущих h1
= 0,5 см; ведомых h2=0,23 см.
Ширина площадки смятия, равная толщине дисков:
ведущих S1 = 0,2 см; ведомых
S2=0,4 см.
Средний диаметр шлицев втулки dcp=2,32
см. Средний диаметр пазов корпуса Dcp =7 см. Передаваемый
крутящий момент
.
Расчет фрикционных муфт производится на
прочность сцепления и ограничение давления на рабочих поверхностях.
Расчетный момент определяется по уравнению Мр
= βМк , где β — коэффициент запаса сцепления. Принимаем β =
1,25; Мк —номинальный крутящий момент, который может передать
дисковая муфта, определяется по уравнению:
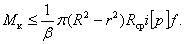
Отсюда число поверхностей трения
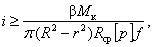
где R и r
— наружный и внутренний радиусы кольцевой поверхности трения;
—
средний радиус поверхности трения:

f — коэффициент трения при трении стали
по текстолиту f=0,15 (таблица 3.68);
[р] —
допускаемое удельное давление,

[ро] = 6 (таблица 3.68); k1=1 (таблица 3.69); k2=l
(таблица 3.70); k3=0,95 (таблица 3.70) (при 120 включениях в час).

Принимаем i = 2.
Число ведущих дисков

Число ведомых дисков

При разомкнутой муфте зазор между ведущими и
ведомыми дисками принимаем равным 0,8—1,5 мм.
Ход поводковой втулки X
= 12 мм.
Для предотвращения смятия вала и корпуса и
образования канавок следует проверить напряжения смятия по уравнениям:
на валу
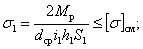
в корпусе
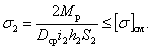
Принимаем
z1
и z2 — соответственно число шлицев (вал) и
пазов (корпус), dср и Dср
— средний диаметр соответственно шлицев вала и пазов корпуса.


Усилие для включения дисковой муфты, приведенное
к оси муфты, определяется по уравнению:
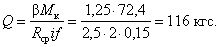
Ведомые части муфты, соединенные с зубчатыми
венцами z1 и z2, должны
вращаться на валу свободно. Поэтому установим их на валу на игольчатых
подшипниках. Требуемый коэффициент работоспособности определим по наиболее
нагруженной опоре под шестерней z2

Для определения динамической грузоподъемности
принимаем следующие условия: нагрузка только радиальная, подшипник игольчатый
без внутренней обоймы, вращается внутреннее кольцо подшипника (вал), рабочая
температура подшипника не превышает 125 °С, желательная долговечность Lh=10
000 ч, диаметр шейки вала d ' = 20 мм.

Принимаем: коэффициент динамичности kб
= 1,1 (таблица 3.63), кинематический коэффициент kк
=1, температурный коэффициент kТ =1.
По ГОСТ 4060—78 принимаем игольчатый подшипник с
одним наружным штампованным корпусом № 942/20 нормальной серии. Монтажные
размеры подшипника — по ГОСТ 4060—78 d = 20
мм, D = 26 мм, B
= 20 мм, радиус фаски наружного кольца R = 1,2
мм.
С целью унификации подшипниковых узлов для
второй части муфты принимаем тот же подшипник.
Подбор шпонки и проверка прочности шпоночного
соединения.
Для закрепления шкива клиноременной передачи на
валу принимаем призматическую шпонку исполнения А, размеры
сечений шпонки и паза по ГОСТ 29175—91.
По диаметру вала d
=15 мм принимаем шпонку шириной b = 5 мм,
высотой h = 3 мм, t1
= 1,8 мм, t2 = 1,4 мм (рисунок
7.11 из 1-го примера).
Определим длину шпонки из условия прочности на
смятие:
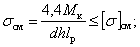
Материал шпонки — сталь 45 нормализованная.
Принимаем допускаемое напряжение
.
Рабочая длина шпонки
.
Полная длина шпонки
l = lp + b
= 7,08+5 = 12,08 мм
Принимаем по ГОСТ 29175—91
l=14 мм.
Условное обозначение: шпонка А 5×3×14 ГОСТ
29175—91.
Так как вал вращается в шарикоподшипниках с
внутренним диаметром 17 мм, то смежная ступень — шейка вала, на которой
закреплен подшипник, сопрягается с первой ступенью галтелью радиусом
R = 1 мм (см. рисунок 7.35). Для беспрепятственного
прохождения на посадочное место игольчатых подшипников диаметр шейки вала под
подшипники примем равным 20 мм. Так как в заплечик этой ступени упирается
подшипник, а высота заплечика мала, поставим упорную втулку (см. рисунок 7.33). Для
беспрепятственного прохождения дисков муфты сцепления на шлицевой участок вала
последний выполним диаметром d = 21мм.
Выбор посадок, квалитетов и шероховатости
поверхностей I вала.
По данным
Приложений 14 и
15 назначаем посадку
L0/k6
для внутренних колец подшипников.
По данным
Приложения 20 назначаем посадку для
наружных колец подшипников в корпус — H7/l0.
По
Приложению 18 назначаем
шероховатость поверхности: Ra 1,25 для
подшипниковых шеек, Ra 2,5 для торцов заплечиков вала, Ra 0,63 для шеек, на
которые будут установлены игольчатые подшипники качения. Для шкива
принимаем посадку
.
По Приложению 18
определяем шероховатости: Ra 1,25 на посадочную поверхность для шкива, Ra
0,63 для втулки на шейке вала под уплотнение.
После определения радиальных и осевых размеров
вала, назначения квалитетов и шероховатости поверхностей и посадок
вычерчиваем конструкцию вала (см. рисунок 7.35) с указанием данных, необходимых для
расчета вала на выносливость.
Расчет I вала на выносливость.
Определим коэффициент запаса усталостной
прочности для двух предположительно опасных сечений: А—А и Б— Б.
На расчетной схеме (рисунок. 7.35) представлена конструкция вала с указанием
предположительно опасных сечений и эпюры суммарных изгибающих и крутящих
моментов.
Сечение А—А.
Концентрация напряжений вызывается шпоночным
пазом.
Коэффициент запаса усталостной прочности на
кручение

где
τ-1
= 2400 кг/см2 (таблица 3.57);
ετ
= 0,89 (таблица 3.58);
β = 1,0 (таблица
3.59); kτ
= 2,05 (приложение 8);
ψτ =
0,05 (таблица 3.57).

Просмотреть ближе
Рисунок
7.35 - К расчету I
вала на выносливость
Так как в нашем случае вал подвергается частому
реверсированию, то принимаем, что напряжения кручения изменяются по
симметричному циклу. Тогда
τm
= 0

Момент сопротивления кручению поперечного
сечения вала с учетом ослабления шпоночным пазом:


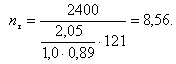
Сечение Б—Б.
Для этого сечения (концентратор
напряжения № 5, (рисунок 3.50) отношение
,
отношение
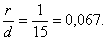
Коэффициент запаса усталостной прочности:
а) по изгибу
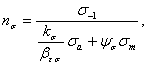
где
σ-1=4100
кг/см2 (таблица 3.57);
kσ
= 1,78 (приложение 4);
β = 1,0 (таблица 3.59);
εσ =
0,83 (табл. 3.58); ψσ=
0,1 (таблица 3.57).
При симметричном цикле напряжений изгиба
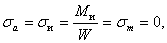

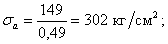
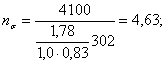
б) по кручению:
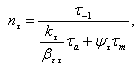
где
ετ = 0,89 (таблица 3.58); kτ
= 1,5 (Приложение 5);
β = 1,0 (таблица 3.59).
При симметричном цикле напряжений кручения:


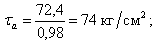
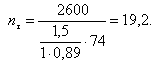
Результирующий коэффициент запаса не
вычисляется, поскольку очевидно, что получится значительно больше допустимого [n]=1,5—2,5.
7.2.3.2
Расчет II вала
Так как возможны различные комбинации включения
передач, то путем анализа установим такую из них, при которой нагрузки на валы
оказываются самыми неблагоприятными, вызывающими наибольшие эквивалентные
моменты.
Из рассмотрения компоновочной схемы (рисунок 7.32)
видно, что возможны 6 комбинаций включения передач: a) z1—z7;
z2—z6; б) z1—z7,
z5—z9; в) z1—z7,
z4—z10; г) z2—z3,
z6—z8; д) z2—z3,
z5—z9; ж) z2—z3,
z4—z10. Наиболее нагруженной
является пара z5—z9, так как делительный диаметр колеса
наименьший и расстояние между плоскостями действия сил наибольшее. Из двух
других зацеплений z4—z10 и z6—z8, у
которых расстояния между плоскостями действия сил примерно одинаковы, наибольшее
распорное и окружное усилие будет в зацеплении z4—z10, так
как делительный диаметр колеса z4 меньше, чем колеса z6.

Просмотреть ближе
Рисунок 7.36 - Расчетная схема
II
вала при включении передачz2—z3,
z5—
z9
Таким образом, комбинации а, б, в, г
исключаются, так как дают более легкие случаи нагружения вала. Для того чтобы
выяснить, какая из комбинаций д или ж дает более тяжелый случай
нагружения, составим две расчетные схемы (рисунки 7.36, 7.37).
Комбинация д (рисунок 7.36).
Расстояние между плоскостями действия сил
принимаем по компоновочной схеме (рисунок 7.32). Крутящий момент, передаваемый
валом, Мк = 148 кгс·см (см.
п. 7.1.2). Определим усилия в зацеплении.
Окружные:

Распорные:



Определим опорные реакции. В вертикальной
плоскости (рисунок 7.36)


Проверка:

В горизонтальной плоскости:


Проверка:
Результирующие изгибающие моменты:


Суммарные реакции опор:


Эквивалентные моменты:


Комбинация ж (рисунок 7.37).
Так как расчеты реакций опор и различных
моментов производятся так же, как и в предыдущем случае, то записываем лишь
конечные результаты вычислений, опуская промежуточные операции. Расчетная схема
вала показана на рисунке 7.37.
Усилия в зацеплении.
Окружные:

Распорные:

Реакция опор.
В вертикальной плоскости: АВ
= 9,7 кг, ВВ = 28,4 кг.
В горизонтальной плоскости: АГ
= 1,2 кг, ВГ = 16,5 кг.

Просмотреть ближе
Рисунок 7.37 - Расчетная схема
II вала при включении передач
z2—z3,
z4—z10
Результирующие изгибающие моменты:


Суммарные реакции опор:


Эквивалентные моменты:


Из рассмотрения эпюр эквивалентных моментов
(рисунок 7.36) следует, что за расчетный случай нужно принять тот, при котором в
зацеплении находятся колеса z2—z3, z5—z9, так как при этом вал нагружен
наибольшим эквивалентным моментом.
Определим диаметр вала, принимая допускаемое
напряжение


Принимаем диаметр вала d =18 мм.
Подбор подшипников качения.
Диаметры шеек II
вала под подшипники были определены исходя из условия прочности вала на
кручение и приняты d = 17 мм.
Требуемая динамическая грузоподъемность
определяется по большей реакции в опоре В, по условиям, принятым для
подшипников I вала, поскольку эти условия
одинаковы:

По ГОСТ 8338—75 принимаем шарикоподшипник № 203
легкой серии, имеющий Стр = 732 кгс. Монтажные размеры
подшипника d =17 мм, D = 40 мм, В
= 12 мм, r =1,5 мм. С целью унификации
подшипниковых узлов для опоры А (менее нагруженной) принимаем тот же
подшипник, как и для опоры В.
Подбор шпонок и проверка прочности шпоночных
соединений.
Передача крутящих моментов валом осуществляется
при помощи призматических шпонок. Принимаем призматические шпонки исполнения A,
размеры сечений шпонки и пазов по ГОСТ 29175—91.
По диаметру вала d =18 мм принимаем
шпонку шириной b =5 мм, высотой
h =3 мм, t 1 =1,8 мм,
t2 =1,4 мм (рисунок 7.11).
Определим длину шпонки из условия прочности на
смятие:
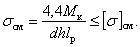
Материал шпонки — сталь 45
нормализованная. Принимаем допускаемое напряжение

Рабочая длина шпонки:
мм.
Полная длина шпонки
l
= lp + b =
12,06 +5 = 17,06 мм.
Принимаем по ГОСТ 29175—91
l = 18 мм.
Условное обозначение: шпонка А 5х3х18 ГОСТ 29175—91.
С целью уменьшения перекосов при монтаже и
эксплуатации каждое зубчатое колесо соединяется с валом при помощи отдельной
шпонки (рисунок 7.33).
Выбор посадок, квалитетов и шероховатости
поверхностей II вала.
По
Приложениям 14 и
15 назначаем посадку L0/k6
для внутренних колец подшипника, а по
Приложению 16 определяем
шероховатость поверхности: Ra 1,25 для подшипниковых шеек и
Ra 2,5 для торцов заплечиков вала.
По данным
Приложения 17 назначаем для
зубчатых колес посадку
, а по
Приложению 18 назначаем шероховатости
Ra 0,63 — на посадочные поверхности для зубчатых колес.
Шероховатость свободных поверхностей принимаем Rz 40.
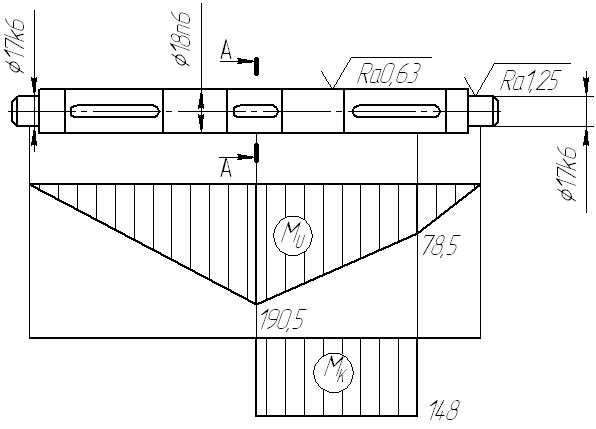
Просмотреть ближе
Рисунок 7.38 - К расчету
II
вала на выносливость
После определения радиальных и осевых размеров
вала, назначения классов точности и шероховатости поверхностей и посадок
вычерчиваем конструкцию вала (рисунок 7.38) с указанием данных, необходимых для
расчета вала на выносливость.
Расчет II вала на выносливость.
Рассмотрим случай включения передач
z2—z3
и z5—z9, при котором вал
нагружен наибольшим результирующим изгибающим моментом
и в то же время наибольшим крутящим моментом

Определим результирующий коэффициент запаса
усталостной прочности n в сечении А—А
(рисунок 7.38).
Концентрация напряжений обусловлена шпоночным
пазом. (Концентратор напряжения № 15,
рисунок 3.50.)
Коэффициенты запаса по усталостной прочности:
а) по изгибу:
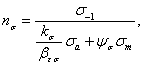
где
σ-1=2500 кг/см2
(таблица 3.57);
kσ
= 1 (табл. 3.60); β
= 1 (таблица 3.59); εσ
= 0,83 (таблица 3.58).
При симметричном цикле напряжений изгиба:
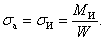
Момент сопротивления изгибу с учетом
ослабления сечения шпоночным пазом:


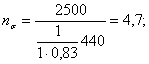
б) по кручению: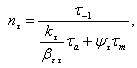
где
τ-1
= 1500 кг/см2 (таблица 3.57); kτ
=1,37 (таблица 3.60); β
= 1 (таблица 3.59); ετ
= 0,89 (таблица 3.58).
При симметричном цикле напряжений
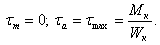
Момент сопротивления кручению поперечного
сечения с учетом ослабления сечения шпоночным пазом:


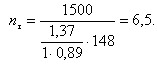
Результирующий коэффициент запаса по усталостной
прочности:

7.2.3.3 Расчет III вала
Вал передает 6 крутящих моментов. Из
рассмотрения компоновочной схемы (рисунок 7.32) видно, что одним из наиболее
тяжелых случаев будет случай включения передачи z2—z3 и z5—z9 (комбинация д), так как расстояние между плоскостями
действия сил будет наибольшим. Из двух других комбинаций: z6—z8
и z2—z3 (комбинация г)
и z2—z3 и z4—z10 (комбинация
ж), у которых расстояния между плоскостями действия сил примерно одинаковы,
наиболее тяжелым будет случай при комбинации г, так как делительный
диаметр колеса z8 меньше, чем колеса z10. Комбинации z1—z7, z5—z9; z1—z7
и z4—z10,
z1—z7, z6—z8 исключаются, так как зацепление z2—z3 передает больший крутящий момент при примерно одинаковом
расстоянии между плоскостями действия сил.
Для того чтобы выяснить, какая из комбинаций
д или г дает более тяжелый случай нагружения, составим две расчетные
схемы (рисунки 7.39, 7.40).
Комбинация а (рисунок 7.39).
Расстояние между плоскостями действия сил
принимаем по компоновочной схеме (см. рисунок 7.32).
Усилия в зацеплении.
Окружное:
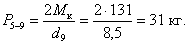
Распорное:

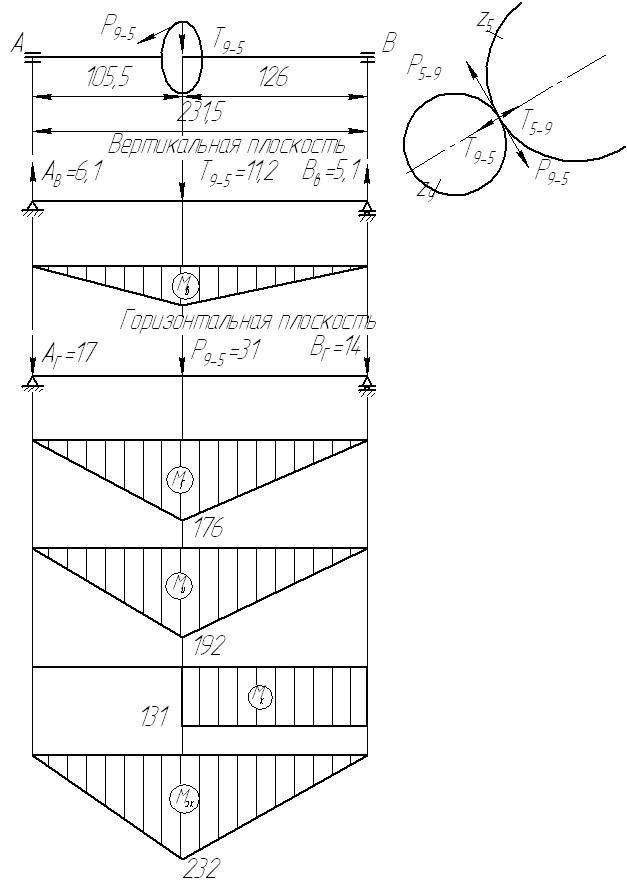
Просмотреть ближе
Рисунок 7.39 - Расчетная схема III вала при включении
передач z5—z9
и z2—z3
Определяем опорные реакции. В вертикальной
плоскости:


Проверка:

В горизонтальной плоскости:


Проверка:

Результирующий изгибающий момент:

Эквивалентный момент:


Просмотреть ближе
Рисунок 7.40 - Расчетная
схема III вала при включении передачи z6—z8 и
z2—z3
Суммарные реакции опор:


Комбинация г (рисунок 7.40).
Расстояния между плоскостями действия сил
принимаем также по компоновочной схеме (рисунок 7.32).
Усилия в зацеплении.
Окружное:

Распорное:

Определяем опорные реакции в вертикальной
плоскости:


Проверка:

В горизонтальной плоскости:


Проверка:

Суммарные реакции опор:


Результирующий изгибающий момент:

Эквивалентный момент:

Из рассмотрения эпюр эквивалентных моментов
следует, что за расчетный случай нужно принять тот, при котором в зацеплении
находятся колеса z2—z3 и
z5—z9,
так как при этом вал нагружен наибольшим эквивалентным моментом.
Определим диаметр вала, принимая допускаемое
напряжение


Принимаем d = 16 мм.
Подбор подшипников качения.
Диаметры шеек III вала под подшипники
были определены, исходя из условия прочности вала на кручение, и приняты d
= 15 мм.
Требуемая динамическая грузоподъемность
определяется по наибольшей реакции в опоре А по условиям, принятым для
подшипников I и II валов.

По ГОСТ 8338—75 принимаем шарикоподшипник № 202
легкой серии, имеющий С = 597 кгс. Монтажные размеры подшипника d
= 15 мм, D = 35 мм, b
= 11 мм, r = 1 мм.
По конструктивным соображениям (рисунок 7.33) для
опоры B по ГОСТ 8338—75 принимаем
шарикоподшипник № 204 легкой серии, имеющий С = 1000 кгс. Монтажные
размеры подшипника: d = 20 мм, D = 47 мм,
b = 14 мм, r =1,5 мм.
Передача крутящих моментов валом осуществляется
посредством прямобочного зубчатого (шлицевого) соединения, причем для
обеспечения осевого перемещения блока зубчатых колес вал принят постоянного
сечения по всей длине между подшипниковыми шейками (рисунок 7.41).
Принимаем соединение средней серии с
центрированием по наружному диаметру.
Из ГОСТ 1139—80 выписываем размеры шлицевого
соединения
d = 16 мм, D = 20 мм, f = 0,3 мм,
r = 0,2 мм, z = 6,
b = 4 мм.
Свободный выход фрезы при нарезании зубьев
обеспечен, поскольку
d = 16 мм больше диаметра подшипниковой шейки.
Высота заплечика для упора внутреннего кольца
подшипника:
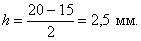
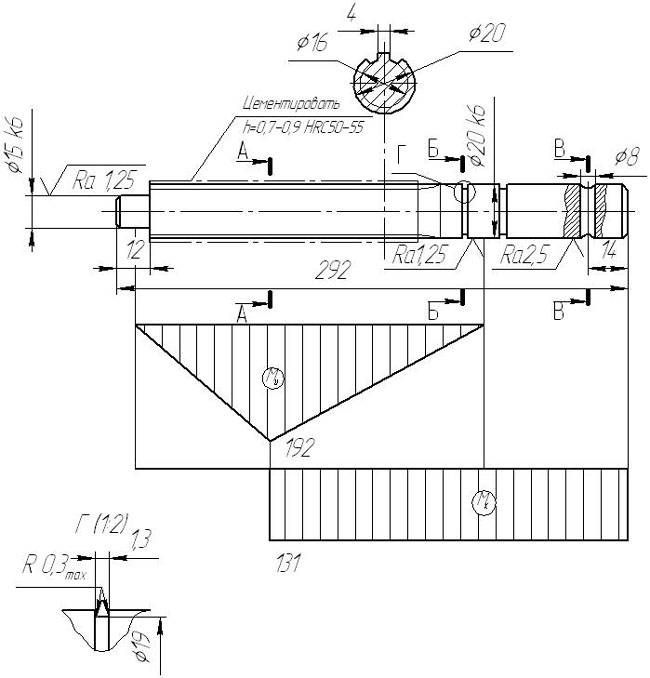
Просмотреть ближе
Рисунок 7.41 - К расчету
III вала на выносливость
Проверка прочности шлицевого соединения.
Проверка прочности на смятие производится по
уравнению:
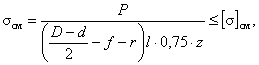
где l = 30 мм —
длина ступицы блока.
По
таблице 3.61 принимаем



Прочность соединения обеспечена, так как

Выбор посадок, кавлитетов и шероховатости
поверхностей III вала.
По
Приложениям 14 и
15 назначаем посадку L5/k5
для внутренних колец подшипника, а по
Приложению 16 определяем
шероховатости: Ra 1,25 для подшипниковых шеек и
Ra 2,5 для торцов заплечиков, приняв предварительно класс точности
подшипника 5. Назначаем посадку шлицевого соединения D-
6×16×20H7/f7х4F8/f8 . Контактные поверхности шлицев обрабатываются: по центрирующей
поверхности — Ra 0,65, по боковым сторонам —
Ra 2,5.
Расчет муфты.
Для соединения III
вала с IV (ходовым) (рисунок 7.33) принимаем втулочную муфту с
коническими штифтами (рисунок 7.42). Размеры муфты принимаем по нормали
машиностроения [37]. Основные размеры муфты следующие:

Просмотреть ближе
Рисунок 7.42 - К расчету
втулочной муфты
d = 20 мм,
D = 35 мм, L = 60 мм, d1
= 6 мм, l = 15 мм. Штифты конические: штифт 6×35 ГОСТ
3129—70. Материал втулки и штифтов — сталь 45.
Штифты проверяем на срез по двум плоскостям:
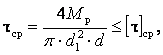
где
— расчетный момент,
кгс·см

— коэффициент режима работы.



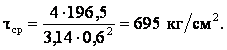
Прочность соединения обеспечена.
Расчет III вала на выносливость.
Определим коэффициент запаса усталостной
прочности для трех предположительно опасных сечений А — А, Б — Б и В — В
(рисунок 7.41) в том случае, когда включены передачи z2—z3 и z5—z9 (рисунок
7.39) и передается наибольший эквивалентный момент.
Сечение А — А (рисунок 7.41).
Из расчетной схемы видно, что вал в этом сечении
нагружен наибольшим изгибающим моментом
и крутящим моментом
Концентрация напряжений вызывается шлицами (концентратор №
13,
рисунок 3.50).
Коэффициенты запаса усталостной прочности:
а) по изгибу:
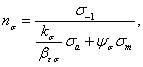
где σ-1 = 3000 кг/см2
(таблица 3.57);
kσ = 1 (концентратор № 13,
рисунок 3.50);
β = 1,5 (таблица 3.59);
εσ = 0,83 (таблица 3.58);
ψσ= 0,05 (таблица 3.57);
ψτ =
0 (таблица 3.57).


б) по кручению:
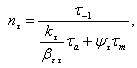
где
τ-1
= 1600 кг/см2 (таблица 3.57);
kτ
=2,45 (таблица 3.60,
концентратор № 13);
β = 1,8
(таблица 3.59);
ετ
= 0,83 (таблица 3.58);
ψτ = 0 (таблица 3.57).

где

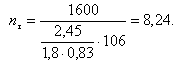
Результирующий коэффициент запаса не
вычисляем, поскольку очевидно, что он получится больше допустимого

Сечение Б—Б (рисунок 7.41).
Концентрация напряжения вызывается галтелью
(концентратор № 9, Приложение 7)
 Поскольку в данном сечении действует сравнительно небольшой
изгибающий момент
поэтому расчет производим только по крутящему моменту.
Коэффициент запаса усталостной прочности по
кручению:

где
τ-1
= 1600 кг/см2 (таблица 3.57);
kτ
= 1,66 (таблица 3.60);
β
= 0,85 (таблица 3.59);
ετ
= 0,84 (таблица 3.58);
d = 19 мм.


Сечение В—В (рисунок 7.41).
В данном сечении вал нагружен только крутящим
моментом. Концентрация напряжения вызывается отверстием диаметром d1
= 6 мм (концентратор № 19,
рисунок 3.50).
Коэффициент запаса усталостной прочности по
кручению:

где
τ-1
= 1600 кг/см2 (таблица 3.57);
kτ
= 1,75 (таблица 3.60);
β
= 0,85 (таблица 3.59);
ετ
= 0,84 (таблица 3.58);
τm = 0;


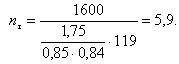
Во всех сечениях коэффициент запаса усталостной
прочности превышает допустимое значение

7.2.3.4 Расчет ходового вала
Ранее диаметр вала был рассчитан, исходя из
условия прочности на кручение, поскольку изгибных нагрузок этот вал не
передает (рисунок 7.33) и его диаметр принят d = 17 мм.
В связи с тем, что ходовой вал имеет
значительную длину, то жесткость его может оказаться недостаточной, т. е.
действительный угол закручивания превысит допускаемое значение. Поэтому
определим диаметр вала исходя из условия ограничения угла закручивания,
допустимое значение которого примем
на метр длины вала.

Принимаем диаметр вала d
= 27 мм.
Передача крутящего момента валом осуществляется
с помощью призматической шпонки.
По диаметру вала d = 27 мм по ГОСТ
8790—79 принимаем призматическую шпонку исполнения 1. Размеры сечения шпонки и
пазов по ГОСТ 8790—79: b = 8 мм,
h = 7 мм, t1 = 4,0
мм, t2 = 3,3 мм. В связи с тем, что
контактные поверхности шпонки и паза в ходовом валике подвержены износу,
допускаемое напряжение смятия принимаем пониженным

Определим рабочую длину шпонки

По ГОСТ 8790—79 принимаем
lр = 90 мм. Шпонка крепится к зубчатому колесу
z1 двумя винтами М3х8 (рисунок 7.33).
Расчет ходового вала на выносливость не
производим, т. к. диаметр вала по условию жесткости значительно больше, чем по
условию прочности на кручение.
7.2.3.5 Расчет VI вала
Шестой вал — шестерня находится в постоянном
зацеплении с рейкой и передает шесть крутящих моментов, максимальным из которых
является
. Расчетная схема шестого вала приведена на рисунке
7.43. Расстояние между плоскостями действия сил принимаем по компоновочной
схеме (рисунок 7.29).
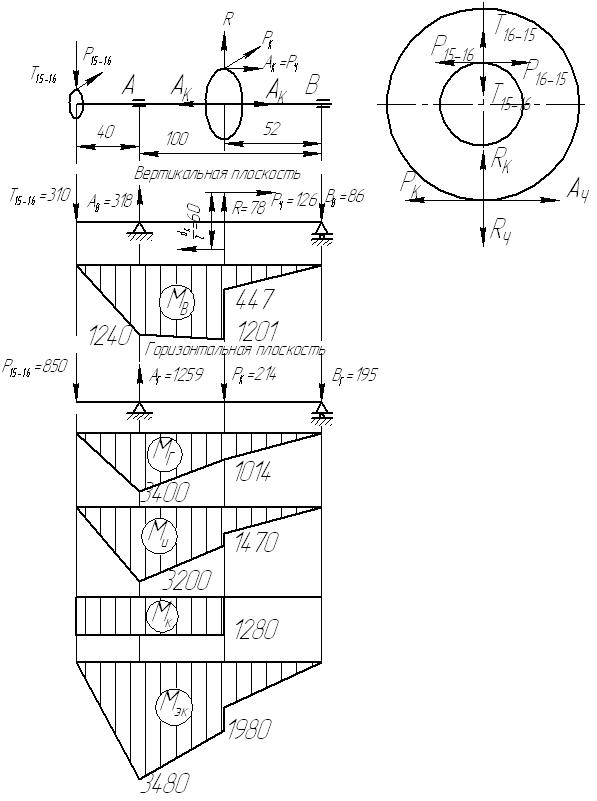
Просмотреть ближе
Рисунок 7.43 - Расчетная схема
VI вала
Усилия в зацеплении:
а) в червячной передаче (рисунок 7.43)

б) в реечной передаче
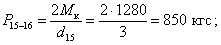

Реакции опоры:
а) в вертикальной плоскости:


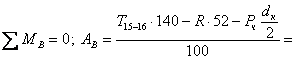

Проверка:

б) в горизонтальной плоскости:


Проверка:

Результирующие изгибающие моменты:


Суммарные реакции опор:


Эквивалентные моменты:


Определим диаметры ступеней вала, приняв
допускаемое напряжение



Подбор подшипников вала червячного колеса.
Исходные данные: радиальные нагрузки опор А = 1260 кгс; В = 206
кгс, осевая нагрузка Рч = 126 кгс, передача работает в
масляной ванне (с легкими толчками) при температуре подшипника t
≤100 °C. Желаемый срок службы подшипника Lh
=5000 ч.
Для опоры А, воспринимающей большую
нагрузку, предварительно принимаем по диаметру цапфы вала
d = 35 мм роликоподшипник конический легкой серии
7207А (ГОСТ 27365—87). Начальный угол контакта принят α = 14°02'10",
поскольку радиальные нагрузки опор больше осевой нагрузки.
По методике, примененной при выборе подшипников
червячного вала, определена динамическая грузоподъемность для подшипника в
опоре А Стр = 2980 кгс. Таким образом, Стр
< С = 3520 кгс, а поэтому сохраняем выбранный подшипник 7207А.
Монтажные размеры подшипника, мм: d =
35, D = 72, В = 17,
Tmax = 18,25;
r = 2.
Для опоры В принимаем подшипник
7206А, имеющий С = 2230 кгс. Монтажные размеры подшипника, мм: d
= 30, D = 62, В = 16;
Tmax = 17,25; r = 2. В данном
случае применение подшипников разных размеров оказывается необходимым для
облегчения монтажа узла вала червячного колеса (рисунок 7.33).
Подбор шпонки и проверка прочности шпоночного
соединения.
Для закрепления червячного колеса на валу
принимаем шпоночный паз и призматическую шпонку исполнения А по ГОСТ 29175—91.
По диаметру вала d
= 31 мм принимаем шпонку шириной b = 10 мм,
высотой h = 6 мм, t1 = 3,5 мм, t2
= 2,8 мм (рисунок 7.11).
Определим длину шпонки из условия прочности на
смятие:

Материал шпонки — сталь 45 нормализованная.
Принимаем допускаемое напряжение
.
Рабочая длина шпонки:
мм.
Полная длина шпонки:
l
= lp + b = 30
+ 10 = 40 мм (по
ГОСТ 29175-91 l = 40 мм).
Условное обозначение: шпонка А
10×6×40 ГОСТ 29175—91.
Выбор посадок, квалитетов и шероховатости
поверхностей VI вала.
По данным
Приложений 14 и
15 назначаем посадку L5/k6
для внутренних колец подшипников, а по Приложению 16 определяем шероховатости:
Ra 1,25 для подшипниковых шеек. По
Приложению 17 назначаем посадку
червячного колеса на валу . По
Приложению 18 назначаем шероховатость
Ra 0,63 на посадочную поверхность червячного
колеса.
Расчет VI вала на выносливость.
Определим коэффициент запаса усталостной
прочности для трех предположительно опасных сечений А—А, Б—Б и
В—В (рисунок 7.44).
Сечение А—А.
Из расчетной схемы видно, что вал в этом сечении
ослаблен выходом режущего инструмента при нарезании зубьев реечной шестерни
(концентратор № 12,
рисунок 3.50).
Коэффициент запаса усталостной прочности:

Просмотреть ближе
Рисунок 7.44 - К расчету VI
вала на выносливость
а) по изгибу
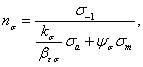
где σ-1 = 4100 кг/см2
(таблица 3.57);
kσ = 1,69 (таблица 3.60);
β = 0,85 (таблица 3.59);
εσ = 0,77 (таблица 3.58);
ψσ=
0,1 (таблица 3.57).


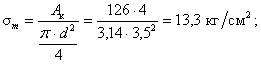

б) по кручению:

где τ-1 = 2400 кг/см2
(таблица 3.57);
kτ = 2,05 (таблица 3.60);
β = 0,85 (таблица 3.59);
ετ = 0,81 (таблица 3.58);
ψτ = 0,05 (таблица 3.57).

τm = 0, так как изменение напряжений происходит по симметричному
циклу.
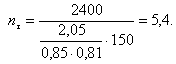
Результирующий коэффициент запаса усталостной прочности:
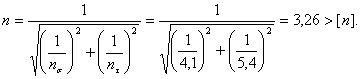
Сечение Б—Б.
Концентрация напряжения вызывается шпоночным
пазом.
Коэффициент запаса усталостной прочности:
а) по изгибу:

где kσ = 1 (таблица 3.60);
β = 1
(таблица 3.59);
εσ = 0,83 (таблица 3.58);
ψσ=
0,1 (таблица 3.57).
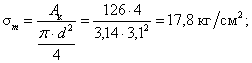
б) по кручению:
где kτ = 2,05 (таблица 3.60);
β
= 1 (таблица 3.59);
ετ = 0,89 (таблица 3.58);
ψτ = 0,05
(таблица 3.57).
При симметричном цикле напряжений: τm
= 0.

Результирующий коэффициент запаса усталостной
прочности:
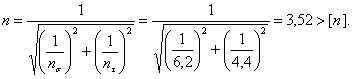
Сечение В—В (рисунок 7.44).
Концентрация напряжений вызывается
концентратором № 10 (рисунок 3.51);
r = 0,5 мм;
h = 1 мм; d = 28 мм;

Коэффициент запаса усталостной прочности:
а) по изгибу

где kσ = 2,01 (таблица 3.60);
β
= 1 (таблица 3.59);
εσ = 0,83 (таблица 3.58);
ψσ= 0,1
(таблица 3.57);


Во всех сечениях коэффициент запаса усталостной
прочности превышает допустимое значение

Расчет механизма переключения.
Изменение подач осуществляется введением в
зацепление различных пар зубчатых колес и включениями фрикционной муфты (рисунки
7.33 и 7.45). Для перемещения блока зубчатых колес применен реечный механизм и
вилка.

Просмотреть ближе
Рисунок 7.45 - Расчетная
схема привода управления
Полный ход блока составляет S = 64 мм.
Ход рейки вправо (если смотреть со стороны рукояток управления) составляет S1
= 30 мм, ход влево S2 = 34 мм.
Определим длину рейки, обеспечивающую осевое
перемещение блока:

Принимаем число зубьев реечной шестерни
z =15, m = 2 мм,
число зубьев зубчатых колес z2 = 18 и
z3 = 48 при m
= 2 мм.
Расчет углов поворота рукоятки управления
показан на рисунке 7.45. Для перемещения блока влево от среднего положения
необходимо:
а) число оборотов промежуточного валика
I' (рисунок 7.45):

б) число оборотов рукоятки управления 1:
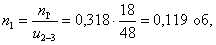
что соответствует повороту рукоятки
управления на угол φ1 = 43°. Для перемещения блока вправо от
среднего положения необходимо:
а) число оборотов промежуточного валика I':

б) число оборотов рукоятки управления 1:

что соответствует углу поворота рукоятки
управления на угол φ2 = 48°48'.
Полный угол поворота рукоятки управления'
φ'
= φ1 + φ2 = 43° + 48°48' = 91°48'.
Шестерня z3
изготовлена в виде сектора с углом φ = φ'
+ φ0, где φ0 — угол, необходимый для
обеспечения постоянного зацепления шестерни z2
с сектором z3.

Для управления фрикционной муфтой принимаем
наиболее широко распространенный механизм переключения — рычажный (рисунок 7.46).
Переключение производится непосредственно рычагом, сидящим на одной оси с
рукояткой управления. Недостатком этого механизма является то, что при повороте
рычага его конец описывает дугу и камень, находящийся в пазу, смещается
относительно последнего. При небольшой длине рычага и большом угле поворота
камень может чрезмерно отклониться от оси муфты, что приведет к нарушению
нормальной работы механизма. Но в данном случае ход поводковой втулки для
включения муфты небольшой (12 мм в одну сторону и столько же в другую).

Просмотреть ближе
Рисунок 7.46 - Привод управления
|