7.1.3 Расчет
валов
7.1.3.1 Выбор материала валов
Для правильного выбора материала валов и
термообработки их необходимо знать: тип подшипников, в которых вращается вал,
характер посадок деталей на валу (подвижные или с натягом), характер действующей
нагрузки.
Первый вал быстроходный, вращается в подшипниках
качения. Зубчатые колеса z1
и
z2
и полумуфта посажены на вал на шпонках по переходным посадкам. Наиболее
подходящим материалом для этих условий является сталь 35 нормализованная (таблице
3.56). Механические свойства этой стали принимаем по
таблице 3.57:
σв
= 5200 кг/см2; σ–1= 2600 кг/см2; σT
= 3100 кг/см2: τ–1
= 1300 кг/см2; ψσ = 0; ψτ
= 0.
Второй и третий валы имеют шлицы, по которым
перемещаются кулачковая полумуфта и блок зубчатых колес
z4—z5,
кроме того, третий вал имеет подшипниковые шейки, на которых вращаются зубчатые
колеса z7
и z8.
Валы вращаются в подшипниках качения. Для обеспечения достаточной
износостойкости трущихся поверхностей принимаем для указанных валов сталь 20Х.
Термообработка — цементация и закалка трущихся поверхностей до
HRC
58÷62. Механические свойства этой стали принимаем по
таблице 3.57.
σв
= 6500 кг/см2; σ–1= 4000 кг/см2; σT
= 3000 кг/см2: τ–1
= 1600 кг/см2; ψσ = 0,05;
ψτ = 0.
Для расчета валов и подбора подшипников необходимо
вычислить реакции опор и изгибающие моменты, действующие в различных сечениях
валов.
Эта задача может быть выполнена лишь в том случае,
когда будут известны расстояния между плоскостями действия нагрузок и опорами.
Для нахождения этих расстояний необходимо вычертить в
произвольном масштабе эскизную компоновку коробки скоростей в виде развертки по
осям и свертки (рисунок
7.7). При выполнении компоновочной схемы необходимо:

Просмотреть ближе
а — развертка; б — свертка
Рисунок 7.7 - Компоновочная схема коробки скоростей
1) обеспечить достаточные осевые перемещения зубчатых
колес, муфт, переключающих устройств;
2) исключить одновременное включение блоков зубчатых
колес с двумя смежными неподвижными колесами;
3) механизмы управления располагать так, чтобы
рукоятки управления находились в удобном положении. Нежелательно располагать
подшипники механизма управления в области масляной ванны корпуса коробки
скоростей или подач, с тем чтобы исключить подтеки масла и уплотнения на осях
механизма управления. Не рекомендуется располагать устройства для управления
механизмами на съемных крышках коробок скоростей или подач;
4) обеспечить доступную и быструю сборку и разборку,
легкую регулировку опор, зубчатых зацеплений. Кроме того, обеспечить хороший
доступ для осмотра деталей коробки и ремонта;
5) обеспечить самосмазываемость зубчатых зацеплений
и подшипников в тех случаях, когда это допускается окружной скоростью зубчатых
колес (см. п. 5.2);
6) конструкцию корпуса выполнять наиболее удобной,
простой и технологичной, обеспечивающей наибольшую простоту монтажа и демонтажа
деталей и узлов коробок;
7) возможно большее число центров валов располагать по
одним и тем же вертикалям и горизонталям, что обеспечит наибольшую простоту
настройки станков при обработке посадочных отверстий в корпусах;
8) наиболее быстроходные валы располагать возможно
ближе к основанию коробки, что будет способствовать увеличению устойчивости и
снижению интенсивности вибраций;
9) обеспечить наибольшую жесткость валов и опор, для
чего следует расстояния между зубчатыми колесами и другими деталями принимать
наименьшими из допустимых. Если предписанная для данных условий жесткость вала
не может быть выдержана, то следует предусмотреть установку третьей
промежуточной опоры;
10) достичь наибольшей компактности, удобной формы и
привлекательных внешних очертаний.
На основании указанных рекомендаций компоновочная
схема разрабатывается в следующем порядке.
1. Проводятся оси валов, причем межосевые расстояния,
полученные при расчете зубчатых передач, откладываются в произвольном масштабе.
2. Производится предварительное определение диаметров
валов.
Для составления расчетных схем необходимо знать
расстояния между плоскостями действия сил, которые зависят от осевых размеров
муфт, зубчатых колес, звездочек, подшипников и т. д., в свою очередь зависящих
от диаметра вала. Поэтому диаметры валов могут быть определены лишь
предварительно по условному расчету на кручение по уравнению:
.
Консольный участок
I
вала только скручивается, поэтому диаметр вала под полумуфту определим также по
приведенному уравнению:
.
Предварительно принимаем
dI’
= 22 мм по диаметру расточки в полумуфте (Приложение
12).
Для обеспечения свободного прохода полумуфты и
подшипников на посадочные места вал следует выполнять ступенчатым. Поэтому
диаметр шейки вала под подшипники увеличиваем до ближайшего большего
стандартного диаметра внутреннего кольца подшипника (см. ГОСТ 8338—75).
pI
= 25 мм.
Диаметр
II
вала:
.
Диаметр
III
вала:
.
Расчетные значения
dII
и
dIII
округляем до ближайших значений по указанному
стандарту на подшипники и принимаем эти значения за диаметры шеек валов под
подшипники.
Таким образом,
dII
=30 мм;
dIII
=40 мм.
В зависимости от этих диаметров внутренних колец
подшипников выписываются из таблиц стандарта диаметры наружных колец и ширины колец
В (размеры в мм):
dI
= 25, D
= 52, В = 15;
dII
=30, D
= 62, В = 16;
dIII=
40, D
= 80, В = 18.
При последующем основном расчете валов эти диаметры
могут быть изменены в большую или меньшую сторону.
3. Выбирается способ смазки подшипниковых узлов и
зубчатых зацеплений (см.
п. 5.1).
В данном случае подшипники должны смазываться
консистентной смазкой, закладываемой в подшипниковые камеры. Поэтому подшипники
закрываются со стороны внутренней полости корпуса мазеудерживающими кольцами.
Ширина кольца по валу b
= 10 мм. Расстояние между средней
плоскостью звездочки, в которой действует нагрузка на вал от цепного привода, и
средней плоскостью подшипника определяется в зависимости от конструкции
уплотняющих устройств, размеров сквозной крышки и конструкции ограждения для
цепной передачи.
4. Определяются в зависимости от диаметра вала и
конструктивных особенностей деталей передач длины ступиц зубчатых колес,
звездочек. В данном примере для сокращения осевых габаритов коробки применено
переключение блока колес с помощью охватывающей вилки. В таком случае ширина
блока складывается из ширины зубчатых венцов
z4
и z5
(таблице 7.6) и ширины проточки b = 7 мм (таблице 4.15) для выхода долбяка.
B=24+18+7=49
мм. Этот же размер принимаем за длину ступицы блока, так как рекомендуемая длина
последней lcт=
(0,2÷1,6)·30=36÷48 мм незначительно отличается от принятой ширины блока, равной
49 мм.
5. Предварительно подбираются размеры муфт,
смонтированных внутри коробки в зависимости от диаметра вала и передаваемой
нагрузки. В этом примере осевые размеры кулачковой муфты определяются в
зависимости от осевых размеров деталей, посаженных на
II
вал. Длина подвижной полумуфты укладывается в осевой размер, определяемый осевым
перемещением блока колес.
Обычно принимают зазор между торцами цилиндрических
зубчатых колес и внутренней стенкой корпуса равным толщине стенки корпуса,
причем толщина стенки принимается δ = 0,025 а + 5 мм (но не менее 10 мм), где
а — большее из межосевых расстояний в мм. В данном случае δ = 0,025·168,75+5
мм ≈ 10 мм.
Расстояние между торцами зубчатых колес не должно
превышать 4—6 мм, а расстояние между торцами зубчатых блоков и неподвижных колес
следует принимать 3—4 мм .
По найденным осевым и радиальным размерам деталей коробки скоростей, а также
монтажным размерам (расстояния между различными деталями) вычерчивается
развертка. Одновременно или попутно с этой операцией производится вычерчивание
свертки коробки, при этом необходимо руководствоваться ранее изложенными
рекомендациями. При последующем основном расчете валов чертеж свертки необходим
для вычерчивания расчетных схем валов. По свертке определяются направления
радиальных и окружных усилий, действующих в зубчатых зацеплениях, а также
направление сил, действующих на валы от ременных и цепных передач (рисунок
7.8,
7.12, 7.13, 7.18, 7.19).
Из рассмотрения схемы коробки (рисунок
7.7) следует, что
наибольшее расстояние между центрами подшипников и наибольшие габариты коробки в
осевом направлении определяются монтажными и осевыми размерами деталей,
посаженных на II
валу. Поэтому вычерчивание компоновочной схемы коробки скоростей следует
начинать с вычерчивания , компоновочной схемы узла
II
вала (рисунок
7.7).
Следует иметь в виду, что в результате предварительной
компоновки деталей на валах коробок скоростей и подач мы получаем необходимые
нам расстояния между плоскостями действия сил лишь ориентировочно, по той
причине, что размеры опор, муфт, зубчатых колес, регулировочных и крепежных
средств зависят и устанавливаются по диаметру вала. Последний может быть
определен более точно по эквивалентному моменту только после вычерчивания
развертки, необходимой для составления расчетных схем.
7.1.3.2 Основной расчет валов
Для каждого вала составляются расчетные схемы в
соответствии с нагрузками, действующими в зубчатых зацеплениях при различных
положениях колес и муфт, что дает возможность выявить наиболее тяжелый случай
нагружения вала.
При этом расчете вычерчивается схема нагружения вала с
изображением векторов сил, действующих на вал со стороны зубчатых, ременных,
цепных и других передач. В обозначениях сил, возникающих в зубчатых зацеплениях,
первый индекс обозначает номер колеса, на которое действует сила, второй — номер
колеса, со стороны которого действует сила (рисунок 7.8). На расчетных схемах вычерчиваются эпюры изгибающих, крутящих и
эквивалентных моментов. Для удобства построения эпюр изгибающих моментов следует
на схемах нагружения валов указывать активные силы и реакции опор в цифровом
виде. Затем с помощью логарифмической линейки или других счетных средств
непосредственно определять изгибающие моменты в сечениях под силами, не прибегая
к составлению уравнений моментов.
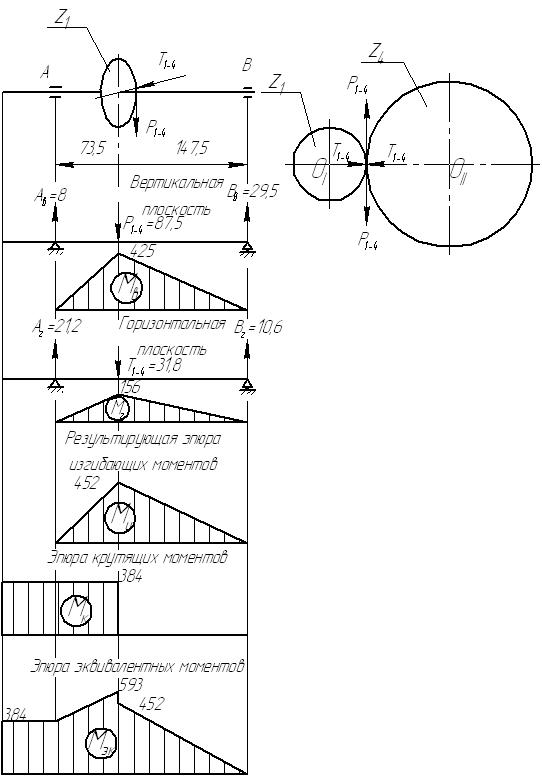
Просмотреть ближе
Рисунок 7.8 - Расчетная схема I вала при включении передачи z1—z4
7.1.3.3 Расчет
I вала
Из рассмотрения компоновочной схемы (рисунок 7.7) видно,
что расстояния между средними плоскостями подшипников и зубчатых венцов колес
z1
и
z2
одинаковы и равны 73,5 мм.
Поскольку делительный диаметр 1 колеса меньше
чем 2, то окружное и распорное усилия на 1 колесе будут больше чем на
2. Поэтому за расчетный случай принимаем тот, когда в зацеплении находятся
колеса z1—z4
(рисунок 7.8).
Крутящий момент, передаваемый
I
валом, Мк =384 кгс · см (таблице
7.2).
Усилия в зацеплении:
окружное


распорное


Определяем опорные реакции. В вертикальной плоскости
(рисунок 7.8):
.
.
Проверка:

В горизонтальной плоскости


Проверка: Результирующий изгибающий момент

Значения Мив и
Mиг
берутся по эпюрам изгибающих моментов.
Суммарные реакции опор

Вал скручивается моментом Mк
=384 кгс · см только на участке левее средней плоскости зубчатого венца шестерни
zu, что отражено на эпюре крутящих
моментов.
Наибольшее значение эквивалентного момента будет под
шестерней z1:

Определяем диаметр вала в этом сечении. Для упрощения
расчетов принимаем допускаемое напряжение
[σ–1]и = 600 кг/см2
.
Для конструктивного оформления любого вала необходимо
подобрать все детали, сопрягаемые с валом, с тем чтобы установить диаметры
ступеней валов и их длины, размеры шпоночных пазов и шлицев, конструктивные виды
и размеры галтелей, канавок и т. д. Кроме того, необходимо установить класс
шероховатости поверхностей и характер посадок деталей на валах, вид упрочнения и
термообработки, словом, все те данные, которые необходимы для
последующего расчета валов на выносливость.
Диаметры смежных ступеней вала и их осевые размеры
должны обеспечивать беспрепятственное прохождение деталей на место посадки, чтобы исключалось повреждение посадочных поверхностей и в связи с этим
нарушение характера посадки. Однако отношение диаметров смежных ступеней вала
должно быть возможно меньшим, но обеспечивать необходимые размеры упорных буртов
для подшипников, муфт, зубчатых колес и т. д. Всегда следует иметь в виду, что с
увеличением отношения диаметров смежных ступеней вала усталостная прочность вала
понижается в связи с ростом концентрации напряжений в переходном сечении.
В данном случае принимаем для закрепления зубчатых
колес z1
и
z4
на валу и передачи крутящего момента
призматические шпонки. В соответствии с темой проекта для соединения вала
электродвигателя с I
валом принята упругая муфта. Поскольку коробка скоростей составлена из
прямозубых цилиндрических передач, то осевые усилия на валах отсутствуют и
поэтому в качестве опор для всех валов предварительно принимаем однорядные
радиальные шарикоподшипники. Окончательный тип подшипника определится после
нахождения динамической грузоподъемности.
Подбор подшипников
качения.
Для определения коэффициента работоспособности
принимаем следующие условия: нагрузка только радиальная переменная, вращается
внутреннее кольцо подшипника, рабочая температура подшипника не превышает 100 °С, желательная долговечность Lh
=10000
Lh
ч, диаметр шейки вала
d1
=25 мм.
Требуемая динамическая грузоподъемность определяется
для более нагруженного подшипника в опоре А по уравнению
.
Принимаем: коэффициент динамичности нагрузки
kб
= 1,2
(таблица 3.63), температурный коэффициент
kT
= 1, кинематический коэффициент kк=1
.
По ГОСТ 8338—75 принимаем шарикоподшипник 205 легкой
серии, имеющей С = 1100 кгс. Условие С > Стр
выполнено.
Монтажные размеры подшипника
d=25
mm, D=52 мм, В = 15 мм, радиус фаски внутреннего кольца
r
= 1,5 мм.
С целью унификации подшипниковых узлов для опоры В
(менее нагруженной) принимаем тот же подшипник, как и для опоры А.
В зависимости от радиуса фаски внутреннего кольца
подшипника принимаем: высоту заплечика на валу
h
= 3 мм, радиус галтели
r1
= 1 мм (рисунок 4.43,
таблица 4.9). Тогда
диаметр, смежной ступени вала будет
d
= 25+6=31 мм (рисунок 7.9). Для обеспечения
беспрепятственного перемещения зубчатых колес
z1
и
z4
на посадочную ступень последнюю выполняем
диаметром 32 мм. С целью осевой фиксации этих же колес на валу выполняются
заплечики высотой h1
= 1
мм. Поэтому диаметр следующей ступени будет
d
=32+2=34 мм.
Диаметр консольного конца
I
вала был рассчитан ранее из условия прочности только на кручение,
поскольку этот участок вала изгибающим моментом не нагружен, если не учитывать
небольшой нагрузки со стороны муфты, которая может возникнуть в случае
несоосного расположения вала двигателя и
I вала.
В соответствии с заданием на проектирование для
соединения I
вала с валом двигателя выбираем упругую втулочно-кольцевую муфту (МУВП). По
расчетному диаметру вала и крутящему моменту принимаем по нормали МН 2096—64
муфту с условным обозначением:
МУФТА МУВП 1—22 МН 2096—64
(диаметр вала
d
= 22 мм, исполнение 1).
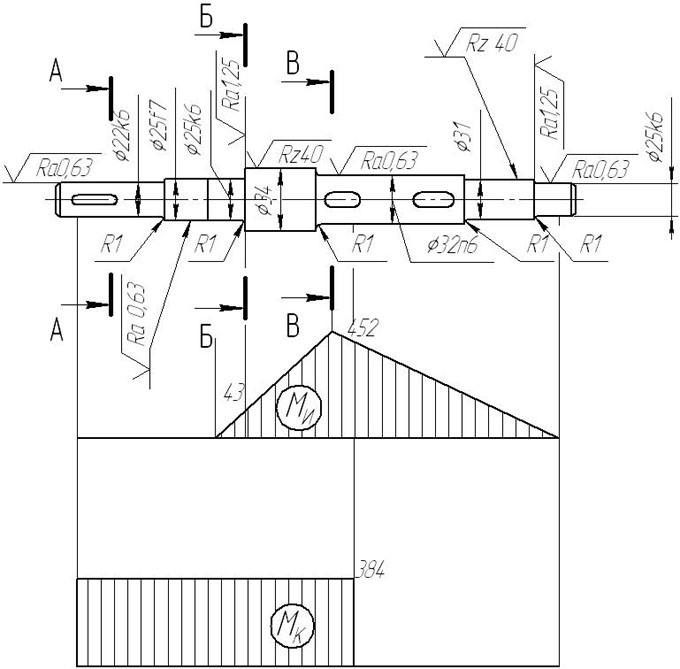
Просмотреть ближе
Рисунок 7.9 - К расчету I вала на выносливость
Таким образом определился диаметр консольной части
вала. Размеры муфты, принятые по таблицам ГОСТа или нормалей, переносятся
непосредственно на конструктивный чертеж. В расчетно-пояснительную записку
вносятся лишь те конструктивные элементы и их размеры, которые необходимы для
выполнения проверочных расчетов муфт.
Проверочный расчет
упругой втулочно-кольцевой муфты.
На рисунке 7.10 показан палец муфты с упругими
элементами. Из указанной нормали выписываем размеры: диаметр пальца
dп
= 10
мм, длина участка пальца
l2=19
мм, длина распорной втулки S
= 4 мм. Число пальцев
z
= 6. Радиус расстановки пальцев
R
= 34 мм.

Рисунок 7.10 - Палец муфты МУВП с упругими элементами
Упругие элементы муфты проверяются на смятие по
уравнению:
.
Передаваемый крутящий момент Мк
= 384 кгс · см (таблица
7.2). Допускаемое напряжение принимаем [σ]см=20
кг/см2 (см.
п.
3.32). Коэффициент режима работы принимаем
k
=1,25 (см. п. 3.32),
.
Пальцы проверяются на изгиб по уравнению:
.
Допускаемое напряжение на изгиб принимаем [σ]и
= 900 кг/см2.
.
Подбор шпонок и проверка прочности шпоночных
соединений.
Для закрепления зубчатых колес
z1
, z2
и полумуфты принимаем призматические шпонки
исполнения А по ГОСТ 29175—91, размеры сечений шпонок и пазов по ГОСТ 29175—91.
По диаметру вала
d
= 32 мм принимаем шпонку шириной
b
=10 мм, высотой h
=6 мм,
t1
= 3,5 мм;
t2
= 2,8 мм (рисунок 7.11).
Определим длину шпонки из условия прочности на смятие:
.
Материал шпонок — сталь 45 нормализованная. Принимаем
допускаемое напряжение [σ]см = 1000 кг/см2.
Рабочая длина шпонки
.

Просмотреть ближе
Рисунок 7.11 - Расчетная схема для проверки шпоночного соединения
Полная длина шпонки
l
=
lр
+ b = 8,8 + 10 = 18,8 мм.
Принимаем по ГОСТ 29175-91
l
=20 мм.
Условное обозначение: шпонка А 10×6×20
ГОСТ 29175—91.
По тем же стандартам подбираем шпонку для вала
d
=22 мм; b
= 8 мм; h
= 5 мм;
t1
= 3;
t2
= 2,3 мм.
Рабочая длина шпонки
.
Полная длина шпонки
l =
lр
+ b = 15,36 + 8 = 23,36 мм, принимаем l
= 25 мм.
Условное обозначение: шпонка А 8×5×25 ГОСТ 29175—91.
Выбор посадок, квалитетов
и шероховатости поверхностей
I вала.
По данным приложений
14 и
15 назначаем посадку
L0/k6
для внутренних колес подшипника.
По приложению 16 назначаем шероховатости:
Ra 0,63
для подшипниковых шеек и Ra 1,25 для торцов заплечиков вала, приняв предварительно класс
точности подшипника - 5. Посадки зубчатых колес и полумуфты назначаем по данным
приложения 17. Для зубчатых колес — посадку m6, для полумуфты — посадку
k6. По приложению
18 назначаем шероховатости:
Ra 0,63— на посадочные поверхности для зубчатых колес и полумуфты,
Rа 0,63
— для шейки вала под уплотнение. Шероховатость свободных
поверхностей принимаем Rz 40.
После определения радиальных и осевых размеров вала,
назначения квалитетов и шероховатости поверхностей и посадок производится
вычерчивание конструкции вала с указанием данных, необходимых для расчета вала
на выносливость.
Расчет
I вала
на выносливость.
Определим коэффициент запаса усталостной прочности для
трех предположительно опасных сечений: А — А; Б — Б; В — В (рисунок 7.9), принимая
при этом, что нормальные напряжения изменяются по симметричному циклу, а
касательные по пульсирующему, поскольку передачи нереверсивные.
На расчетной схеме (рисунок 7.9) необходимо представить
конструкцию вала с указанием предположительно опасных сечений и эпюры суммарных
изгибающих и крутящих моментов.
Сечение А — А.
Из расчетной схемы видно, что эта часть вала нагружена только крутящим моментом.
Концентрация напряжений вызывается шпоночным пазом.
Коэффициент запаса усталостной прочности по кручению
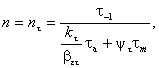
σ–1 = 2600
кг/см2;
τ–1
= 1300 кг/см2;
σв
= 5200 кг/см2;
ψτ
= 0 (таблица
3.57)
ετ
=0,89 (
таблица3.58);
β = 1,0
(
таблица
3.59);
kτ
= 1,40 (таблица
3.60)
При нереверсивном вращении напряжения изменяются по
пульсирующему циклу, поэтому амплитуда и среднее напряжение цикла касательных
напряжений
.
Момент сопротивления кручению поперечного сечения вала с учетом ослабления
шпоночным пазом
;

.
Сечение Б —
Б. Для этого сечения (концентратор напряжения № 5),
(рисунок 3.50) отношение
; отношение
.
Коэффициенты запаса усталостной прочности:
а) по изгибу
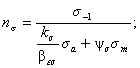
kσ
= 2,23 (таблица 3.60); β = 1 (таблица 3.59); εσ
= 0,88 (таблица 3.58); ψσ = 0 (таблица 3.57).
При симметричном цикле напряжений изгиба
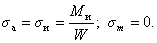
.
.
;
б) по кручению
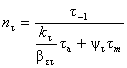
kτ
= 2,12 (Приложение 5); β = 1 (таблица 3.59); ετ = 0,81 (таблица 3.58); ψτ =0 (таблица 3.57)
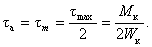
.
.
.
Результирующий коэффициент запаса не вычисляется,
поскольку очевидно, что он получится значительно больше допустимого =1,5÷2,5.
Сечение В — В.
Концентрация напряжений обусловлена шпоночным пазом. (Концентратор напряжения №
15,
рисунок 3.50.)
Коэффициенты запаса по усталостной прочности:
а) по изгибу
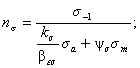
kσ
= 1,7 (таблица
3.60); εσ =0,88 (таблица
3.58); β = 1 (таблица
3.59); ψσ = 0 (таблица
3.57);W = 2,73 см3.
.
;
б) по кручению 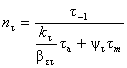
kτ
= 1,5 (приложение 8); ετ =0,81
(таблица 3 58); β =1 (таблица 3.59); ψτ =0 (таблица 3.57)
Wк
= 5,94 см3.
.
.
Результирующий коэффициент запаса по усталостной
прочности:
.
Для всех сечений
n
> [n].
7.1.3.4 Расчет
II вала
Если возможны различные комбинации включения передач,
то необходимо путем анализа установить такую из них, при которой нагрузки на
валы окажутся самыми неблагоприятными, вызывающими наибольшие эквивалентные
моменты. Этот случай принимается за расчетный.
Наиболее простым, но весьма трудоемким способом
является составление расчетных схем вала при всех возможных комбинациях передач.
Затем по эпюрам эквивалентных моментов легко выявляется та комбинация передач,
при которой вал испытывает наибольшие нагрузки.
В данном примере возможны 4 комбинации включений
передач (рисунок 7.3): а) z1—z4;
z3—z7;
6) z2—z5;
z3—z7;
в) z1—z4;
z6—z8;
г) z2—z5;
z6
— z8.
Нетрудно видеть, что в зацеплении
z6—z8
возникают меньшие окружное и распорное усилия, чем в зацеплении
z3—z7,
поскольку парами z3—z7
и z6—z8
преобразуются по два крутящих момента (Мк = 765 кгс · см и 855
кгс · см, таблица 7.2), передаваемые
II
валом, но делительный диаметр колеса
z3
меньше, чем колеса z6
(см, таблица 7.6). Из компоновочной схемы видно, что расстояния между плоскостями
действия сил при включении передачи
z3—z7
примерно такие же, как и при включении передачи
z6—z8.
Таким образом, комбинации в и г
исключаются, так как они дают более легкий случай нагружения вала. Наконец,
необходимо выяснить, какая из комбинаций а или б дает более
тяжелый случай нагружения. Эту задачу решим составлением двух расчетных схем
(рисунки 7.12 и 7.13).
Комбинация а.
Расстояния между плоскостями действия сил принимаются
по компоновочной схеме (рисунок 7.7). Крутящий момент, передаваемый валом, Мк
=855 кгс·см. Определим усилия в зацеплении.
Окружные: Р4–1=87,5
кг; Распорные:
T4–1=
31,8 кг; T3–7
= P3–7·tgα=
165·0,364 = 60 кг. Определим опорные реакции.
В вертикальной плоскости (рисунок
7.12) ΣМA=
0;
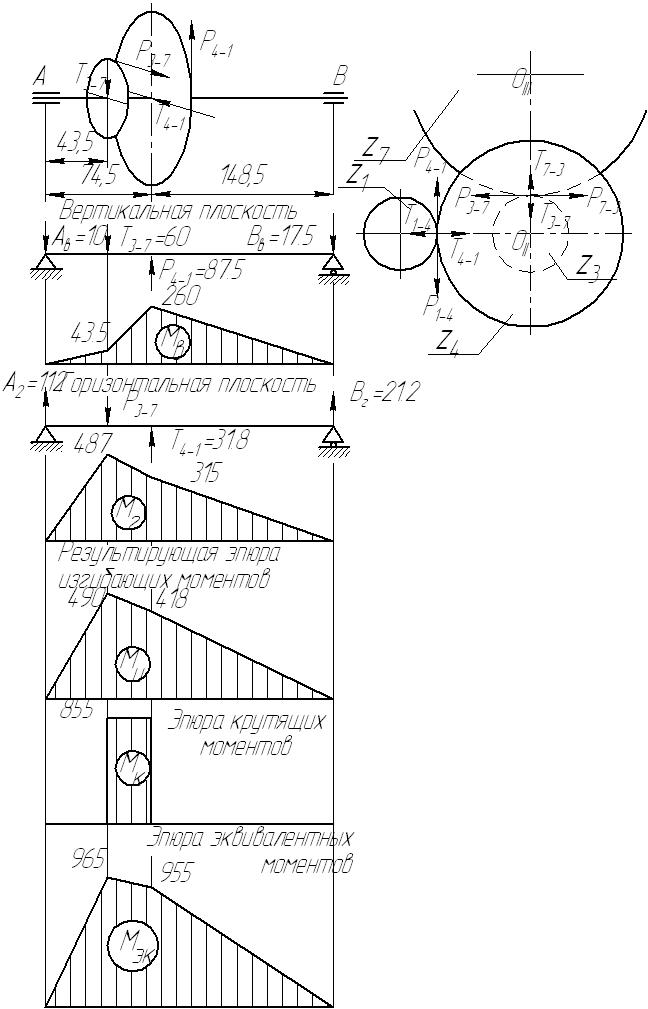
Просмотреть ближе
Рисунок 7.12 - Расчетная схема II вала при включении передач z1—z4
и z3—z7
P1–4
· 7,45 – T3–7
· 4,35 – Вв · 22,3 = 0;
Вв
= 17,5 кг.
ΣМв =
0; Ав · 22,3 +
T3–7
· 17,95 – Р4–1 · 14,85 = 0;
Ав
= 10 кг.
Проверка: Σy
=0; 87,5 – 60 – 10 – 17,5=0;
в
горизонтальной плоскости
ΣМA = 0;
T4–1
· 7,45 + Вг · 22,3 – Р3–7 · 4,35 = 0;
Вв
= 21,2 кг.
ΣМв =
0; Г4–1 · 14,85 –
P3–7
· 17,95 + Aг
· 22,3 = 0;
Аг=
112 кг.
Проверка: Σy
=
0; 112
– 165
+
31,8
+
21,2
=
0.
Результирующие изгибающие моменты

Суммарные реакции
опор:

Эквивалентные моменты:

Комбинация б.
Поскольку расчеты реакций опор и различных моментов
производятся так же, как и в предыдущем случае, то записываем лишь конечные
результаты вычислений, опуская промежуточные операции. Расчетная схема вала
показана на рисункке 7.13.
Усилия в зацеплении.
Окружные:
,
.
Распорные:
T2–5 = P2–5·tgα = 80 · 0,364 = 29,1
кг;
Т3–7
= P3–7·tgα
= 148 · 0,364 = 54 кг.
Реакции опор.
В вертикальной плоскости Ав
= 17 кг, Вв = 43 кг.
В горизонтальной плоскости Аг
= 109,35 кг; Вг = 9,55 кг.
Результирующие изгибающие
моменты
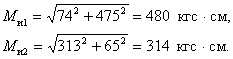
Суммарные реакции опор:
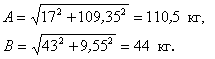
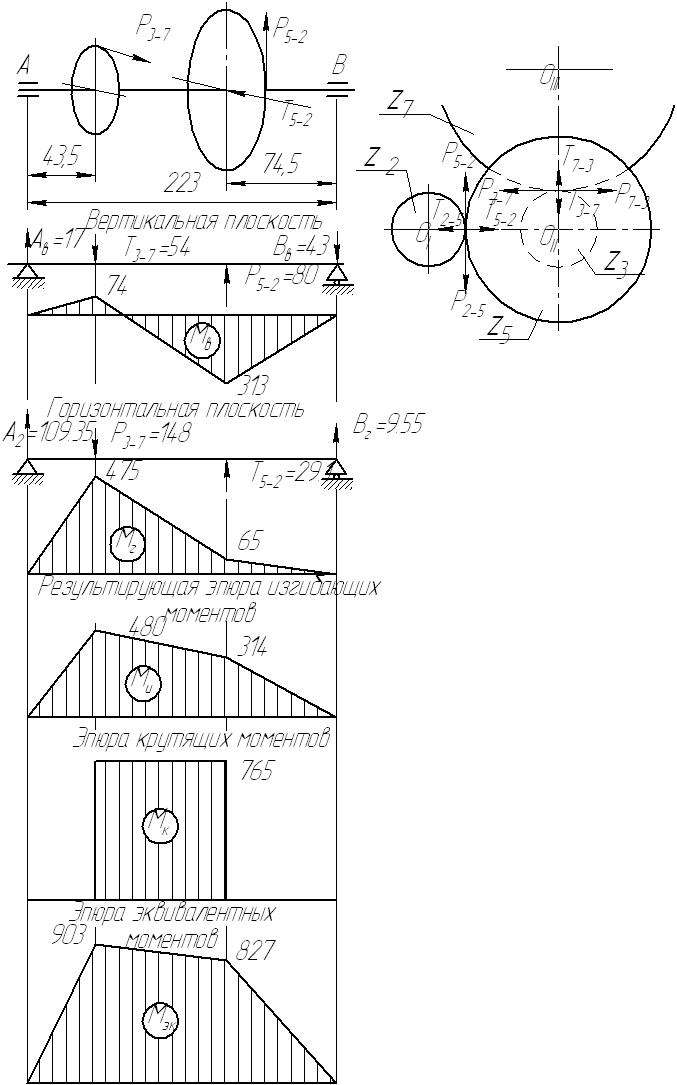
Просмотреть ближе
Рисунок 7.13 - Расчетная схема II вала при включении передач z2–z5
и z3–z7
Эквивалентные моменты:


Из рассмотрения эпюр эквивалентных моментов (рисунки
7.12, 7.13) следует, что за расчетный случай нужно принять тот, при котором в
зацеплении находятся колеса z1–z4
и z3–z7,
так как при этом вал нагружен наибольшим эквивалентным моментом.
Определяем диаметр вала, принимая допускаемое
напряжение
[σ–1]и
= 600 кг/см2.
.
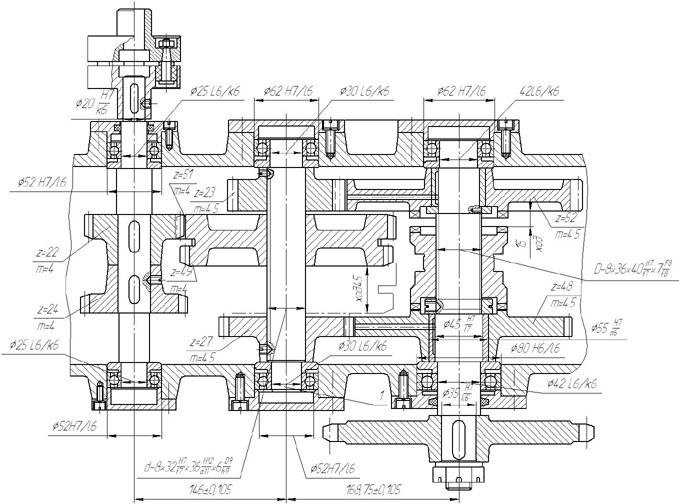
Просмотреть ближе
1-шлицевой вал постоянного сечения
Рисунок 7.14 - Общий вид коробки скоростей
Подбор подшипников
качения.
Диаметры шеек
II
вала под подшипники были определены, исходя из условия прочности на кручение
вала, и приняты d2=30
мм.
Требуемая динамическая грузоподъемность определяется
по большей реакции в опоре А по условиям, принятым для подшипников
I
вала, поскольку эти условия одинаковы.

По ГОСТ 8338–75 принимаем подшипник 206 легкой серии,
имеющий С = 1530 кгс. Монтажные размеры подшипника
d =
30 мм, D
= 62 мм,
B
= 16 мм,
r
= 1,5
мм. С целью унификации подшипниковых узлов для опоры
В принимаем тот же подшипник, хотя нагрузка в этой опоре примерно в 4
раза меньше, чем в опоре А.
Передача крутящих моментов валом осуществляется
посредством прямобочных зубчатых (шлицевых) соединений, причем для упрощения
конструкции вал
I
принят постоянного сечения на всей длине между подшипниковыми шейками (рисунок
7.14). В данном случае диаметр подшипниковых шеек является определяющим при
выборе размеров шлицевого соединения. Принимаем соединение легкой серии с
центрированием по внутреннему диаметру
d.
Выбор наиболее точного и сравнительно
дорогого метода центрирования обусловлен высокой точностью зубчатых передач
(колеса 6-й и 7-й степени точности). Из ГОСТ 1139–80 выписываем размеры
шлицевого соединения (28×32×36;
d
= 32;
d1
= 30,4; f
= 0,4;
r
= 0,3;
D
= 36;
z =
8 (рисунок 7.15) (размеры, мм).
Свободный выход фрезы при нарезании зубьев обеспечен,
поскольку d1
= 30,4 мм больше диаметра подшипниковой шейки. Высота заплечика для упора
внутреннего кольца подшипника
, что отвечает рекомендации.

Просмотреть ближе
Рисунок 7.15 - Схема для расчета шлицевого соединения
Проверка прочности
шлицевого соединения.
Проверка прочности на смятие производится по уравнению
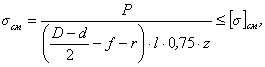
где
l
= 49 мм – длина ступицы блока.
По
таблице 3.61 принимаем [σ]см
= 500 кг/см2.
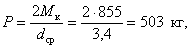
где
.
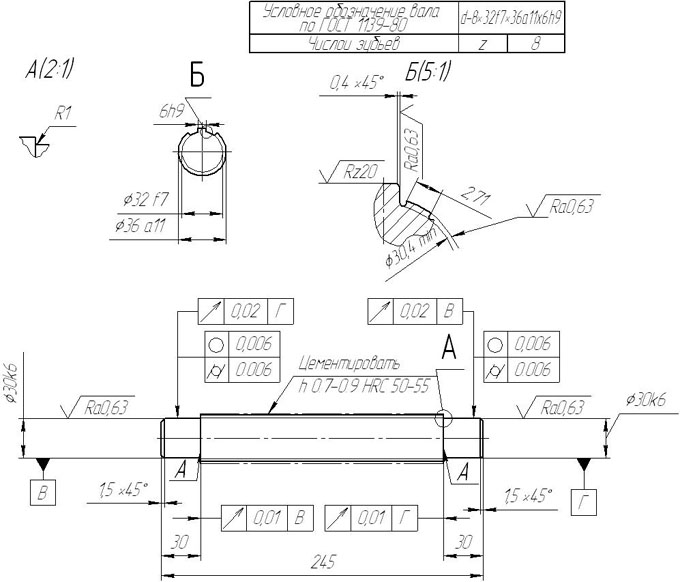
Просмотреть ближе
Рисунок 7.16 - Вал шлицевый
Прочность соединения обеспечена, так как σсм
< [σ]см.
Выбор посадок, квалитетов и шероховатости
поверхностей II
вала.
По данным
Приложений 14 и 15 назначаем посадку
k6
для внутренних колец подшипников, а по Приложению 16 назначаем
шероховатости: Ra 0,63 для подшипниковых шеек и Ra
1,25 для торца заплечиков, приняв предварительно класс точности
подшипника 6. Для неподвижных зубчатых колес и подвижного блока принимаем
одинаковый характер посадки, поскольку шлицевый вал по всей длине
обрабатывается одинаково, назначаем посадку H12/а11. Условное обозначение
d-
8×32H7/f7×36H12/a11×6D9/h9 (рисунок 7.16).
Расчет
II вала
на выносливость.
Рассмотрим случай включения передач
z1–z4
и z3–z7
при котором вал нагружен наибольшим
результирующим изгибающим моментом Ми1 = 490кгс · см и в то же время наибольшим крутящим моментом Мк
= 855 кгс · см.
Определим результирующий коэффициент запаса
усталостной прочности п в сечении А – А (рисунок 7.17).
Коэффициенты запаса усталостной прочности:
а) по изгибу
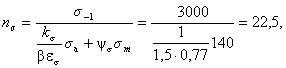
где σ–1
= 3000 кг/см3 (таблица 3.57);
kσ
= 1 (концентратор № 13,
приложение 8);
β = 1,5 (таблица 3.59); εσ = 0,77 (таблица
3.58); ψσ = 0 (таблица 3.57).
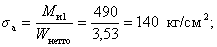
Wнетто
= 3,53 см3
вычислено по уравнению
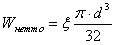
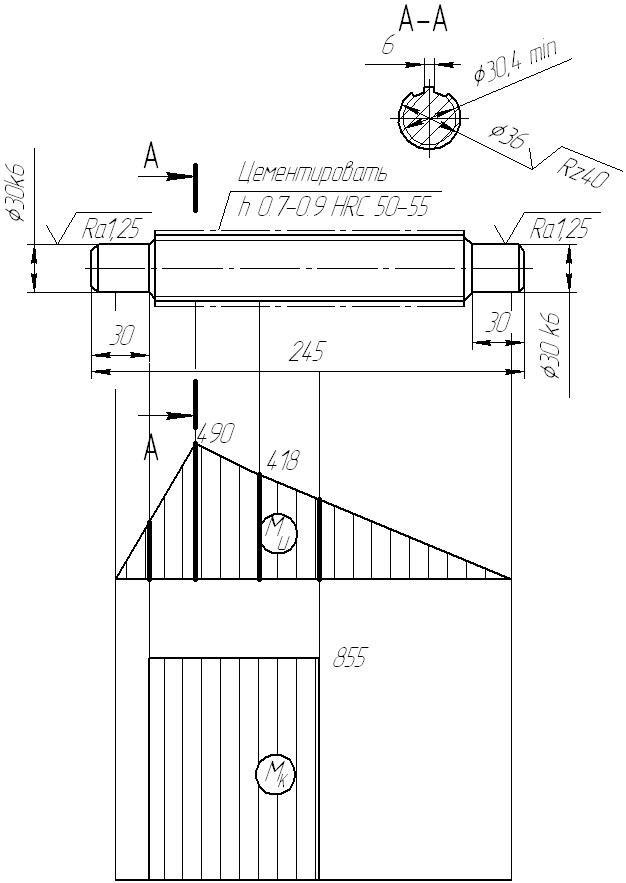
Просмотреть ближе
Рисунок 7.17 - К расчету II вала на выносливость
б) по кручению
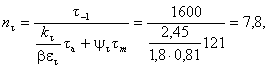
где τ–1 = 1600 кг/см2, ψτ
= 0.
kτ
= 2,45 (концентратор № 13,
Приложение 8);
β = 1,8 (таблица 3.59); ετ =0,81 (Приложение 8);
.
Результирующий коэффициент запаса не вычисляется,
поскольку очевидно, что он получится большим допустимого
n =
1,5÷2,5.
7.1.3.4 Расчет III вала
Вал передает 4 различных крутящих момента (таблица 7.2).
Выясним, какая из комбинаций включения зубчатых колес дает наиболее тяжелый
случай нагружения путем анализа данных, собранных в таблице 7.8.
Таблица 7.8
Комбинация включения зубчатых колес |
Муфта включена (рисунок 7.13) |
Частота вращения
III
вала, п об/мин |
Передаваемый крутящий момент М кгс·см |
Окружное усилие на звездочке |
а)
z1–z4;
z3–z7
б)
z2–z5;
z3–z7
в)
z1–z4;
z6–z8
г) z2–z5;
z6–z8 |
влево
влево
вправо
вправо |
710
563
631
795 |
1645
1840
1460
1290 |
116
146
130
104 |
|
Из рассмотрения компоновочной схемы (рисунок 7.7) и
данных таблицы видно, что наиболее легким случаям нагружения отвечают комбинации
включения а и г.
Так как при комбинациях включения б и в
расстояния между плоскостями действия сил различны (рисунок 7.7), то неочевидно,
какая из этих комбинаций может быть принята за расчетную. Выясним это
составлением расчетных схем для обеих комбинаций.
Комбинация б (рисунок
7.18).
Расстояния между плоскостями действия сил принимаются
по компоновочной схеме (рисунок 7.7).
Усилия в зацеплении. Окружное: Р3–7
= 165 кг, распорное: Т7–3 =60 кг. Нагрузка на вал от цепной
передачи
Sв
=
kв·Р =
1,05 · 146 =153 кг, где коэффициент нагрузки
kв
= 1,05 (таблица 3.53).
Sв
раскладываем на две составляющие в вертикальной и
горизонтальной плоскостях (рисунок 7.18).
Sвв
= SВ
cos
45° = 1530·707= 108 кг =
SВг.
Реакции опор: в вертикальной плоскости (рисунок 7.18)
ΣMA
= 0; SВв27,4
– Вв22,4
+
Т7–3 ·
4,4
=
0; Вв
= 144 кг.
ΣMВ
= 0; Ав · 22,4 – Т7–3
· 18 + SВв
· 5 = 0; Ав = 24 кг.
Проверка: Σy
= 0; 60 + 108 – 24 – 144=0.
В горизонтальной плоскости
ΣMA
= 0; Р7–3 ·
4,4 – ВГ22,4 +
SВг
· 27,4 = 0; Вг = 165 кг.
ΣMВ
= 0; Аг · 22,4 – P7–3 ·
18 + SBr ·
5=0; Аг = 108кг.
Проверка: Σy
=0; 165 + 108 – 108 – 165=0.
Результирующие изгибающие моменты

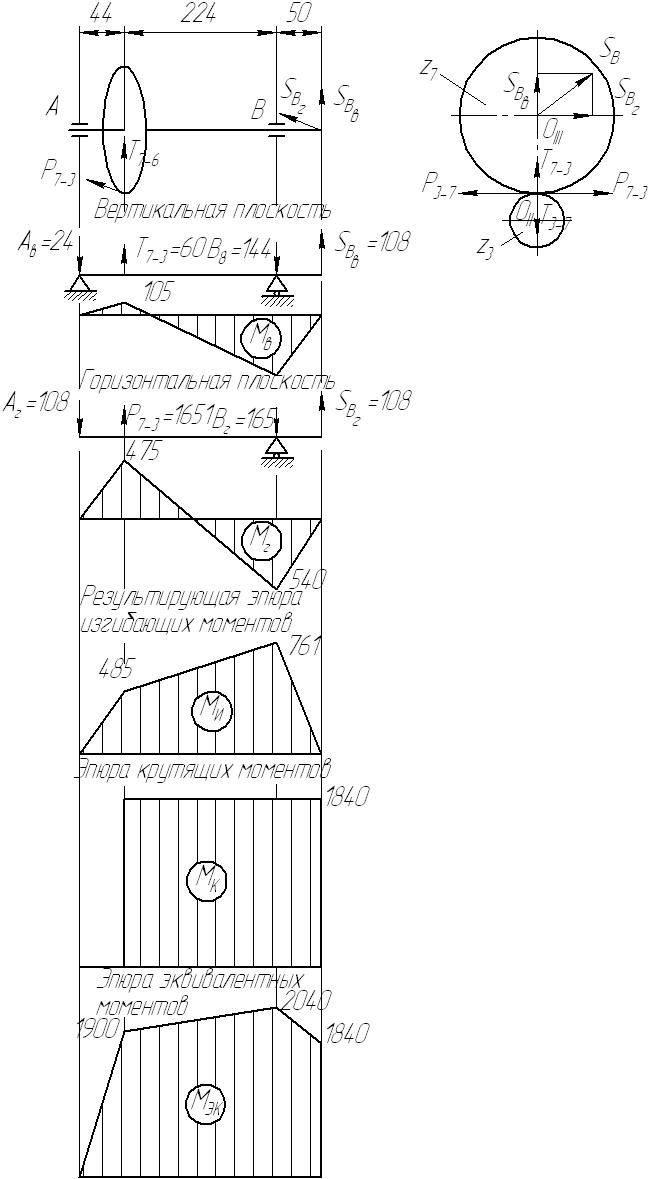
Просмотреть ближе
Рисунок 7.18 - Расчетная схема III вала при включении передач z1
– z4 и z3 – z7
Суммарные реакции опор:

Эквивалентные моменты:

Комбинация в (рисунок
7.19).
Усилия в зацеплении. Окружное:
.
Распорное:
T8–6
= P8–6·tgα
= 141 · 0,364 = 52 кг;
Нагрузка на вал от цепной передачи
SB
=
kB·Р
= 1,05 · 130 =137 кг.
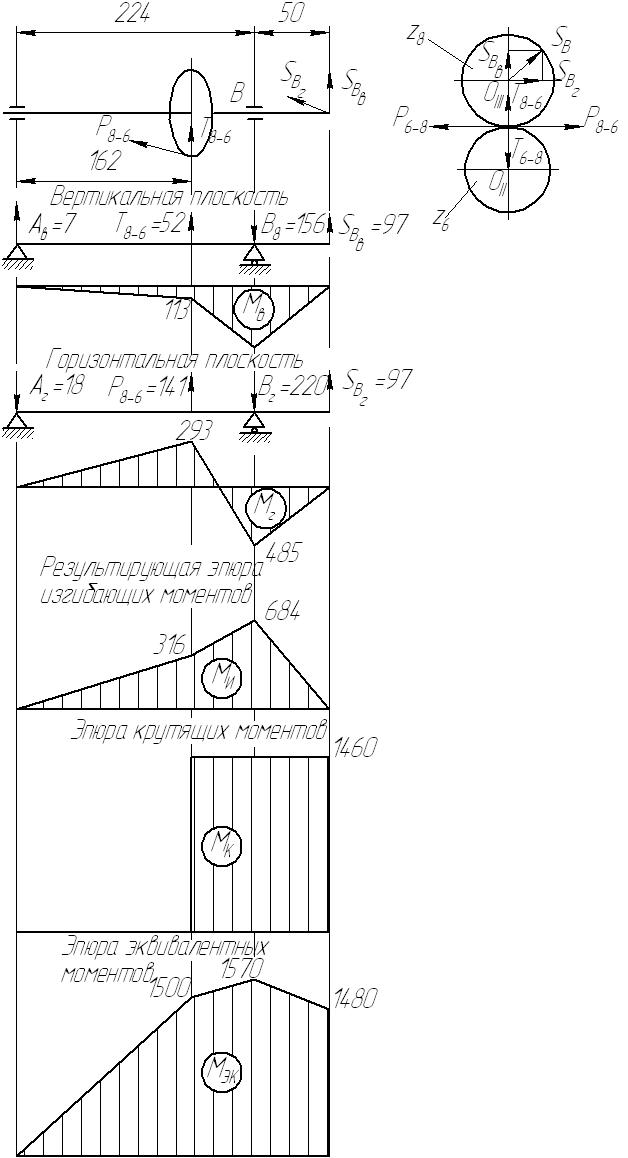
Просмотреть ближе
Рисунок 7.19 - Расчетная схема III вала при включении передач z2–z5
и z6–z8
Так как реакции опор, изгибающие и эквивалентный
моменты определяются так же, как и в предыдущем случае, то записываем конечные
результаты, опуская промежуточные операции.
Реакции опор. В вертикальной плоскости: Ав
= 7 кг; Вв = 256 кг.
Проверка: Σy
= 0; 97 – 156 + 52 + 7 = 0.
В горизонтальной плоскости Аг = 18 кг; Вг
= 220 кг.
Проверка: Σy
=0; –18 + 141 – 220 + 97 = 0.
Результирующие изгибающие моменты:

Суммарные реакции опор А = 19 кг; В =270
кг.
Эквивалентные моменты

Из рассмотренных эпюр эквивалентных моментов (см. рисунки
7.18 и 7.19) следует, что за расчетный случай нужно принять тот, при котором в
зацеплении находятся колеса z1–z4
и
z3–z7,
так как вал при этом нагружен наибольшим
эквивалентным моментом.
Определяем диаметр вала, принимая допускаемое
напряжение
[σ–1]и
= 600 кг/см2

Подбор подшипников
качения.
Подбор подшипников ведем по большим реакциям опор:
A
= 110 кг, возникающей при комбинации б зацепления зубчатых колес и В
= 270 кг при комбинации в. Поскольку осевые усилия на валу
отсутствуют, то в опорах устанавливаем радиальные шарикоподшипники, диаметры
шеек вала под которые предварительно определены по условию прочности на кручение
и приняты d3
= 40 мм. На валу, кроме подшипников, посажены два свободно вращающихся зубчатых
колеса и полумуфта (см. рисунок 7.14), причем размеры подшипниковых шеек и шлицев
следует согласовать с соответствующими стандартами. Таким образом, вал имеет
несколько ступеней, размеры которых должны позволить свободную сборку узла вала
внутри корпуса коробки. Разность смежных ступеней вала должна быть возможно
меньшей, но обеспечивать заплечики необходимой высоты для упора внутренних колец
подшипников. Если в обеих опорах вала установить подшипники одинакового размера,
то окажется невозможным выполнить ряд указанных условий. Поэтому принимаем
диаметры подшипниковых шеек различными: в опоре
A
d
= 30 мм, а
в опоре В d
= 40 мм. Требуемая динамическая
грузоподъемность для подшипника в опоре А:

По ГОСТ 8338 – 75 принимаем шарикоподшипник 206 легкой
серии, имеющий С = 1530 кгс. Монтажные размеры подшипника
d
= 30 мм;
D
=62 мм; B
= 16 мм; r
=1,5 мм.
Требуемая динамическая грузоподъемность для подшипника
в опоре В:

По тому же стандарту принимаем, шарикоподшипник 208 с
размерами d
= 40 мм, D
= 80 мм, В = 18 мм, r
=2
мм. Условия работы подшипников приняты такие же,
как и для подшипников I
и
II
валов.
Размеры шеек вала под втулки, запрессованные в ступицы
зубчатых колес, принимаем с таким расчетом, чтобы обеспечить необходимую высоту
заплечиков для упора колец подшипников. Подвижная часть кулачковой муфты
перемещается по шлицевой части вала. Принимаем шлицевое соединение легкой серии
с центрированием по внутреннему диаметру
d,
причем наименьших размеров, но
обеспечивающих свободный проход фрезы над поверхностью
Æ
35f8 при нарезании зубьев. Из
стандарта
выписываем размеры соединения
d
8×36×40;
d
= 36,
D =
40,
b =
7, d1=34,5;
f
=0,4;
r
=0,3; z
=8 (размеры в мм). Размер
d>Æ
35f7,
что обеспечивает выход фрезы.
Проверка прочности
шлицевого соединения.
Проверка производится по уравнению:
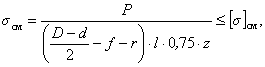
Длина шлицев в полумуфте
l
=62 мм получена из конструктивных соображений.
По
таблице 3.61 принимаем [σ]см =500 кг/см2.

где

,
,
следовательно, прочность соединения обеспечена.
Подбор шпонки и
проверка прочности шпоночного соединения.
Для закрепления звездочки на валу принимаем
призматическую шпонку исполнения A, размеры сечения шпонки и
пазов по ГОСТ 29175 – 91.
По диаметру вала
d =
35 мм принимаем шпонку шириной
b =
10 мм, высотой h
= 6
мм,
t1 =3,5 мм,
t2
= 2,8 мм (рисунок 3.64).
Определим длину шпонки из условия прочности на смятие:
.
Материал шпонки — сталь 45 нормализованная. Принимаем
допускаемое напряжение [σ]см = 1000 кг/см2. Рабочая длина
шпонки:
.
Полная длина шпонки
l =
lр
+ b
= 38,6 + 10 = 48,6 мм.
Принимаем по ГОСТ 29175 – 91
l
= 50 мм.
Условное обозначение: шпонка A 10×6×50 ГОСТ 29175 – 91.
Выбор посадок, квалитетов
и шероховатости поверхностей
III
вала.
По данным Приложений 14 в 15 назначаем посадку
kп для
внутренних колец подшипников, а по Приложению
16 определяем шероховатости Rz 3,2
для подшипниковых шеек и Rz 6,3 для торцов заплечиков, так же как для
I
и
II
валов принимаем класс точности подшипников
В. По приложению 17 для зубчатых колес, свободно вращающихся на валах и
включаемых муфтами, назначаем посадку
и
посадку звездочки на валу .
Для втулки в зубчатом колесе назначаем
посадку шлицевого соединения полумуфты и вала .
Условное обозначение
d
8×36×40 .
Контактные поверхности шлицев обрабатываются одинаково
Rz 3,2 (рисунок 7.16).
Подбор и проверочный
расчет кулачковой муфты.
Для соединения зубчатых колес с валом применим сцепную
кулачковую муфту с кулачками трапецеидального профиля. По
таблицам 3.64,
3.65,
и
рисунок
3.76 принимаем
основные
размеры муфты:
D
= 90,
z
= 7,
h =
6, а =10, α = 3° (рисунок 7.20).
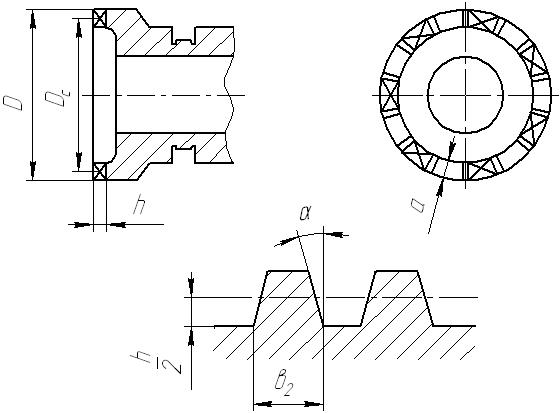
Просмотреть ближе
Рисунок 7.20 - К расчету кулачковой муфты
Допустимость включения муфты на ходу проверяется по
уравнению:
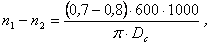
где
Dc
= D
– а = 90 – 10 = 80 мм.
.
При правом и левом включении муфты разность п1
– n2
оказывается меньше 178 об/мин: 710–566=147 об/мин, 795 – 631 = 164 об/мин.
Кулачки муфты проверяются на смятие и изгиб:
,
где расчетный момент Мр =
Mкk=
1840 · 1,25 = 2300 кгс · см,
k
= 1,25. [σ]см
= 500 кг/см2.


Для стали 40
X, из
которой изготавливаются зубчатые колеса, имеющие кулачки, и подвижная часть
муфты, допускаемое напряжение изгиба
[σ]и=0,25·σT
=0,25·5000= 1250 кг/см2,
.
Необходимое усилие включения муфты
,
где
f’ =
f
= 0,05
(с. 241),
d —
средний диаметр шлицев,


Усилие выключения

Расчет
III
вала на выносливость.
Определим коэффициент запаса усталостной прочности для
двух предположительно опасных сечений
A –
А и Б – Б (рисунок 7.21) в том случае, когда включены передачи
z1
– z4
и z3
– z7
(рисунок 7.18) и передается наибольший
крутящий момент и в то же время вал нагружен наибольшими изгибающими моментами.
Сечение А—А.
Из расчетной схемы (рисунок 7.21) видно, что вал в этом
сечении нагружен изгибающим моментом Ми =513 кгс · см и
крутящим моментом Мк = 1800 кгс · см. Концентрация напряжений
вызывается галтелью (концентратор № 5,
рисунок
3.50) kσ
= 1,94 при
= 2,5 и
= 0,03 (рисунок 7.21).
По этим же данным
Приложения 5 принимаем
kτ
= 1,59.
Коэффициент запаса усталостной прочности:
а) по изгибу
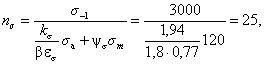
где

.
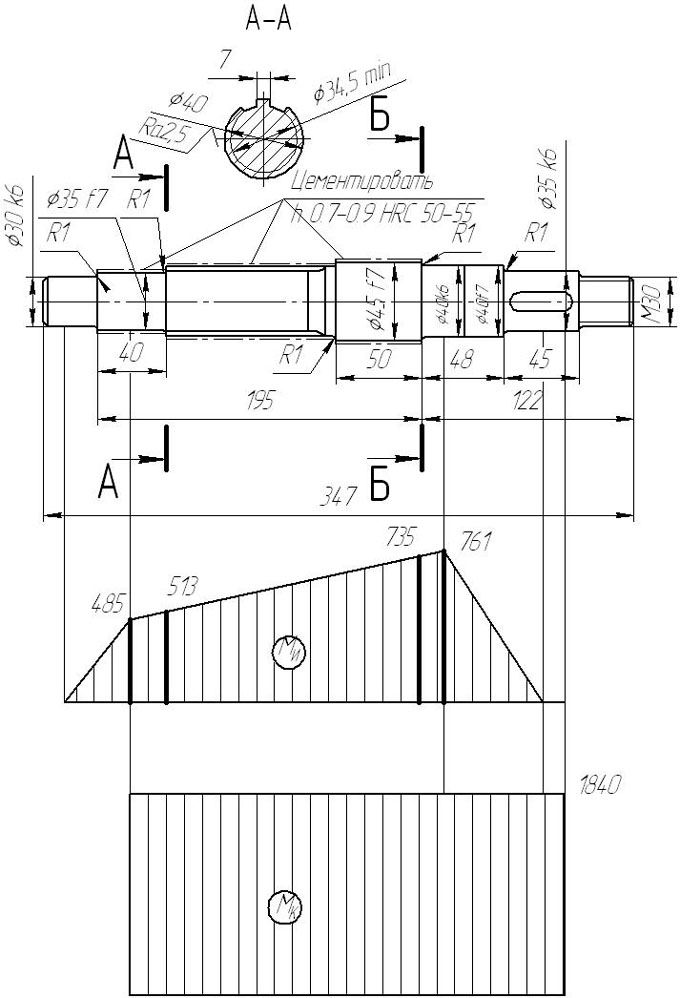
Просмотреть ближе
Рисунок 7.21 - К расчету III вала на выносливость
Для симметричного цикла напряжений изгиба σm
= 0; β = 1,8 (таблица 3.59); εσ =0,77 (таблица 3.58);
ψσ
= 0,05;
б) по кручению

где

ετ =
0,81(таблица 3.58); β = 1,8 (таблица 3.59); ψτ =0.
Результирующий коэффициент запаса усталостной
прочности
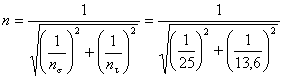
превышает допустимые значения.
Сечение Б—Б.
Концентрация напряжений вызывается также галтелью. По
тем же таблицам принимаем
kσ
= 1,94; при
,
,kτ
= 1,59.
Коэффициент запаса усталостной прочности:
а) по изгибу
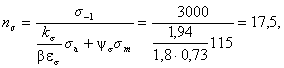
где


σm
= 0; β = 1,8; εσ =0,78;
ψσ
= 0,05;
б) по кручению

ετ
= 0,78; β
= 1,8; ψτ
=0.
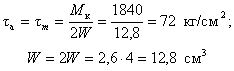
Результирующий коэффициент запаса усталостной
прочности

превышает допустимые значение.
В данном примере валы обладают избыточным запасом
усталостной прочности, поскольку диаметры шеек под подшипники определялись не
только из условий прочности, но также из необходимости одинаковой долговечности
опор, не меньше 10000 часов.
|