3.26 Расчет
шпоночных и зубчатых (шлицевых) соединений
3.26.1
Шпоночные соединения
В коробках скоростей и подач находят применение
призматические шпонки, направляющие с креплением на валу и сегментные. Размеры
сечений призматических шпонок и пазов в валах и ступицах выбираются по ГОСТ
29175—91, длины призматических шпонок— по ГОСТ 29175—91, размеры сегментных шпонок
и пазов — по ГОСТ 24071—97, размеры сегментных шпонок — по ГОСТ 24071—97,
направляющие призматические шпонки с креплением на валу — по ГОСТ 14737—69.
Клиновые шпонки, вызывающие распорные усилия при
сборке и эксцентриситет посадки, применения не находят. Существенными
недостатками шпоночных соединений являются наличие очагов концентрации
напряжений в шпоночных пазах, что может являться причиной усталостного
разрушения валов и тонких ступиц, ограниченные возможности передачи крутящих
моментов одной шпонкой и неудобство применения двух шпонок. Следует избегать
постановки двух шпонок, каждая из которых может передавать половину нагрузки
лишь в том случае, когда точности изготовления шпонок и пазов достаточно
высокие. Если же применяются две шпонки, то их следует располагать под углом 120
или 180°. К недостаткам соединений с призматическими шпонками необходимо отнести
также сравнительно плохое качество центрирования, возможность перекосов и
ускоренный износ при осевом перемещении деталей по направляющим шпонкам, высокие
напряжения на рабочих поверхностях, что при передаче нагрузок, особенно ударного
характера, может вызвать смятие рабочих поверхностей и поворот шпонок в пазу,
трудность обеспечения взаимозаменяемости из-за необходимости подбора или ручной
пригонки шпонки по пазу. Этого недостатка не имеют сегментные шпонки, которые к
тому же более технологичны.
Призматические шпонки с закругленными торцами в
пазах валов монтируются с некоторым натягом, а с боковыми сторонами паза ступиц
выполняется свободное соединение. Поэтому призматические шпонки не удерживают
деталь в осевом направлении и требуют дополнительного крепления. По
технологическим соображениям шпоночные пазы на одном валу следует выполнять
одного сечения так, чтобы оси пазов лежали вдоль одной образующей. Рассчитывать
шпонку следует по меньшему диаметру вала. Применение общей шпонки для нескольких
деталей нежелательно вследствие возможного перекоса шпонки и неравномерного
распределения напряжений по рабочим граням (рисунок 3.63, а), лучше применять
отдельные шпонки для каждой детали (рисунок 3.63, б). Чтобы не допускать повышения
концентрации напряжений, не рекомендуется доводить шпоночные пазы до выточек
(рисунок 3.63, б).

Просмотреть ближе
а – неправильное; б –
правильное; в – нерекомендуемое
Рисунок 3.63
- Расположение шпонок
Размеры шпонок выбираются в зависимости от
принятого диаметра вала по таблицам стандарта, а затем производится условный расчет
на смятие в предположении, что напряжения на узких рабочих гранях шпонки и паза
распределяются равномерно (рисунок 3.64, в). При проектном расчете определяется
длина шпонки lp, по которой
вычисляется общая длина шпонки
, согласуемая со стандартом(ГОСТ 29175–91), b —
ширина шпонки. Условие прочности:
,
где Мк— передаваемый крутящий момент, кгс·см;
d— диаметр вала, h — высота сечения шпонки (рисунок
3.64,6);.
lр — рабочая длина шпонки. Для
шпонки с плоскими торцами (рисунок 3.64, а, исполнение 3) полная длина l шпонки и
рабочая длина lр одинаковы. Для исполнения l: lр
= l - b (рисунок 3.64, а). Размеры, см; [σ ]см —
допускаемое напряжение смятия, кг/ см2 .

Просмотреть ближе
а –
исполнение шпонок; б – размеры сечений шпонок и валов; в – расчетная схема для
соединения с призматической шпонкой
Рисунок 3.64
- Соединение с
призматическими шпонками
Стандартные шпонки изготавливаются из
углеродистой или легированной стали с пределом прочности не менее 50 кг/мм2,
например, стали ст. 6, 45, 50 [σ ]см для неподвижных соединений при
стальной ступице принимают 1000÷1200 кг/см2 , при чугунной ступице
500÷600 кг/см2 . При прессовых посадках деталей на вал допускаемое
напряжение повышается на 30÷50 %, при σсм << [σ]см можно принять шпонку на номер меньше и
повторить расчет. При ударной нагрузке [σ ]см понижают на 20÷40 %, а
при спокойной повышают на 25 %. Для подвижных соединений принимают
[σ ]см=200÷300 кг/см2 с целью ограничения износа. Если
прочность одной шпонки недостаточна, т. е. при σсм > [σ]см,
ставятся две шпонки, а сегментные две или даже три в одном пазу.
Для призматических закладных шпонок напряжения
среза малоопасны, поэтому проверки на прочность, как правило, не производится.
В коробках передач находят применение на малонагруженных участках валов
сегментные шпонки. В связи с глубокой посадкой в вал сегментные шпонки менее
подвержены выворачиванию из пазов, но глубокий паз значительно ослабляет вал.
Сегментные шпонки (рисунок 3.65,а), так же, как и призматические, выбираются по
таблицам стандарта в зависимости от диаметра вала, а затем проверяются на смятие и
срез по уравнениям:
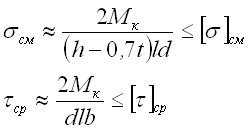
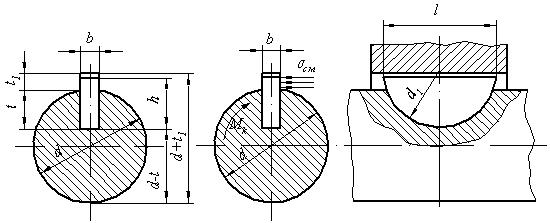
Просмотреть ближе
а –
размеры шпонок и пазов; б – расчетная схема для соединения с сегментной шпонкой
Рисунок 3.65
- Шпоночное соединение
с сегментной шпонкой
Обычно принимают [τ]ср =600—900 кг/см2.
Допускаемые напряжения на смятие принимаются такими же, как для призматических
шпонок.
3.26.2 Шлицевые соединения
Основное применение в коробках передач находят
прямобочные и эвольвентные шлицевые соединения, применяемые как для подвижных,
так и неподвижных посадок. Прямобочные шлицевые соединения стандартизованы трех
серий: легкой, средней й тяжелой. Серии различаются тем, что при одинаковом
внутреннем диаметре другие размеры и число зубьев различны, что дает возможность
подбирать шлицевые валы для разных нагрузок, передаваемых зубьями, но при
одинаковом расчетном внутреннем диаметре. Чаще всего применяются два способа
центрирования: по внутреннему диаметру d и наружному диаметру D (рисунок 3.66).
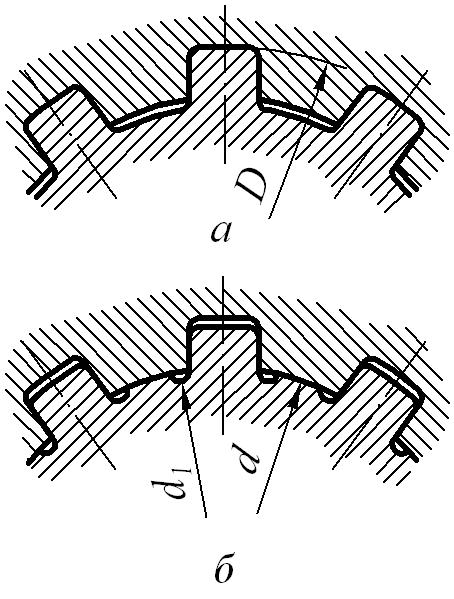
Просмотреть ближе
а –
центрирование по наружному диаметру; б – центрирование по внешнему диаметру
Рисунок
3.66 - Прямобочное шлицевое
соединение
Центрирование по наружному диаметру — наиболее
простой и экономичный способ, поэтому находит широкое применение.
Этот способ центрирования применим в том случае,
когда втулка закаливается до невысокой твердости (НВ<350), такой, при которой
возможно прокалибровать отверстие протяжкой, или остается незакаленной. При
высокой твердости втулки, получаемой при закалке, искажение профиля и размеров
исправить протяжкой нельзя. При центрировании по внутреннему диаметру посадочные
поверхности вала и втулки шлифуются и, кроме того, можно произвести любую
термообработку парных деталей.
Сочетание этих технологических возможностей
обеспечивает высокую точность соединения, большую износостойкость парных
поверхностей, что особенно важно для подвижных соединений, передающих переменные
нагрузки. Прямобочные шлицевые соединения по сравнению со шпоночными обладают
рядом достоинств: лучшее центрирование и направление деталей при перемещении их
вдоль вала, меньшие напряжения смятия на рабочих поверхностях зубьев, большая
динамическая и усталостная прочность валов.
Находят также применение эвольвентные шлицевые
соединения с центрированием по наружному диаметру D боковым граням, причем
первый способ находит более широкое применение.
Эвольвентные шлицевые соединения по сравнению с
прямобочными обладают рядом достоинств: образование зубьев и отделочная
обработка рабочих поверхностей производятся посредством хорошо разработанных
методов обкатки, обеспечивается более точное центрирование и способность
самоустановки под нагрузкой, большая износостойкость в подвижных соединениях,
увеличенная прочность зуба у основания, почти вдвое меньший эффективный
коэффициент концентрации напряжений у основания зуба, что способствует
увеличению усталостной прочности валов, возможность применения в коробках
передач с подвижными косозубыми колесами. Все эти достоинства обеспечивают
широкое перспективное применение эвольвентных шлицевых соединений, особенно для
высокоточных тяжелонагруженных передач. Размеры шлицевого соединения выбираются
по ГОСТ 1139—80 в зависимости от расчетного диаметра вала, а затем производится
проверка на смятие рабочих граней зубьев в предположении, что по поверхности
контакта давления распределяются равномерно, но в передаче крутящего момента
участвует 75 % общего числа зубьев.
Условие прочности
,
где
- окружная сила, действующая на зубья, кгс
(рисунок 3.67);
dср—средний диаметр соединения, см;
Мк—
момент, передаваемый шлицевым соединением, кгс•см ;
z — число зубьев;
— расчетная площадь смятия, одного зуба, см2,
где дополнительно l — длина ступицы детали, насаженной на вал.
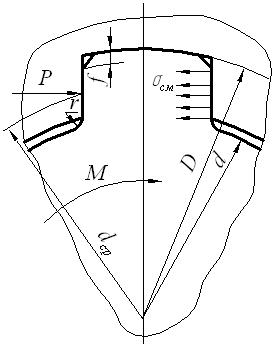
Просмотреть ближе
Рисунок 3.67
- Расчетная схема для прямобочного шлицевого соединения
Для эвольвентного шлицевого соединения
.
Значения [σ]см приведены в таблица
3.61.
Таблица 3.61 - Допускаемые
напряжения смятия [σ]см для шлицевых соединений
Соединения |
Условия эксплуатации |
Термообработка материала |
рабочие поверхности шлицев не подвергнуты специальной термообработке |
рабочие поверхности шлицев подвергнуты специальной термообработке |
Неподвижное |
Тяжелые
Средние
Хорошие |
350—500
600—1000
800—1200 |
400—700
1000—1400
1200—2000 |
Подвижное не под нагрузкой |
Тяжелые
Средние
Хорошие |
150—200
200—300
250—400 |
200—350
300—600
400—700 |
Подвижное под нагрузкой |
Тяжелые
Средние
Хорошие |
— |
30—100
50—150
100—200 |
|
В подвижном шлицевом соединении применяется
смазка, поэтому [σ]см значительно понижается с целью предотвращения выдавливания
смазки и ускоренного износа.
|