7.1.2 Расчет
передач
7.1.2.1
Определение мощностей и передаваемых крутящих моментов на валах
Мощности на валах:
кВт;
кВт;
кВт;
кВт.
Передаваемые крутящие моменты на валах:
;
 ;
 ;
 ;
 ;
 ;
.
Результаты расчетов сводим в таблицу 7.2.
Таблица 7.2
Номер вала (рисунок 7.3) |
Частота вращения валов, об/мин |
Передаваемая мощность, кВт |
Передаваемые крутящие моменты МК кгс·см |
I |
2910 |
11,5 |
384 |
II |
 |
11,05 |
 |
III |

 |
10,6 |

 |
|
7.1.2.2
Расчет цепной передачи
Исходные данные: мощность на валу ведущей звездочки
NIII
= 10,6 кВт, передаточное число передачи
uц.п
= 1,78, предельные частоты вращения
ведущей звездочки (рисунок
7.3) nImax
=795 об/мин,
nImin
=563 об/мин, межосевая линия наклонена к
горизонту под углом α=45°, натяжение цепи осуществляется нажимным роликом,
смазка периодическая, передаваемая нагрузка спокойная, работа односменная,
межосевое расстояние не должно превышать 750 мм.
По
таблице 3.49 принимаем число зубьев малой звездочки
z1=31
в зависимости от передаточного числа, тогда число зубьев ведомой звездочки
z2=z1·uц.п=31
· 1,78=55.
Находим коэффициент
kЭ,
учитывающий условия эксплуатации. По данным
п. 3.23 принимаем:
kдин=1;
коэффициент kA
предварительно принимаем равным 1 по той
причине, что шаг цепи пока неизвестен, а поэтому нельзя определить межосевое
расстояние, зависящее от шага цепи;
kH=1,
так как α<60°,
kper=l,l;
kсм
= 1,5; kреж=1,25,
kЭ
= kдин
kA
kH
kper
kсм
kреж
= 1·1·1·1,1·1,5·1,25 = 1,65. Среднее
значение допускаемого давления в шарнирах [р]0
принимаем по данным
таблицы 3.51 в зависимости от меньшего числа оборотов
n1min=563
об/мин малой звездочки:
.
Определяем ориентировочное значение шага цепи,
принимая число рядов цепи m=1,
мм.
Так как для расчетов принято [р]0
средним и предварительно коэффициент
kA
= 1, то вычисленное значение шага можно
оценивать как предварительное.
Для определения оптимального значения шага зададимся
двумя смежными шагами цепи типа ПР по ГОСТ 13568—97 и расчеты сведем в таблицу
7.3.
Таблица
7.3
-
Определяемые величины и расчетные
уравнения
|
-
Шаг цепи, мм
|
-
Примечания
|
-
19,05
|
-
25,4
|
-
Разрушающая нагрузка
Q,
кг
|
-
2500
|
-
5000
|
-
|
-
Ширина внутреннего звена В, мм
|
-
17,75
|
-
22,61
|
-
|
-
Диаметр валика, мм
|
-
5,96
|
-
7,95
|
-
|
-
Сила тяжести одного погонного метра цепи
q,
кг/м
|
-
1,52
|
-
2,57
|
-
|
-
Проекция опорной поверхности шарнира
F
= bd,
мм2
|
-
105,8
|
-
180
|
-
|
-
Средняя скорость цепи
-
м/с
|
-
υmax
|
-
7,8
|
-
10,4
|
-
υmin
|
-
5,53
|
-
7,4
|
|
-
Число звеньев цепи или длина цепи, выраженная в шагах,
-
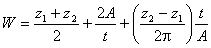
|
-
122
|
-
102
|
-
|
-
Допустимая частота вращения меньшей звездочки по
таблице 3.48,
об/мин
|
-
1550
|
-
1300
|
-
Условие n1max
≤ [n]
соблюдается
|
-
Число ударов цепи, с
-

|
-
6,75
|
-
8,05
|
-
|
-
Допускаемое число ударов по
таблице 3.54
|
-
18
|
-
15
|
-
|
-
Полезное рабочее усилие
-
кг
|
-
195
|
-
146
|
-
|
-
Уточняем коэффициент
kА
, для чего определяем
межосевое расстояние, выраженное в шагах
|
-
39t
|
-
29,5t
|
-
|
-
Значение kA
можно
принять
|
-
1
|
-
1
|
-
|
-
Таким образом, значение
kЭ
остается без изменений
|
-
1,65
|
-
1,65
|
-
|
-
Давление в шарнирах цепи
|
-
2,2
|
-
0,95
|
-
по
υmax
|
-

|
-
3,04
|
-
1,34
|
-
по
υmin
|
-
Допускаемое значение [р]0 по
таблице 3.51.
|
-
2,1
|
-
2,1
|
-
по
υmax
|
-
Цепь шага
t
= 19,05 непригодна, так как
p
> [р]0
|
-
2,35
|
-
2,35
|
-
по
υmin
|
-
Натяжение цепи от центробежных сил
|
-
–
|
-
28,3
|
-
по
υmax
|
-

|
-
–
|
-
14,35
|
-
по
υmin
|
-
Натяжение от провисания цепи
-

|
-
–
|
-
3,8
|
-
kf
= 2
-
(по таблице 3.52)
|
-
Расчетный коэффициент запаса прочности
|
-
–
|
-
36,8
|
-
по
υmax
|
-
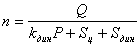
|
-
–
|
-
30,5
|
-
по
υmin
|
-
Допустимое значение [n]
по
таблице 3.55
|
-
–
|
-
10,3
-
11,7
|
-
|
|
Условие
n
≥ [n]
выполнено. Принимаем роликовую однорядную цепь
типа ПР-25,4—5000 ГОСТ 13568—97.
Определим параметры профиля зубьев звездочки (рисунок
7.4, а). Результаты расчетов указаны в таблице 7.4.
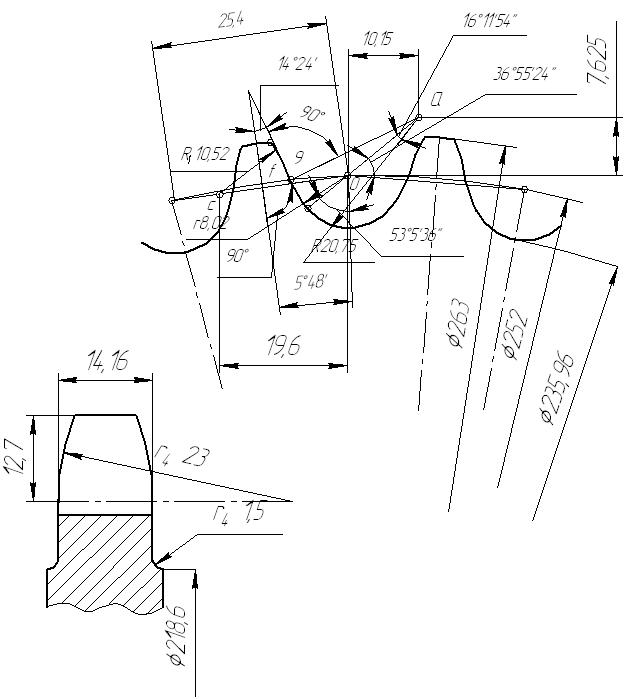
Просмотреть ближе
Рисунок 7.4 - К расчету размеров
звездочки:
а — профиль зубьев звездочки;
б — диаметральное сечение зубчатого венца
Таблица 7.4
Наименование параметров |
Обозначение |
Расчетные уравнения |
Результаты расчетов |
Шаг
цепи |
t |
ГОСТ 13568—97 |
25,4 |
Диаметр ролика |
D |
15,88 |
Число зубьев звездочки |
z1 |
31 |
Диаметр делительной окружности |
dд |
 |
252 |
Диаметр окружности выступов |
De |
 |
263 |
Радиус впадин зуба |
r |
мм |
8,02 |
Диаметр окружности впадин |
Di |
 |
235,96 |
Радиус вогнутости зуба |
R |
 |
20,75 |
Угол соединения |
β |
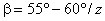 |
53° 5’36’’ |
Угол вогнутости |
γ |
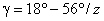 |
16°11’54’’ |
Угол профиля |
φ |
 |
14°24’ |
Прямой участок профиля |
fд |
 |
1,35 |
Расстояние от центра дуги впадины до центра дуги головки зуба |
OC |
 |
19,6 |
Радиус головки зуба |
R1 |
 |
10,52 |
Угол наклона радиуса вогнутости |
ψ |
 |
36°
55’24’’ |
Координаты точки С |
F
V |
 |
19,6
1,99 |
Координаты точки а |
|
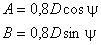 |
10,15
7,625 |
|
В связи с тем что число зубьев звездочки нечетное,
вычисляем наибольшую хорду, необходимую для контроля звездочек:
мм.
Определяем размеры ведущей звездочки в диаметральном
сечении (рисунок
7.4, б). Результаты расчетов указаны в таблице
7.5.
Таблица
7.5
Наименование параметров |
Обозначение |
Расчетные уравнения |
Результаты расчетов, мм |
Диаметр ролика для роликовой цепи |
D |
ГОСТ
13568—97 |
15,88 |
Ширина внутренней
пластины |
b |
24,13 |
Расстояние между внутренними пластинами |
Bвн |
15,88 |
Радиус закругления зуба |
r3 |
 |
23 |
Расстояние от вершины зуба до линии центров дуг закруглений |
h |
 |
12,7 |
Диаметр обода (наибольший) |
Dc |
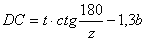 |
218,6 |
Радиус закругления у основания зуба |
r4 |
при
t
≤ 35 |
1,5 |
Ширина зуба однорядной звездочки |
b1 |
 |
14,16 |
|
7.1.2.3
Расчет зубчатых передач
1. Построение графика нагрузки и определение
эквивалентного числа циклов нагружения. Наиболее нагруженной парой колес в
коробке является пара z7—z3,
для которой передаточное число имеет наибольшее значение (u4=2,24),
а частота вращения колеса наименьшую величину
n.3=563
об/мин. Строим условный график нагрузки (рисунок 3.1) для того случая,
когда в зацеплении находятся колеса
z1—z4
и z3—z7
(рисунок
7.5). На графике изображена пиковая
нагрузка, значительно превышающая номинальную. Ввиду кратковременности действия
этой нагрузки при расчете зубчатых колес она не учитывается. Полагаем, что пара
колес z3—z7
работает наиболее длительное время — 5 часов в смену.
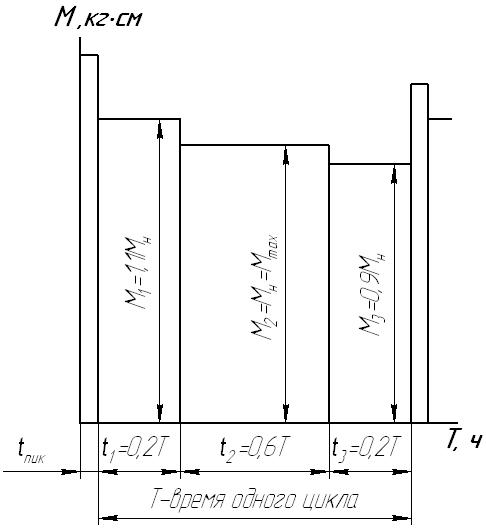
Рисунок 7.5 - График нагрузки
Принимаем число рабочих дней в году — 250, число
смен — 1, срок службы до капитального ремонта — 4 года. Тогда номинальное число
часов работы за указанный срок службы будет:
T=250·5·1·4=5000 ч.
Продолжительность действия
отдельных моментов за срок службы коробки
при М1 = 1,1 МH;
t1
= 0,2 Т = 0,2·5000 = 1000 часов;
при М2 = МH;
t2
= 0,6 Т = 0,6·5000 = 3000 часов;
при М3 = 0,9 МH;
t3
= 0,2 Т = 0,2·5000 = 1000 часов.
Эквивалентное число циклов нагружения зубьев колеса
z7
за срок службы коробки:
.
Показатель степени т при расчете по контактным
напряжениям принимается равным 3. Для данного случая
nMmax
= nз=563
об/мин, так как зубчатое колесо воспринимает переменную нагрузку при постоянном
числе оборотов.
За наибольший длительно действующий момент принимаем
М2= МH=Мтax.
Таким образом,

Эквивалентное число циклов при расчете на выносливость
по изгибным напряжениям определяется по тому же уравнению, но принимается
показатель степени m=6.

2. Выбор материалов колес. По
таблице 3.2 рекомендуемых сочетаний материалов для зубчатых колес и шестерен принимаем: для
шестерен z1,
z2,
z3, z6
сталь марки 40Х улучшенную с механическими
характеристиками, по
таблице 3.3 (при диаметре заготовки до 280 мм и толщине до
90 мм): σв =9000—10000 кг/см2, σТ =8000 кг/см2,
твердость серцевины НВ=250—280. Для колес
z7—z8,
а также для блока колес z4
и
z5
— сталь 50 нормализованную с механическими характеристиками (таблице 3.3): σв=5600—6200
кг/см2, σT
=3200 кг/см2, твердость НВ =
210—230.
Таким образом, выбранные материалы и термообработка их
удовлетворяют желательному соотношению НВ шестерни = НВ колеса + (25÷50). Для
блока зубчатых колес выбрана сталь 50 нормализованная, что позволяет производить
окончательную обработку зубьев лезвийным режущим инструментом. Если применить
марки сталей с термообработкой до НВ>350, то для окончательной обработки зубьев
потребуется применение дорогостоящих операций шлифования или притирки зубьев,
что может оказаться целесообразным лишь в определенных случаях.
3. Определение допустимых напряжений. Коэффициент
режима нагрузки при расчете по контактным напряжениям:
.
Так как
Nц.эк>N0,
то
kрк<1,
поэтому принимаем kрк=1.
Допускаемые контактные напряжения определяются по уравнению [σ]к =
(28÷30) HBmin
kрк
(для нормализованных и улучшенных сталей
при НВ<350).
Для шестерни [σ]к =28·250=7000 кг/см2.
Для колеса [σ]к =28·210 = 880 кг/см2.
В данном случае расчет на контактную прочность
производится по колесу, так как [σ]к.кол < [σ]к.шест,
хотя возможны случаи, когда [σ]к.кол > [σ]к.шест
.
Коэффициент режима нагрузки при расчете по изгибным
напряжениям для улучшенных и нормализованных сталей при НВ<350
.
Так как Nц.эк>N0,
то
kри<1,
поэтому принимаем kри=1.
Коэффициенты режима нагрузки kрк
и kри,
отражающие влияние числа циклов на выносливость зубьев по изгибным и контактным
напряжениям, для всех других более быстроходных колес коробки окажутся меньшими.
Поэтому расчет всех передач производится при коэффициентах режима
kрк
= 1 и kри
= 1. Допускаемые напряжения изгиба при работе одной стороной зуба (по условию на
проектирование передачи нереверсивные) определены по следующим данным:
коэффициент безопасности для нормализованных и улучшенных колес [n]=1,5, эффективный коэффициент концентрации напряжений на
переходной поверхности kσ
= 1,8.
Предел выносливости сердцевины для материалов колес
при симметричном цикле

Для шестерни
σ-1
= 0,24 · 9500+ 600 = 2880 кг/см2.
Для колеса
σ-1
= 0,24 · 6000 + 600 = 2040 кг/см2.
Допускаемые напряжения изгиба:
Для шестерни
.
Для колеса
.
4. Определение коэффициента нагрузки. Для
предварительных расчетов принимаем
k
= 1,5.
5. Определение коэффициента ширины венца колес ψа.
Принимаем ψа =0,15 для колес, включаемых осевым перемещением, и ψа
=0,18 для колес, находящихся в постоянном зацеплении.
6. Определение делительных межосевых расстояний для
наиболее тяжелонагруженных пар колес, для которых передаточное число
наибольшее, а число оборотов колеса наименьшее. Такими парами являются
z1—z4
и
z3—z7.
Делительное межосевое расстояние из условий контактной прочности определяется по
уравнению
.
Расчетный модуль
.
По ГОСТ 9563—60 принимаем
m=4
мм. Уточненное делительное межосевое расстояние для первой двухваловой передачи
.
Делительное межосевое расстояние между вторым и
третьим валами
.
Расчетный модуль
.
По тому же стандарту принимаем т = 4,5 мм.
Уточненное делительное межосевое расстояние для второй
двухваловой передачи
.
7. Определение ширины венцов зубчатых колес:

определяем из условия равнопрочности по уравнению:
;

. Принимаем 30 мм.
определяем
по уравнению (34).
.
Принимаем 18 мм.
Для облегчения переключения зубчатые венцы колес
z1, z2,
z4,
z5
выполняются с бочкообразной формой рабочих торцов зубьев.
В результате рабочая длина зуба уменьшается примерно
на величину l=h·tg
15° (рисунок
7.6), где
h
— высота зуба. В данном примере
l=2,25
· 4 · 0,268=2,4 мм.

Рисунок 7.6 - К расчету ширины венцов колес
Поэтому окончательная ширина венцов зубчатых колес
будет
. Принимаем
24 мм.
. Принимаем
18 мм.
8. Определение степени точности колес. Степень
точности зависит от окружной скорости , которую вычисляем для
зубчатых колес, имеющих наибольшую скорость. Такими колесами в первой
двухваловой передаче являются
z2
и
z5.

По
Приложению 19 принимаем 6-ю степень точности для
колес z1,
z2,
z4
и z5.
Во второй двухваловой передаче наибольшую
скорость имеют колеса z6
и
z8.

Принимаем 7-ю степень точности для колес
z7,
z3,
z6,
z8.
9. В наиболее неблагоприятных условиях по концентрации
нагрузки вдоль зуба находятся две пары колес:
z1—z4
и
z3—z7
по следующим причинам: для этих
пар колес отношение
наибольшее, а именно

Таблица
7.6 - Сводная таблица
основных параметров
колес
Число зубьев
колес |
Модуль, мм |
Диаметры, мм |
Ширины зубчатых
венцов, мм |
Отношение
 |
d |
da |
df |
z1
= 22 |
4 |
88 |
96 |
78 |
24 |
0,27 |
z2
=
24 |
4 |
96 |
104 |
86 |
18 |
0,19 |
z3
= 23 |
4,5 |
103,5 |
112,5 |
92,25 |
30 |
0,29 |
z4
= 51 |
4 |
204 |
212 |
194 |
24 |
0,118 |
z5
= 49 |
4 |
196 |
204 |
186 |
18 |
0,092 |
z6
=
27 |
4,5 |
121,5 |
130,5 |
110,25 |
18 |
0,15 |
z7
= 52 |
4,5 |
234 |
243 |
222,75 |
30 |
0,13 |
z8
= 48 |
4,5 |
216 |
225 |
204,75 |
18 |
0,083 |
|
На валу
III
посажено колесо z7,
а на консоли этого вала звездочка. Силы, возникающие в цепном приводе, вызывают
дополнительные деформации вала, что, в свою очередь, увеличивает угол поворота
торцевой плоскости колеса z7,
а поэтому усиливается концентрация нагрузки
вдоль зуба. Указанные пары зубчатых колес расположены несимметрично относительно
опор. Исходя из этих соображений, коэффициенты концентрации нагрузки определим
для передач z1—z4
и z3—z7.
Значение
kкц
принимаем по
таблице 3.14, как для
прирабатывающихся пар колес (твердость зубьев НВ<350).
.
В связи с небольшим колебанием нагрузки принимаем φ =
0,6. По таблице 3.15 принимаем θ=1,3.
Тогда
kкц
= 1,3 (1–0,6) +0,6= 1,12.
Подсчеты, выполненные по данным указанных таблиц,
показывают, что значения kкц
для обеих пар колес одинаковые. Коэффициент динамичности принимаем по
таблице
3.12. Он оказывается одинаковым для всех передач:
kД=1,5.
Уточненное значение коэффициента нагрузки:

10. Проверка зубьев колес на выносливость по
контактным и изгибным напряжениям. В связи с тем что уточненное значение
коэффициента нагрузки отличается от ранее принятого ориентировочного значения
k
=1,5, рабочие напряжения могут оказаться больше допускаемых. Проверка контактных
напряжений производится у зубьев шестерен или колес, хотя контактные напряжения
у зубьев парных колес одинаковы, но более опасными, как правило, они оказываются
у одного из них, и чаще всего у зубьев колес, которые изготавливаются из менее
прочных материалов.
В данном случае в наиболее неблагоприятных условиях
находятся зубчатые колеса z4
и z7
(о чем сказано ниже), прочность которых
проверим по уравнению
.
Колеса
z4:
.
Условие прочности выполнено, так как
σк= 5420 кг/см2 < 5880
кг/см2 = [σ]к.
Колеса z7:
.
Условие прочности также выполнено. Проверка зубьев
шестерен и колес на выносливость по напряжениям изгиба производится по уравнению:

или по аналогичному уравнению
.
Для шестерен и колес 7-й степени точности (z3,
z7,
z6
и
z8)
коэффициенты формы зуба у принимаем по
таблице 3.7, для шестерен и колес
6-й степени точности (z1,
z4,
z2,
z5)
по графику (рисунок 3.21). Для сравнительной оценки изгибной прочности
зубьев шестерен и колес вычислим произведения [σ0]и у.
Результаты вычислений сводим в таблицу 7.7
Таблица
7.7
|
z1 |
z2 |
z3 |
z4 |
z5 |
z6 |
z7 |
z8 |
Число зубьев |
22 |
24 |
23 |
51 |
49 |
27 |
52 |
48 |
у |
0,415 |
0,425 |
0,390 |
0,450 |
0,445 |
0,408 |
0,460 |
0,456 |
у[σ0]и |
664 |
680 |
624 |
508 |
503 |
653 |
520 |
515 |
|
Из сопоставления произведений у[σ0]и
и других величин, входящих в уравнение прочности σи ≤ [σ0]и,
видно, что необходимо проверить изгибную прочность колес или шестерен четырех
пар зацеплений z1
—
z4,
z2—z5,
z3—z7,
z6—z8.
Проверка производится того из колес данной пары, для которого произведение у[σ0]и
окажется меньшим.

Условие изгибной прочности выполняется.
В уравнения прочности входят частоты вращения колес,
каждое из которых в общем случае может вращаться с разными скоростями. В
уравнение следует подставлять наименьшие частоты вращения, принимая их по
графику (рисунок 7.2). Анализ произведений у[σ0]и
показывает, что парные зубчатые колеса не отвечают желательному равенству
произведений у[σ0]и
шестерен и парных им колес, хотя эта разница небольшая. Для уравнивания этих
произведений можно применить нарезание зубьев колес со смещением режущего
инструмента так, чтобы коэффициент суммы смещений хΣ = х1
+ х2 = 0.
|