8.13 Краткое
описание основных узлов и их регулирование
8.13.1 Шпиндельная бабка
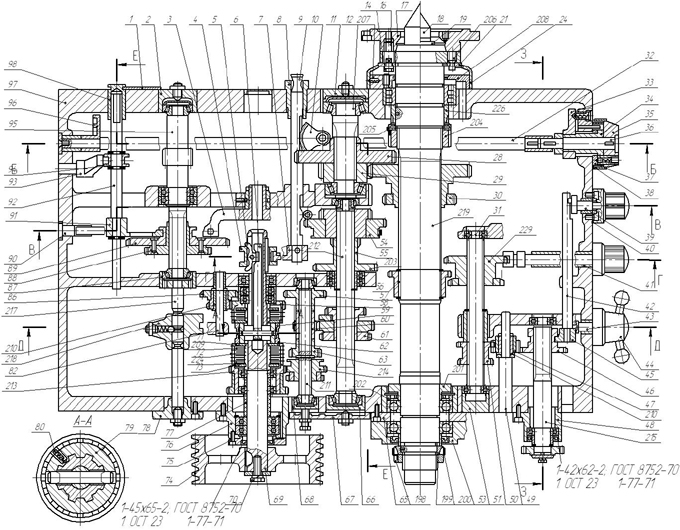
Просмотреть ближе
Рисунок 8.16 - Шпиндельная бабка (развертка)
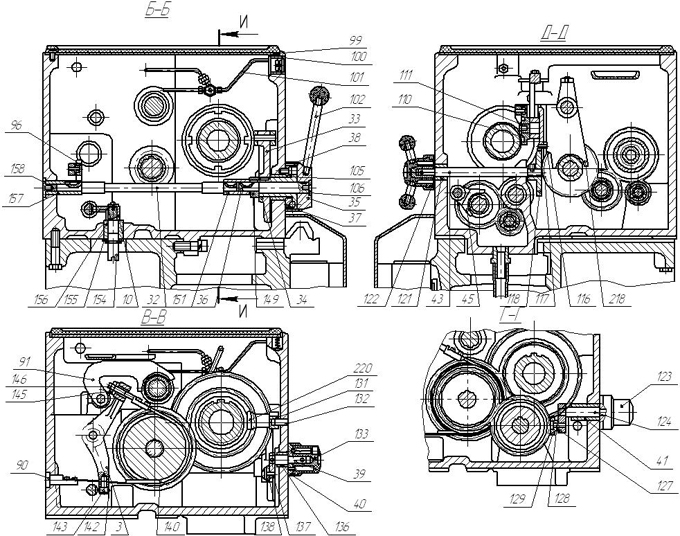
Просмотреть ближе
Рисунок 8.17 - Шпиндельная бабка
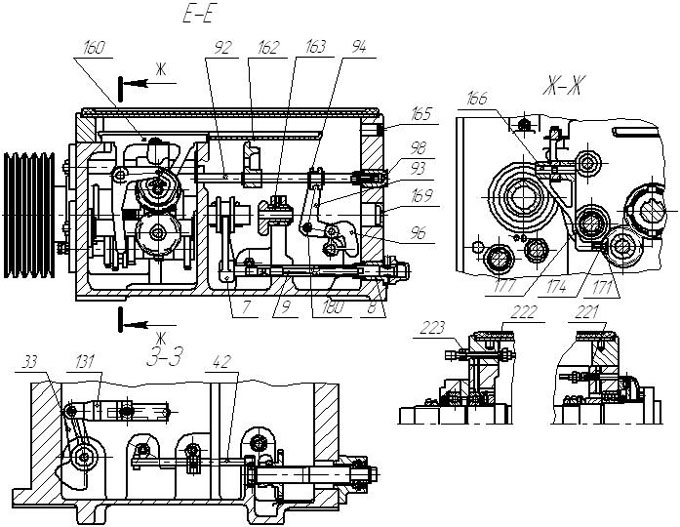
Просмотреть ближе
Рисунок 8.18 - Шпиндельная бабка

Просмотреть ближе
Рисунок 8.19 - Шпиндельная бабка (чертеж шпинделя в
сборе)
8.13.1.1
Шпиндельная бабка жестко сбазирована на станине при сборке станка и не требует
регулирования в процессе эксплуатации.
8.13.1.2 При
ослаблении крепления шкива 74 на конусной части вала 69 нужно
подтянуть винт 70 (рисунок 8.16).
8.13.1.3
Крутящий момент на шпинделе должен соответствовать данным, приведенным в таблице
8.13 (см. раздел 8.12).
При снижении крутящего момента нужно в первую очередь
проверить натяжение ременной передачи главного привода (см. п. 8.13.6). Если
натяжение ремней достаточное, следует отрегулировать фрикционную муфту главного
привода, расположенную в шпиндельной бабке. Для этого надо открыть крышку 99
(рисунок 8.17) шпиндельной бабки и снять маслораспределительный лоток 162.
Поворотом гайки 62 (рисунок 8.16) по часовой стрелке при
утопленной (нажатой) защелке 80 можно подтянуть муфту прямого вращения
шпинделя, поворотом гайки 59 против часовой стрелки — муфту обратного
вращения. Для облегчения регулирования муфты прямого вращения шпинделя рукоятку
8 (рисунок 8.9) нужно повернуть влево, для облегчения регулирования муфты
обратного вращения шпинделя — вправо.
Обычно достаточно повернуть гайки 59 и 62
на 1/12 оборота, т. е. на один зубец. По окончании регулирования нужно
убедиться в том, что защелка 80 надежно вошла в пазы гаек 59 и
62.
При повороте гаек более чем на 1/12 оборота нужно
обязательно проверить, не превышает ли крутящий момент на шпинделе допустимый по
табл. 1 (см. раздел
8.12).
8.13.1.4 Если
при максимальном числе оборотов шпинделя без изделия и патрона время его
торможения превышает 1,5 сек, то нужно при помощи гаек 145
подтянуть ленту тормоза.
8.13.1.5
ВНИМАНИЕ! Шпиндельные подшипники отрегулированы на заводе и не требуют
дополнительного регулирования.
В случае крайней необходимости потребитель может
силами высококвалифицированных специалистов прибегнуть к регулированию
шпиндельных опор.
Однако перед этим необходимо проверить жесткость
шпиндельного узла. Для этого на станине под фланцем шпинделя устанавливается
домкрат с проверенным в лаборатории динамометром и через прокладку,
предохраняющую шпиндель от повреждений, к его фланцу прилагается усилие,
направленное вертикально снизу вверх. Смещение шпинделя контролируется
аттестованным индикатором с ценой деления не более 0,001 мм,
устанавливаемым на шпиндельной бабке и касающимся своим измерительным
наконечником верхней части фланца шпинделя. Отклонение шпинделя на 0,001 мм
должно происходить при приложенном усилии не менее 45—50 кгс. Если
величина нагрузки при смещении на 0,001 мм значительно ниже указанной,
целесообразнее всего обратиться на завод с подробным описанием методики
проверки и указанием измеренных величин, а также сведений о станке,
перечисленных в разделе 1. В каждом отдельном случае будет дана конкретная
консультация или командирован специалист-наладчик.
Примечание -
Станки комплектуются передними шпиндельными подшипниками № 3182120 класса 2
ГОСТ 7634—75 и задними № 46216 класса 4 ГОСТ 831—75 (рисунок 8.16) или передними
подшипниками № 697920Л
(рисунок 8.19). Шпиндельные подшипники заказом не регламентируются.
8.13.2 Задняя бабка

Просмотреть ближе
Рисунок 8.20 - Задняя бабка
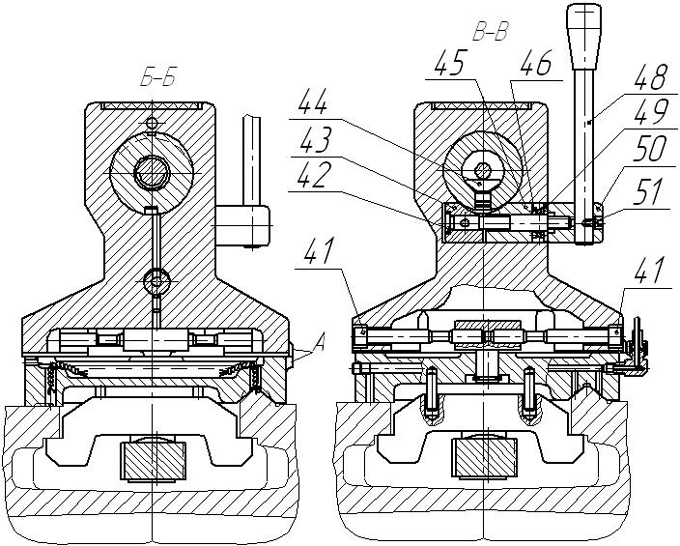
Просмотреть ближе
Рисунок 8.21 - Задняя бабка
8.13.2.1 Если
рукоятка 19, отведенная в крайнее заднее положение, не обеспечивает
достаточный прижим задней бабки к станине, то нужно посредством регулирования
винтами 26 и 33 при отпущенных контргайках 27 и 34,
изменяя положение прижимной планки 31, установить необходимое усилие
прижима.
8.13.2.2 Для
установки задней бабки соосно со шпинделем при помощи винтов 41 совмещают
в одну плоскость поверхности платиков А, расположенных на опорной плите
28 и корпусе 2.
8.13.3 Коробка подач
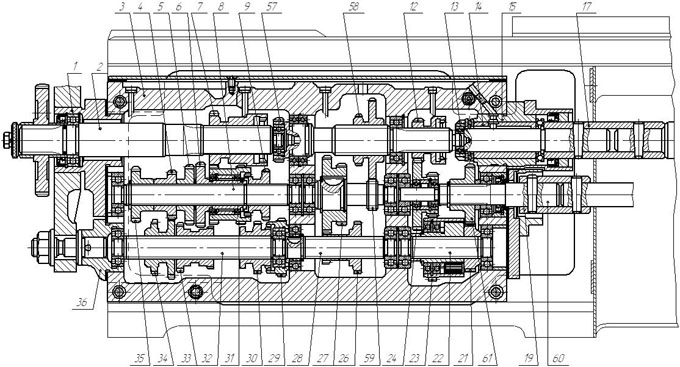
Просмотреть ближе
Рисунок 8.22 - Коробка подач

Просмотреть ближе
Рисунок 8.23 - Коробка подач
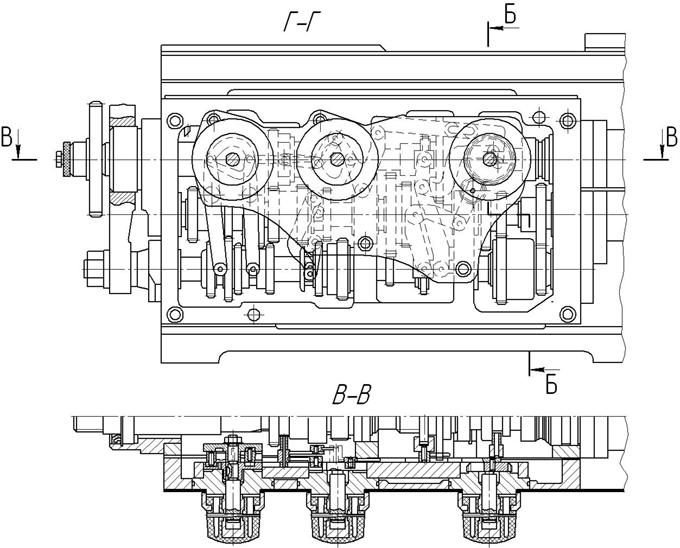
Просмотреть ближе
Рисунок 8.24 - Коробка подач
8.13.3.1 При
ремонте станка особое внимание следует обратить на правильность монтажа
механизма переключения зубчатых колес, смонтированного на плите 37,
которая крепится к корпусу 3 коробки подач. Во избежание нарушения
порядка сцепления зубчатых колес коробки подач при сборке нужно совместить
риски, нанесенные на шестернях 51 и 52.
8.13.4 Фартук
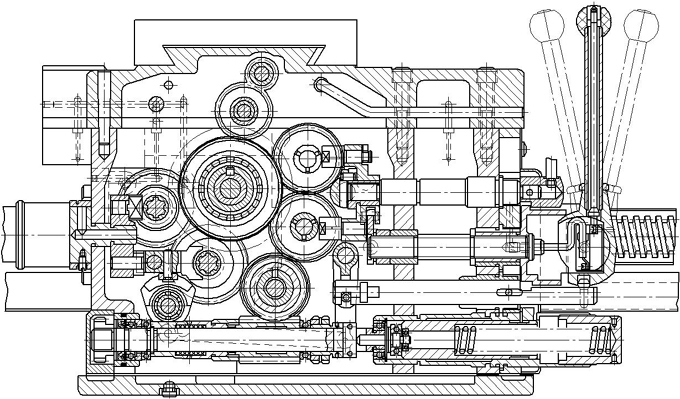
Просмотреть ближе
Рисунок
8.25 - Фартук
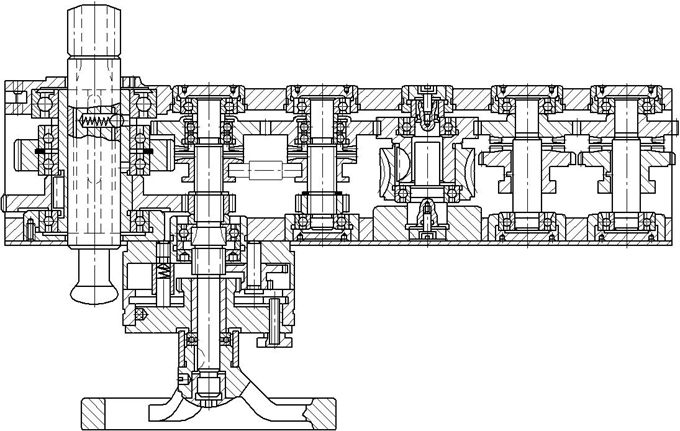
Просмотреть ближе
Рисунок
8.26 - Фартук (развертка)
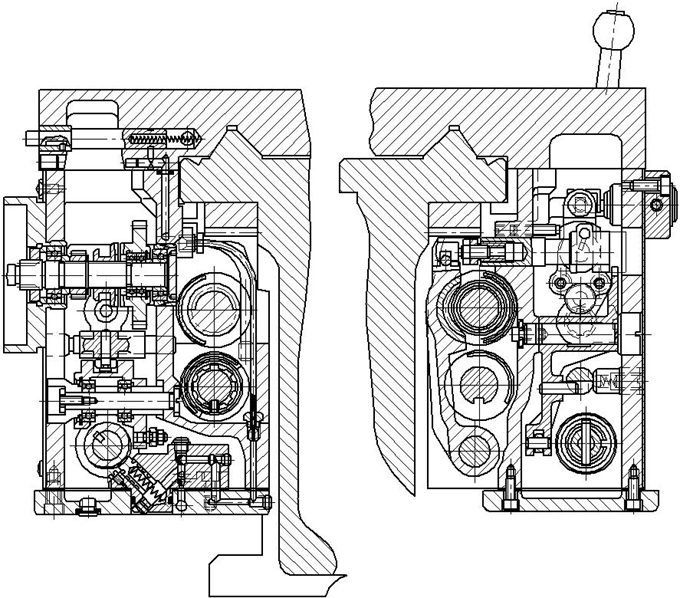
Просмотреть ближе
Рисунок
8.27 - Фартук
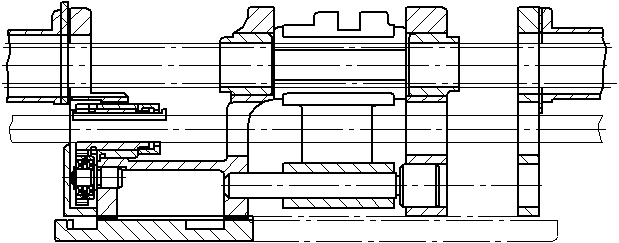
Просмотреть ближе
Рисунок
8.28 - Фартук
8.13.4.1
Регулирование усилия, развиваемого механизмом подач, производится поворотом
гайки 11. Величина усилия определяется динамометром, который нужно
установить между жестким упором 47 (рисунок 8.30) и кареткой 19 (рисунок
8.29). Следует следить за тем, чтобы величина усилия не превышала допустимую по
таблице 8.13 (раздел 8.19).
8.13.4.2
Маточная гайка 62, установленная на кронштейне 61, отрегулирована
на заводе.
В случае необходимости восстановления или замены
изношенной гайки при ремонте нужно воспользоваться специальными кондукторным
приспособлением и метчиком, чертежи на которые могут быть высланы по запросу.
8.13.5 Суппорт
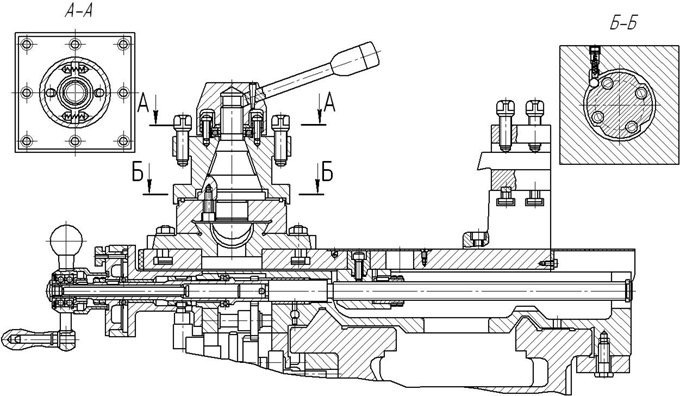
Просмотреть ближе
Рисунок 8.29 - Суппорт
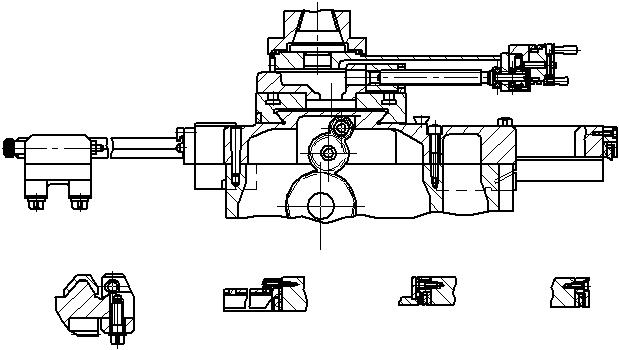
Просмотреть ближе
Рисунок 8.30 - Суппорт
8.13.5.1
Мертвый ход винта 20 привода поперечных салазок 11, возникающий
при износе гаек 22 и 23, устраняется следующим образом.
Снимается крышка 12 и при помощи выколотки
(бородка) из мягкого металла отворачивается контргайка 15. Выборка зазора
в винтовой паре осуществляется вращением гайки 14. Величина зазора
определяется по лимбу 40 при легком поворачивании рукоятки 33.
Оптимальная величина зазора в винтовой паре соответствует свободному ходу в
пределах, одного деления лимба. Затем контргайка 15 затягивается и
устанавливается крышка 12.
8.13.5.2
Поставляемый по особому заказу задний резцедержатель 8 устанавливается на
поперечных салазках, как это показано на рисунок 8.29.
8.13.5.3 Если
по мере износа рукоятка 4 в зажатом положении останавливается в неудобном
для токаря месте, то посредством подшлифовывания или замены проставочного кольца
1 можно установить рукоятку 4 в требуемое положение.
8.13.5.4 При
понижении точности фиксации резцедержателя 43 нужно разобрать резцовую
головку и произвести тщательную очистку рабочих поверхностей сопрягаемых
деталей.
8.13.5.5
Установка оптимального зазора между кареткой 19 и планками 18, 64
и 66 осуществляется путем шлифования последних.
Выборка зазора в направляющих поперечных салазок
11 и резцовых салазок 9 производится подтягиванием соответствующих
клиньев 52 и 42 при помощи винтов, головки которых расположены в
отверстиях протекторов 41 и 49.
8.13.5.6 Для
удобства определения величин перемещения резцовых и поперечных салазок при
обработке деталей суппорт снабжен масштабными линейками.
На резцовых салазках 9 установлена линейка с
ценой деления 1 мм.
Отсчет производится по визиру, закрепленному па
поворотной части 10 суппорта.
На каретке 19 установлена линейка с ценой
деления 10 мм на диаметр изделия, по которой осуществляется контроль
величины перемещения поперечных салазок 11 при помощи закрепленного на
них визира.
Конструкция линейки, закрепленной на каретке,
предусматривает установку жесткого упора поперечных перемещений, поставляемого
по особому заказу.
Жесткий микрометрический упор 47 ограничения
продольных перемещений крепится на передней полке станины двумя винтами 82.
8.13.5.7
Станок 16К20П комплектуется суппортом с механическим приводом резцовых салазок
(рисунок 8.31, 8.32), который также по особому заказу может быть поставлен со станком
16К.20. Включение механического перемещения резцовых салазок 9
осуществляется вытягиванием на себя кнопки 122 при зажатой рукоятке
129. Величина подачи резцовых салазок равна 1/4 величины продольной подачи
суппорта.
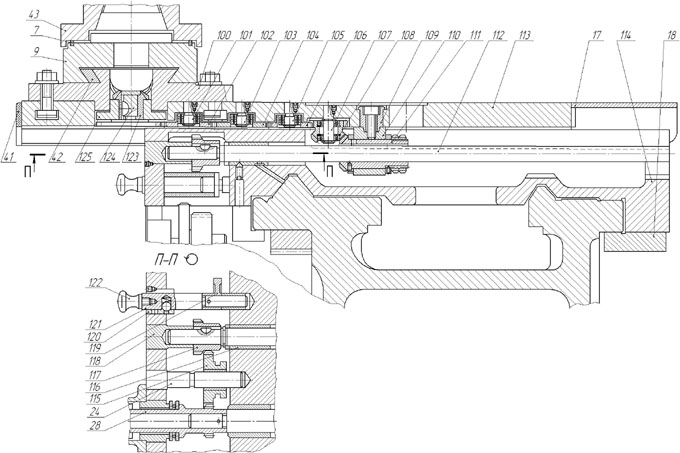
Просмотреть ближе
Рисунок 8.31- Суппорт с механическим приводом
резцовых салазок
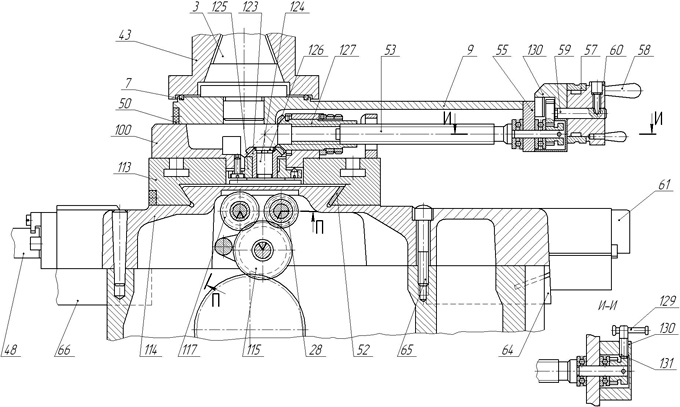
Просмотреть ближе
Рисунок 8.32- Суппорт с механическим приводом
резцовых салазок
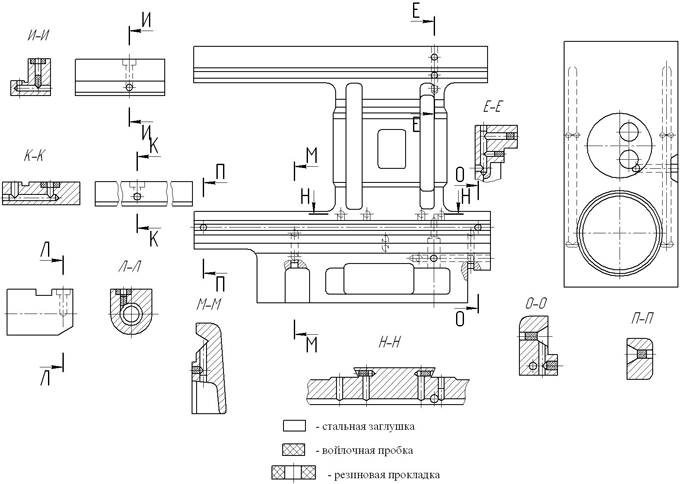
Просмотреть ближе
Рисунок 8.33 - Схема расположения заглушек, пробок
и прокладок в каретке
Примечание
-
Номерами, начинающимися со 100, обозначения детали, относящиеся только к
суппорту с механическим приводом резцовых салазок. Числами меньше 100 — детали,
унифицированные от суппорта с ручным перемещением резцовых салазок (рисунок 8.29,
8.30).
8.13.5.8
Представленная на рисунке 8.33 схема служит для правильной установки заглушек, пробок
и прокладок системы смазки в каретку при ремонте станка.
8.13.6 Моторная установка
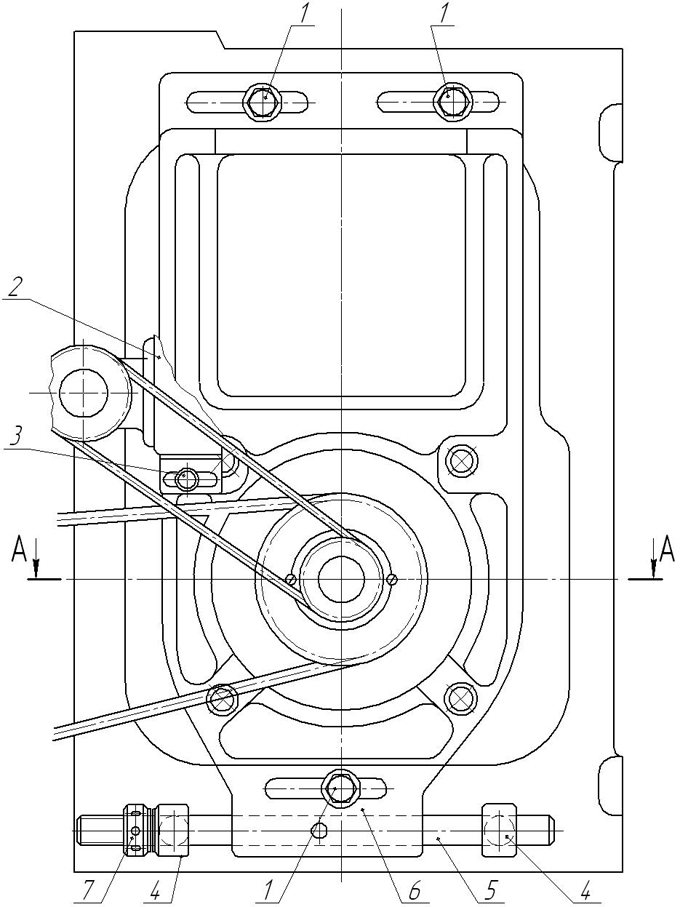
Просмотреть ближе
Рисунок 8.34 - Моторная установка
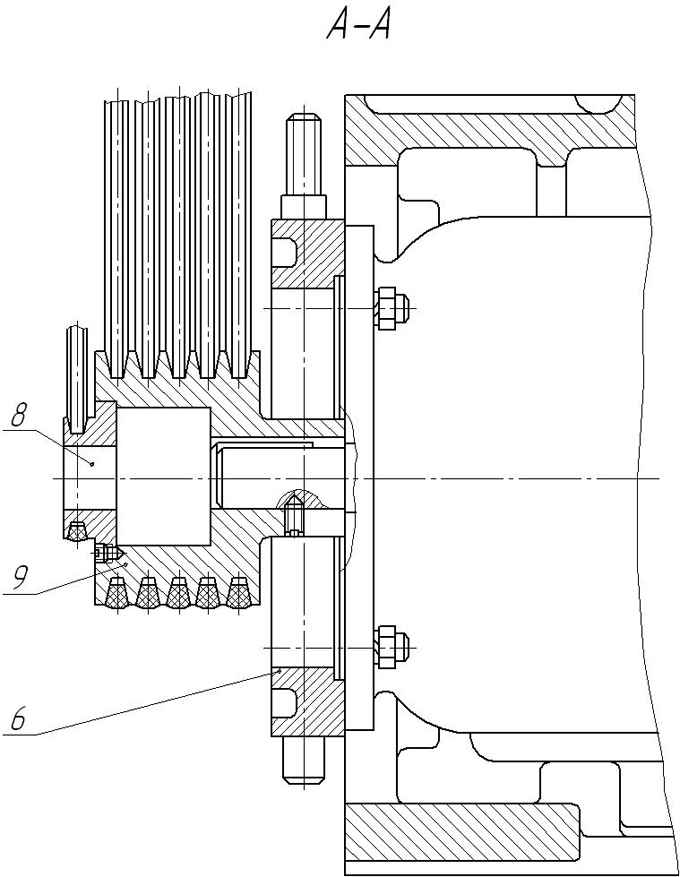
Просмотреть ближе
Рисунок 8.35 - Моторная установка
8.13.6.1 При
уменьшении крутящего момента на шпинделе (см. таблица
8.13, п. 12.1.1.) в первую
очереди следует проверить натяжение ремней главного привода. Если ремни
недостаточно натянуты, то нужно ослабив винты 1, плавным вращением гайки
1 против часовой стрелки опустить вниз подмоторную плиту 6 до требуемого
натяжения ремней, после чего винты 1 завернуть до отказа.
8.13.6.2
Натяжение ремня привода насоса системы смазки осуществляется поднятием бака
2, для чего нужно отпустить три винта 3 (на чертеже показан один),
при помощи которых бак крепится к подмоторной плите 6.
8.13.7 Механизм управления фрикционной муфтой главного привода
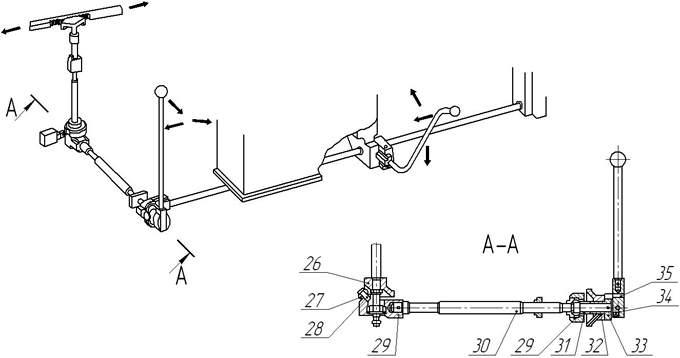
Просмотреть ближе
Рисунок
8.36 - Механизм управления фрикционной муфтой главного привода
8.13.7.1
Конструкция механизма исключает возможность включения или выключения фрикционной
муфты при случайном нажатии на рукоятки 12 и 24, которые
сблокированы между собой следующий образом.
При работе рукояткой 12 рукоятка 24
повторяв операции первой. Выключение возможно любой из рукояток. Если же муфта
была включена рукояткой 24, то выключение можно произвести и рукояткой
12 только при условии предварительного поворота этой рукоятки в
соответствующее рабочее положение с последующим возвращением в нейтральное
(среднее) положение для выключения.
8.13.8 Коробка передач (сменные шестерни)
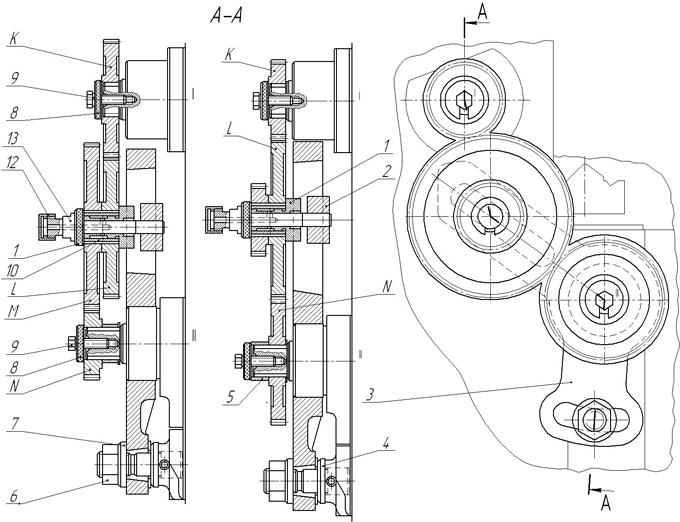
Просмотреть ближе
Рисунок
8.37 - Коробка передач (сменные шестерни)
8.13.8.1
Коробка передач (сменные шестерни) служит для передачи вращения от выходного
вала (ось /) шпиндельной бабки на выходной вал (ось //) коробки подач с помощью
установки комбинаций сменных шестерен в соответствии со схемами таблицы (рисунок
8.11
и 8.12). Станок можно налаживать на нарезание различных резьб.
Сменные шестерни К и
N
монтируются на шлицевых валах и закрепляются болтами 9 через шайбы 5.
Промежуточные шестерни
L
и М устанавливаются на шлицевой втулке 10 оси 13,
закрепляемой при помощи ключа в требуемом месте паза кронштейна 3,
который фиксируется гайкой 6.
8.13.8.2 На
торцах сменных шестерен К,
L, М,
N нанесены условные обозначения деталей
(см. упаковочный лист), число зубьев
z
и модуль т.
8.13.8.3 При
закреплении кронштейна 3 и оси 13 нужно установить сменные
шестерни с минимальным радиальным зазором.
Нельзя забывать о регулярной смазке (см. п.
8.8.6.2.
«Карта смазки») сменных шестерен и втулки 10, которая смазывается через
колпачковую масленку 12.
8.13.9 Станина, рейки, ходовой винт, ходовой вал и привод быстрых перемещений
суппорта
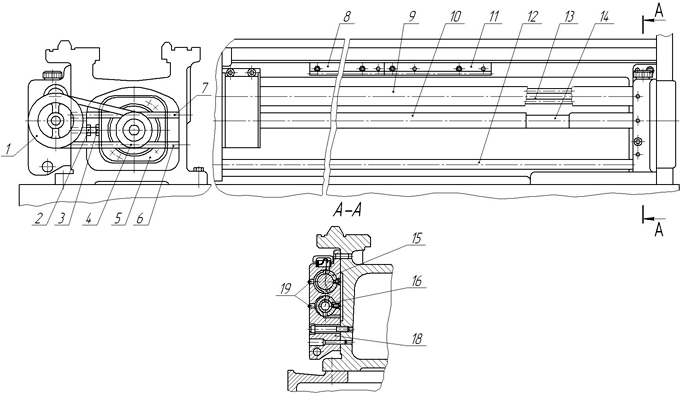
Просмотреть ближе
Рисунок 8.38 - Станины, рейки, ходовой вал, привод быстрых перемещений суппорта
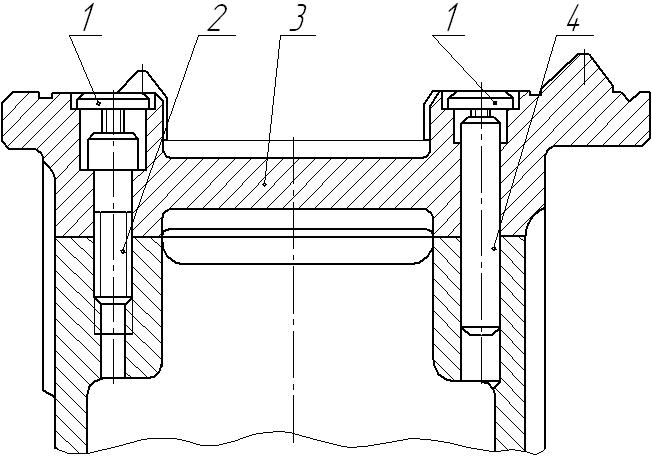
Просмотреть ближе
Рисунок 8.39 - Чертеж установки
мостика на станину
8.13.9.1
Натяжение ремня привода быстрых перемещений суппорта осуществляется
регулировочным винтом 3, который контрится гайкой 2.
8.13.9.2 При
чистке ходового винта 13 и ходового вала 14 необходимо снять щитки
9 и 10. Для этого нужно отпустить винты 19 и вынуть щитки
со стороны заднего кронштейна 18.
8.13.9.3 Еще
раз обращаем внимание на необходимость указания наибольшей длины обрабатываемого
изделия L
при заказе запасных частей. Для заказа
реек следует руководствоваться таблицей:
L |
710 |
1000 |
1400 |
2000 |
Номер
рейки |
8 |
8 |
11 |
8 |
8 |
Количество |
1 |
1 |
1 |
2 |
3 |
|
8.13.9.4
Установка и снятие мостика (рисунок 8.39). Станок 16К20Г поставляется с установленным
на станине мостиком 3. При необходимости обработки деталей большого
диаметра над выемкой в станине мостик снимается. Для этого нужно вывернуть
пробки 1, удалить винты 2 и штифты 4.
Во избежание нанесения забоин мостик положить на
подкладку из мягкого материала и для предотвращения коррозии покрыть тонким
слоем масла.
Перед установкой мостика на станину следует очень
тщательно протереть посадочные поверхности станины и мостика и убедиться в
отсутствии забоин.
8.13.9.5
Следует знать, что при обработке деталей над выемкой на планшайбе диаметром 500
мм (1911/16") число оборотов шпинделя не должно
превышать 400 об/мин. При обработке несбалансированных изделий число
оборотов должно быть снижено.
8.13.10 Держатель центрового инструмента
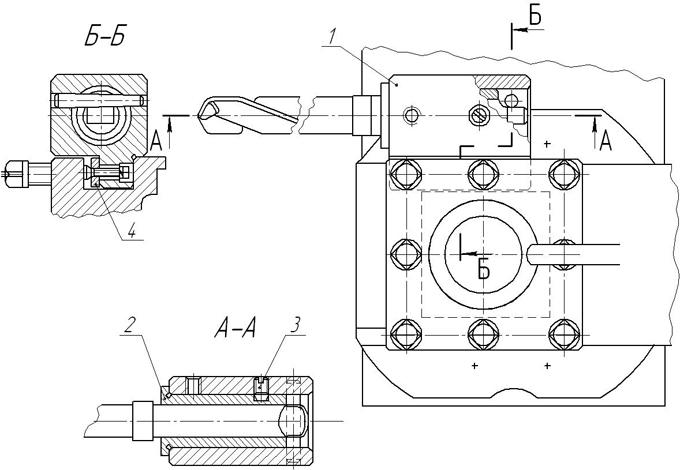
Просмотреть ближе
Рисунок 8.40
- Держатель центрового инструмента
8.13.10.1 В
руководстве под определением «центровой инструмент» понимается режущий
инструмент для обработки отверстий, ось которых совпадает с осью шпинделя
(например, сверла, зенкеры, развертки и т. п.).
8.13.10.2
Держатель центрового инструмента применяется при обработке отверстий с ручной и
механической подачей каретки.
Держатель 1 устанавливают в позицию
резцедержателя, маркированную символом, обозначающим сверло, до упора в его
боковую грань и зажимают винтами.
В цилиндрическое отверстие держателя вставляется
втулка 2 с коническим отверстием для инструмента и стопорится винтом
3.
8.13.10.3
Совмещение оси режущего инструмента с осью шпинделя осуществляется перемещением
поперечных салазок суппорта до совпадения визира с риской на каретке,
обозначенной символом, идентичным нанесенному на резцедержателе. Причем визир
должен быть вдвинут в кронштейн до упора.
Коррекция положения оси режущего инструмента
производится рукояткой перемещения поперечных салазок.
8.13.11 Резцовая оправка для обработки деталей
над выемкой в станине
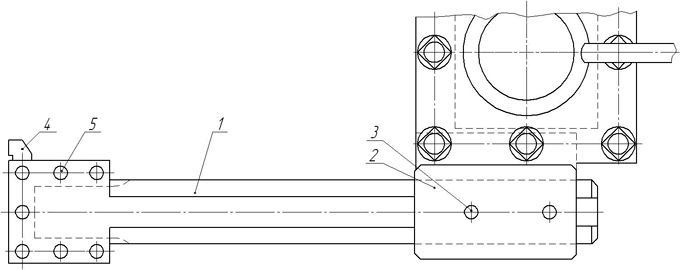
Просмотреть ближе
Рисунок 8.41 - Резцовая
оправка для обработки деталей над выемкой
8.13.11.1
Станок 16К20Г комплектуется специальной резцовой оправкой для обработки деталей
над выемкой в станине, предотвращающей свисание каретки с направляющих станины.
8.13.11.2
Оправка 1 устанавливается в держателе 2, как это показано на
рисунок 8.41. Резец 4 крепится винтами 5.
8.13.11.3
Обработка с использованием оправки должна производиться на минимальных режимах.
|