6.3 Выбор баз
для простановки размеров
Для практических целей вполне достаточно все
размеры классифицировать на две группы: основные, или сопряженные, и свободные.
Основными, или сопряженными, называются размеры,
которые входят в размерные цепи и определяют относительное положение деталей в
собранном изделии.
Основные размеры обеспечивают:
а) точность работы детали в механизме;
б) строгое расположение детали в механизме;
в) нормальную сборку и разборку;
г) требуемую взаимозаменяемость.
Из сказанного следует, что к группе основных
размеров относятся важнейшие конструктивные размеры, влияющие на
работоспособность, точность и взаимозаменяемость изделия. Эти размеры обычно
выполняются с относительно высокой точностью (5–11-й квалитет).
Свободными называются размеры, которые в
размерные цепи деталей или изделия не входят. Эти размеры координируют такие
поверхности детали, которые не соединяются с поверхностями других деталей.
Поэтому свободные размеры не влияют на характер и точность сопряжения деталей, а
обеспечивают:
а) механические, физические и другие свойства
детали;
б) технологические требования (размеры канавок,
проточек, уступов, приливов и т. д.);
в) архитектурные, декоративные и весовые
показатели;
г) удобство эксплуатации, сборки и разборки.
На свободные размеры обычно задаются допуски по
12—16-му квалитетам. На рисунке 6.1 показаны некоторые сопряженные и свободные
размеры. При выполнении чертежей эти размеры можно нанести различным образом.
Однако для выбора наилучшего варианта нанесения размеров дать единого правила,
действительного во всех случаях, нельзя, так как при одинаковой форме деталей
может оказаться целесообразным различное нанесение размеров в зависимости от
размерной базы детали. Под этой базой понимают поверхности, линии или точки,
относительно которых размером задано положение других поверхностей, линий и
точек этой детали. Чаще всего за базы принимаются:
а) плоскости, от которых ведется отсчет размеров
и обычно начинается обработка детали;
б) линии — оси симметрии и прямые линии кромок
детали, которые могут являться осями координат для отсчета размеров до отдельных
элементов детали;

Просмотреть ближе
(О — основной, С — свободный)
Рисунок 6.1 - Примеры классификации размеров
в) точка и ось. Точка — полюс системы полярных
координат; ось — база для отсчетов углов.
Базы имеют важное значение для координирования
взаимного положения отдельных элементов детали, особенно тех ее частей, которые
предназначены для присоединения к ней других деталей. Общая классификация баз
может быть представлена в виде следующей схемы.
Конструктивная база — база, относительно которой
координируется положение деталей в собранном изделии.
Технологическая база — база, при помощи которой
обрабатываемая поверхность ориентируется на станке или в специальных
приспособлениях.
Основная база — та поверхность, которая
определяет положение детали в изделии.
Вспомогательная база — определяет положение
деталей, присоединяемых к данной детали.
Скрытая база — база, которая на детали
существует в неявном виде. К этим базам относятся центры, осевые линии, оси
симметрии.
Свободная база — база, относительно которой
координируется геометрическая форма детали.
Установочная база — база ориентации детали
относительно координатной плоскости XOY.
Направляющая база — база ориентации детали
относительно координатной плоскости ZOY.
Упорная база — база ориентации детали
относительно координатной плоскости ZOX.
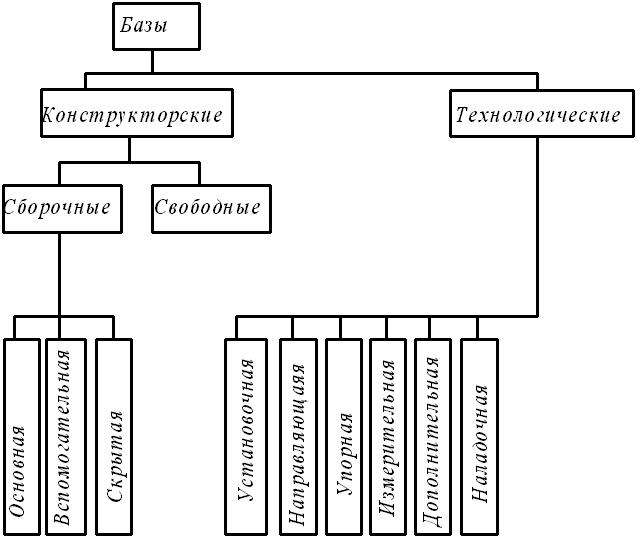
Измерительная база — база, от которой
производится измерение расстояний от других элементов детали.
Дополнительная база—база (поверхность), которая
вводится технологом на деталь с целью удобства обработки.
Наладочная база — база, от которой производится
наладка станка и инструмента. От удачного выбора баз в большой мере зависит
качество обработки и себестоимость изготовления деталей.
На рисунке 6.2 показан пример определения
конструкторских и технологических баз.

Просмотреть ближе
а — пример определения конструкторских баз;
б — схема расположения цилиндра относительно трех координатных
плоскостей
Рисунок 6.2 - Нахождение баз
Приступая к простановке размеров, необходимо
иметь ясное представление, от каких поверхностей целесообразнее проставлять на
чертеже детали сопряженные и свободные размеры. В настоящее время существуют три
системы простановки размеров:
а) от конструкторских баз; б) от технологических
баз; в) комбинированная.
Выбор системы простановки размеров относится к
одному из самых сложных этапов работы конструктора. Это объясняется главным
образом наличием большого количества совместно решаемых конструктивных и
технологических задач. Конструктор должен помнить, что насколько удачно и
технически обоснованно будет выбрана та или другая система простановки размеров,
настолько просто или сложно будет протекать процесс изготовления детали. Система
простановки размеров от конструкторских баз характеризуется тем, что все размеры
на чертеже проставляют от поверхностей, которые определяют положение детали в
собранном и работающем механизме. В этом случае конструктор не связывает
простановку размеров с вопросами изготовления детали и координированием размеров
добивается осуществления идеи работы детали в механизме. Система простановки
размеров от конструкторских баз имеет достоинства и недостатки. К достоинствам
следует отнести наличие в чертежах коротких размерных цепей, что значительно
повышает точность и качество изделия. По размерам, заданным от конструкторских
баз, легко производить проверку, расчет и увязку размеров как в детали, так и в
механизме. Длительность годности чертежа значительно повышается, так как в нем
не отражены требования часто меняющейся технологии. К недостаткам системы
следует отнести отсутствие учета технологических требований. В связи с этим
чертеж часто не отражает требований технологии изготовления детали и технологам
приходится составлять технологические чертежи на сложные детали, что ведет к
увеличению технической документации. Ряд размеров приходится пересчитывать и
назначать более жесткие допуски на них. Возрастает количество измерительного
инструмента, так как заказчик принимает изготовленные детали не по
технологическому, а по конструктивному чертежу. Перечисленные недостатки этой
системы заметно увеличивают сроки освоения изделия и его себестоимость.
Стандартом 2.307—68 предусмотрено, что на
рабочих чертежах деталей размеры, определяющие расположение сопрягаемых
поверхностей, должны быть проставлены, как правило, от конструкторских баз с
учетом возможности их выполнения и контроля.
Система простановки размеров от технологических
баз характеризуется тем, что все размеры на чертеже проставляются от
поверхностей, которые определяют положение детали при обработке. В этом случае
конструктор связывает простановку размеров с вопросами изготовления детали и
подчиняет координирование размеров требованиям технологии обработки. Эта система
имеет свои достоинства и недостатки. Главным достоинством системы является
отражение в простановке размеров производственных требований, что заметно
облегчает изготовление деталей в производстве. Так как простановка размеров
осуществляется от технологических баз, то необходимость в пересчете размеров, а
значит, и в получении более точных размеров отпадает. Заданные чертежом допуски
используются полностью, так как они одинаковые и в чертеже, и в технологии.
Конструкция приспособлений, режущего и измерительного инструмента заметно
упрощается, наблюдается сокращение количества операций и технической
документации. При этой системе простановки размеров процесс изготовления детали
и работы по приемке ОТК и заказчиком производят по одному и тому же чертежу.
К недостаткам системы следует отнести некоторую
осложненность в проверке и увязке размеров как в детали, так и в самом изделии.
Сокращается и длительность срока службы чертежа, так как чертеж часто
корректируется и следует за непрерывно изменяющейся технологией. При этой
системе простановки размеров конструктивные требования отражаются в меньшей
степени, чем технологические, что является также существенным недостатком
системы. При совпадении конструкторской и технологической баз получение
необходимой точности достигается наиболее просто и экономично.
Комбинированная система простановки размеров
характеризуется тем, что одна часть размеров проставляется от конструкторских, а
другая — от технологических баз, при этом от конструкторских баз стремятся
проставить ограниченное количество размеров. К ним относятся главным образом те,
которые входят в размерные цепи и влияют на качество работы детали и механизма в
целом. Остальные размеры, удовлетворяя требованиям производства, проставляют от
технологических баз. При такой простановке размеров сочетаются первые две
системы.
Практика разработки чертежей деталей показывает,
что от конструкторских баз приходится проставлять сравнительно небольшое
количество размеров, которое не превышает 15 % общего числа размеров детали. Для
обеспечения хороших эксплуатационных качеств детали эти размеры сопровождаются
относительно жесткими допусками. В этом случае технолог, зная обоснованность
простановки размеров от конструкторских баз и обоснованность жестких допусков,
сознательно идет на усложненный технологический процесс. Большая часть размеров
проставляется от технологических баз с достаточно широкими допусками, чтобы не
вызывать производственных трудностей при их обеспечении. Размеры на чертеже
должны быть проставлены так, чтобы они могли не только гарантировать хорошие
эксплуатационные качества детали, но и отвечать требованиям наиболее
рациональной обработки детали. Эти требования не может выполнить первая или
вторая системы в отдельности. Выполнение их может обеспечить только
комбинированная система простановки размеров. Однако для целесообразного
координирования размеров еще недостаточно определить только группы размеров,
которые должны быть проставлены от конструкторских или технологических баз.
Необходимо также иметь отчетливое представление о методах простановки размеров.
В практической работе конструкторы применяют три
метода простановки размеров, которые по характеру расположения размеров на
чертеже разделяются на цепной, координатный и комбинированный.
При цепном методе размеры проставляются
последовательно — цепью. На рисунке 6.3, а показаны примеры простановки размеров по
цепному методу. При такой простановке размеров каждая ступень (например, валика)
обрабатывается самостоятельно и в определенной последовательности. Сначала
обрабатывается размер 20H14 от базы А, затем размеры 30H14, 28h12 и т. д. При такой
последовательности обработки на точность каждого размера влияют только
технологические ошибки, возникающие при выполнении данной операции. Ошибки
предыдущих размеров на точность выполняемого размера не влияют. Это — основное
достоинство цепного метода простановки размеров. Однако расстояние какого-либо
буртика валика от любой выбранной базы (например, базы А) зависит от суммы
ошибок предыдущих размеров. Например, ошибка на размер от торца В до торца А
определяется суммой ошибок размеров 20h12 и 30h12, а ошибка на размер от торца Д
до торца А определяется уже суммой ошибок размеров: 20h12, 30h12 и 30H9. Это —
главный недостаток данного метода простановки размеров. Цепной метод часто
применяется в машиностроении при простановке размеров: на межосевые расстояния,
в ступенчатых деталях, где требуется получить очень точные размеры ступеней, при
обработке деталей комплектом режущего инструмента и т. д.

Просмотреть ближе
Рисунок 6.3 - Примеры простановки размеров по цепному, координатному и
комбинированному методам
При координатном методе размеры проставляются от
одной заранее выбранной базы. Точность выполнения любого размера зависит от
технологических ошибок, возникающих при выполнении данной операции, и не зависит
от точности выполнения других размеров, что является достоинством метода.
Координатный метод часто используется конструкторами для точного фиксирования
серии размеров от одной заранее выбранной базы. Выполняя простановку размеров,
конструктор должен помнить, что точность размера детали, заключенного между
двумя соседними координатными размерами, зависит от суммы ошибок двух этих
размеров. Например, точность размера г (рисунке 6.3, б) определяется суммой ошибок
размеров 66h12 и 38h12, а точность размера д — суммой ошибок размеров 96H14 и 66h12.
Поэтому, если требуется выдержать точные размеры между центрами или между
уступами валика и т. д., то координатный метод простановки размеров может
оказаться неприемлемым. В этом случае более точный результат можно получить при
цепном методе простановки размеров.
Комбинированный метод простановки размеров
представляет собой сочетание цепного и координатного методов. Этот метод
простановки размеров конструктор применяет с целью получения меньших ошибок в
более ответственных размерах детали. На рисунке 6.3, в показаны примеры простановки
размеров по комбинированному методу.
Возникает вопрос, какому из трех методов при
простановке размеров следует отдать предпочтение. Перед простановкой размеров
конструктор должен изучить назначение детали в механизме, составить и рассчитать
размерные цепи, выявить основные и свободные размеры и ясно представить себе
технологию обработки детали. Только после такого анализа можно безошибочно
выбрать один из указанных методов простановки размеров. В практике наиболее
распространенным является комбинированный метод простановки размеров.
|